The type of furnace used to melt raw metal depends on the specific application, scale, and desired throughput. For industrial metal smelting, the most common furnaces are electric arc furnaces and induction melting furnaces. Electric arc furnaces use an electric arc to generate intense heat, making them suitable for large-scale melting of metals like steel. Induction furnaces, on the other hand, use electromagnetic induction to heat and melt metals, offering precise temperature control and efficiency, making them ideal for smaller-scale or specialized applications. Both types are widely used in industrial settings due to their ability to handle high temperatures and large volumes of raw metal.
Key Points Explained:
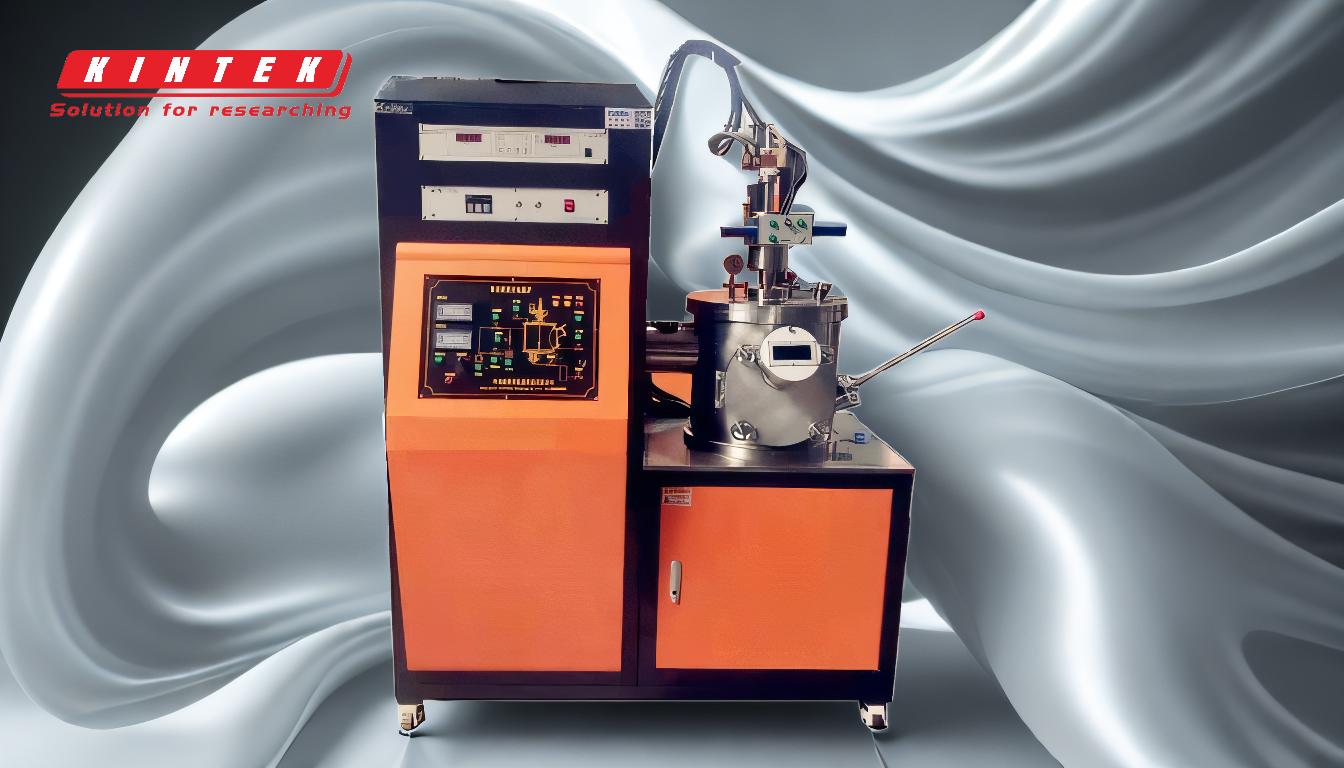
-
Electric Arc Furnaces (EAFs):
- How They Work: Electric arc furnaces generate heat through an electric arc formed between electrodes and the metal. This arc produces temperatures high enough to melt raw metals like steel, iron, and alloys.
- Applications: EAFs are commonly used in large-scale industrial settings, particularly in steel production. They are favored for their ability to recycle scrap metal efficiently.
-
Advantages:
- High throughput and capacity for large volumes.
- Ability to use recycled scrap metal as raw material.
- Flexibility in producing a wide range of steel grades.
-
Limitations:
- High energy consumption.
- Requires significant infrastructure and maintenance.
-
Induction Melting Furnaces:
- How They Work: Induction furnaces use electromagnetic induction to generate heat within the metal itself. A coil carrying alternating current creates a magnetic field, inducing eddy currents in the metal, which heats and melts it.
- Applications: These furnaces are ideal for smaller-scale operations, precision melting, and specialized applications such as foundries and laboratories.
-
Advantages:
- Precise temperature control, which is critical for alloying and refining.
- Energy-efficient and environmentally friendly, with minimal emissions.
- Compact design, making them suitable for smaller facilities.
-
Limitations:
- Limited capacity compared to EAFs, making them less suitable for large-scale industrial production.
- Higher initial cost due to the complexity of the electromagnetic system.
-
Comparison of Electric Arc and Induction Furnaces:
- Scale: Electric arc furnaces are better suited for large-scale industrial operations, while induction furnaces are ideal for smaller-scale or specialized applications.
- Energy Efficiency: Induction furnaces are generally more energy-efficient, but EAFs have the advantage of handling larger volumes.
- Material Flexibility: Both types can handle a variety of metals, but EAFs are particularly effective for steel and iron, while induction furnaces excel with non-ferrous metals like aluminum and copper.
- Cost: Induction furnaces have higher upfront costs but lower operational costs, whereas EAFs require significant infrastructure and maintenance.
-
Other Furnace Types (Contextual Information):
- While the focus is on melting furnaces, it’s worth noting other furnace types mentioned in the references, such as rotary drum furnaces, roller hearth kilns, and pusher slab kilns. These are typically used for sintering and heat treatment rather than melting.
- Belt furnaces are used for lower-temperature processes and are not suitable for the high temperatures required for metal melting.
- Continuous furnaces (e.g., pusher-plate furnaces) are common in powder metallurgy and high-throughput industrial applications but are not typically used for melting raw metal.
-
Factors Influencing Furnace Selection:
- Production Volume: Large-scale operations favor electric arc furnaces, while smaller or specialized operations may opt for induction furnaces.
- Material Type: The type of metal being melted (ferrous vs. non-ferrous) influences the choice of furnace.
- Energy Efficiency and Environmental Impact: Induction furnaces are more energy-efficient and produce fewer emissions, making them a preferred choice for environmentally conscious operations.
- Precision Requirements: Induction furnaces offer better temperature control, which is crucial for applications requiring precise alloying or refining.
In summary, the choice of furnace for melting raw metal depends on the specific requirements of the operation, including scale, material type, and desired throughput. Electric arc furnaces are the go-to for large-scale industrial metal smelting, while induction furnaces are preferred for smaller-scale, precise, or specialized applications. Both types play a critical role in modern metal processing, each with its unique advantages and limitations.
Summary Table:
Feature | Electric Arc Furnace (EAF) | Induction Furnace |
---|---|---|
Scale | Large-scale industrial operations | Smaller-scale or specialized applications |
Energy Efficiency | High energy consumption | Energy-efficient |
Material Flexibility | Ideal for steel and iron | Excellent for non-ferrous metals |
Cost | High infrastructure and maintenance costs | Higher upfront cost, lower operational costs |
Temperature Control | Less precise | Highly precise |
Applications | Steel production, scrap metal recycling | Foundries, labs, precision melting |
Need help choosing the right furnace for your metal melting needs? Contact our experts today for personalized advice!