Brazing is a metal-joining process that involves the use of a filler metal with a melting point above 450°C (842°F) but below the melting point of the base metals being joined. Unlike welding, where the base metals are melted, brazing relies on capillary action to distribute the filler metal between closely fitted surfaces of the base metals. The process creates a strong, durable bond without significantly altering the properties of the base metals. Brazing is widely used in industries such as automotive, aerospace, and HVAC due to its ability to join dissimilar metals and produce leak-tight joints.
Key Points Explained:
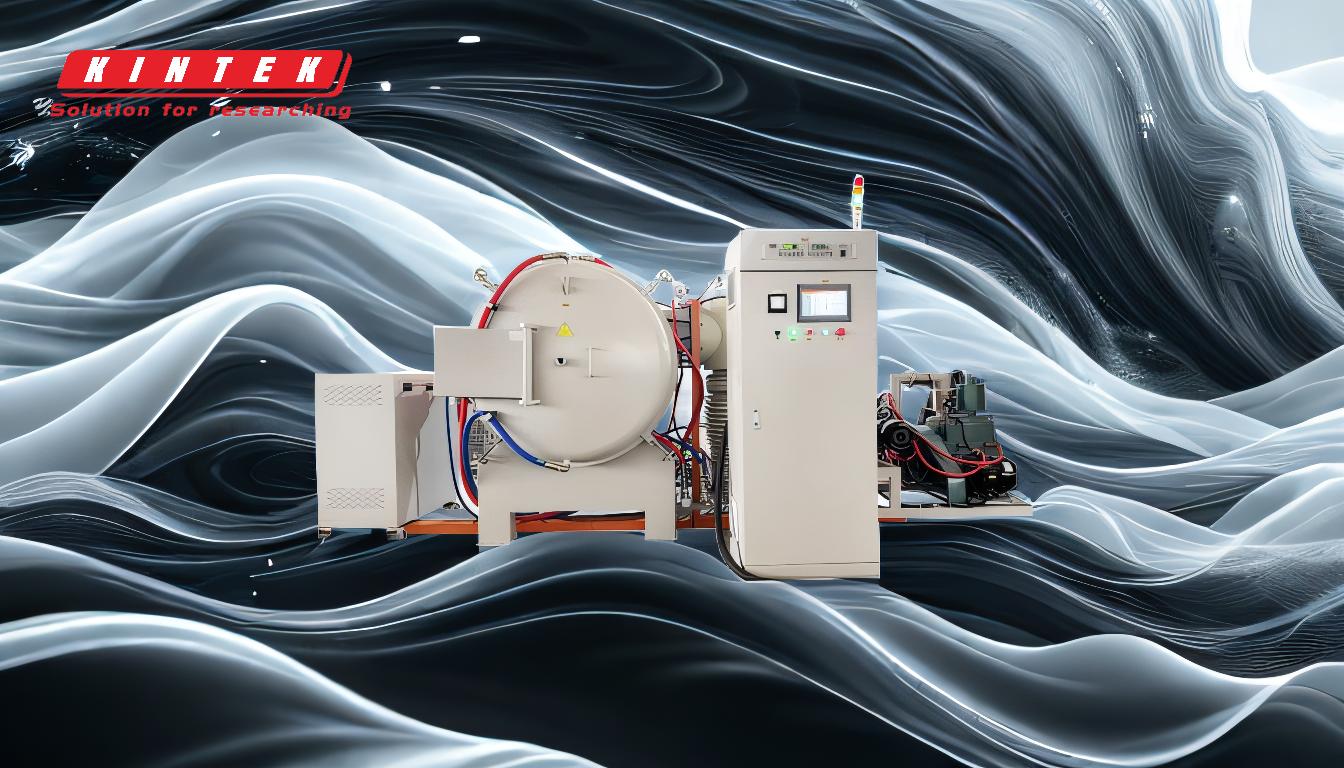
-
Definition of Brazing:
- Brazing is a metal-joining process that uses a filler metal to bond two or more base metals. The filler metal has a lower melting point than the base metals, allowing it to flow into the joint by capillary action without melting the base metals.
- This process is distinct from welding, where the base metals are melted to form the joint. Brazing is also different from soldering, which uses filler metals with melting points below 450°C (842°F).
-
Types of Bonds in Brazing:
- Metallurgical Bond: The primary bond in brazing is a metallurgical bond, where the filler metal forms a solid solution with the base metals at the atomic level. This creates a strong, durable joint.
- Mechanical Bond: In some cases, the joint may also have a mechanical bond due to the interlocking of the filler metal with the surface irregularities of the base metals. However, the primary strength of the joint comes from the metallurgical bond.
-
Capillary Action:
- Capillary action is a critical aspect of brazing. It allows the molten filler metal to flow into the narrow gaps between the base metals, ensuring a uniform and strong joint. The success of capillary action depends on the cleanliness of the surfaces, the fit-up of the joint, and the wetting characteristics of the filler metal.
-
Advantages of Brazing:
- Joining Dissimilar Metals: Brazing can join metals with different compositions, such as copper to steel or aluminum to stainless steel, which is difficult to achieve with welding.
- Minimal Distortion: Since the base metals do not melt, brazing causes minimal distortion or warping, making it suitable for precision components.
- Leak-Tight Joints: Brazed joints are often used in applications requiring leak-tight seals, such as in refrigeration and plumbing systems.
- Versatility: Brazing can be performed on a wide range of metals and alloys, and it is suitable for both small and large-scale production.
-
Common Applications:
- Automotive Industry: Brazing is used to join components such as heat exchangers, radiators, and fuel lines.
- Aerospace Industry: The process is employed in the manufacture of turbine blades, engine components, and structural assemblies.
- HVAC Systems: Brazing is widely used in the fabrication of air conditioning and refrigeration systems, where leak-tight joints are essential.
- Electronics: In the electronics industry, brazing is used to join components that require high thermal and electrical conductivity.
-
Brazing Techniques:
- Torch Brazing: A common method where a gas torch is used to heat the joint and melt the filler metal. This technique is suitable for small-scale or repair work.
- Furnace Brazing: Used for high-volume production, where parts are heated in a controlled atmosphere furnace. This method ensures consistent quality and is ideal for complex assemblies.
- Induction Brazing: This technique uses electromagnetic induction to heat the joint. It is fast and precise, making it suitable for high-precision applications.
- Dip Brazing: Parts are immersed in a molten salt or metal bath to achieve brazing. This method is often used for joining large or complex assemblies.
-
Filler Metals and Fluxes:
- Filler Metals: Common filler metals used in brazing include silver-based alloys, copper-based alloys, and aluminum-based alloys. The choice of filler metal depends on the base metals and the application requirements.
- Fluxes: Fluxes are used to clean the surfaces of the base metals and prevent oxidation during the brazing process. They also improve the wetting and flow of the filler metal. Common fluxes include borax, boric acid, and fluorides.
-
Surface Preparation:
- Proper surface preparation is crucial for successful brazing. The surfaces to be joined must be clean and free of oxides, oils, and other contaminants. Mechanical cleaning, chemical cleaning, or a combination of both may be used to prepare the surfaces.
-
Joint Design:
- The design of the joint plays a significant role in the strength and quality of the brazed joint. Common joint designs include lap joints, butt joints, and T-joints. The joint must be designed to allow proper capillary action and ensure adequate filler metal distribution.
-
Post-Brazing Treatment:
- After brazing, the joint may undergo post-brazing treatments such as heat treatment, cleaning, or inspection to ensure the quality and integrity of the joint. These treatments help to remove any residual flux, improve mechanical properties, and verify the joint's performance.
In summary, brazing is a versatile and reliable metal-joining process that creates strong, durable bonds through metallurgical bonding and capillary action. Its ability to join dissimilar metals, produce leak-tight joints, and minimize distortion makes it a preferred choice in many industries. Proper surface preparation, joint design, and the use of appropriate filler metals and fluxes are essential for achieving high-quality brazed joints.
Summary Table:
Aspect | Details |
---|---|
Primary Bond Type | Metallurgical bond (filler metal forms a solid solution with base metals) |
Secondary Bond Type | Mechanical bond (interlocking of filler metal with surface irregularities) |
Key Process | Capillary action distributes filler metal between closely fitted surfaces |
Advantages | Joins dissimilar metals, minimal distortion, leak-tight joints, versatile |
Common Applications | Automotive, aerospace, HVAC, electronics |
Filler Metals | Silver-based, copper-based, aluminum-based alloys |
Fluxes | Borax, boric acid, fluorides |
Need expert advice on brazing for your project? Contact us today to get started!