Overloading a hydraulic system can lead to a range of adverse effects, including excessive heat generation, pressure spikes, component wear, and potential system failure. When a hydraulic system is overloaded, it operates beyond its designed capacity, which can cause the hydraulic fluid to overheat, leading to reduced lubrication and increased wear on moving parts. Pressure spikes can damage seals, hoses, and other components, while the increased stress on the system can lead to premature failure of pumps, valves, and actuators. Understanding the consequences of overloading is crucial for maintaining system efficiency, safety, and longevity.
Key Points Explained:
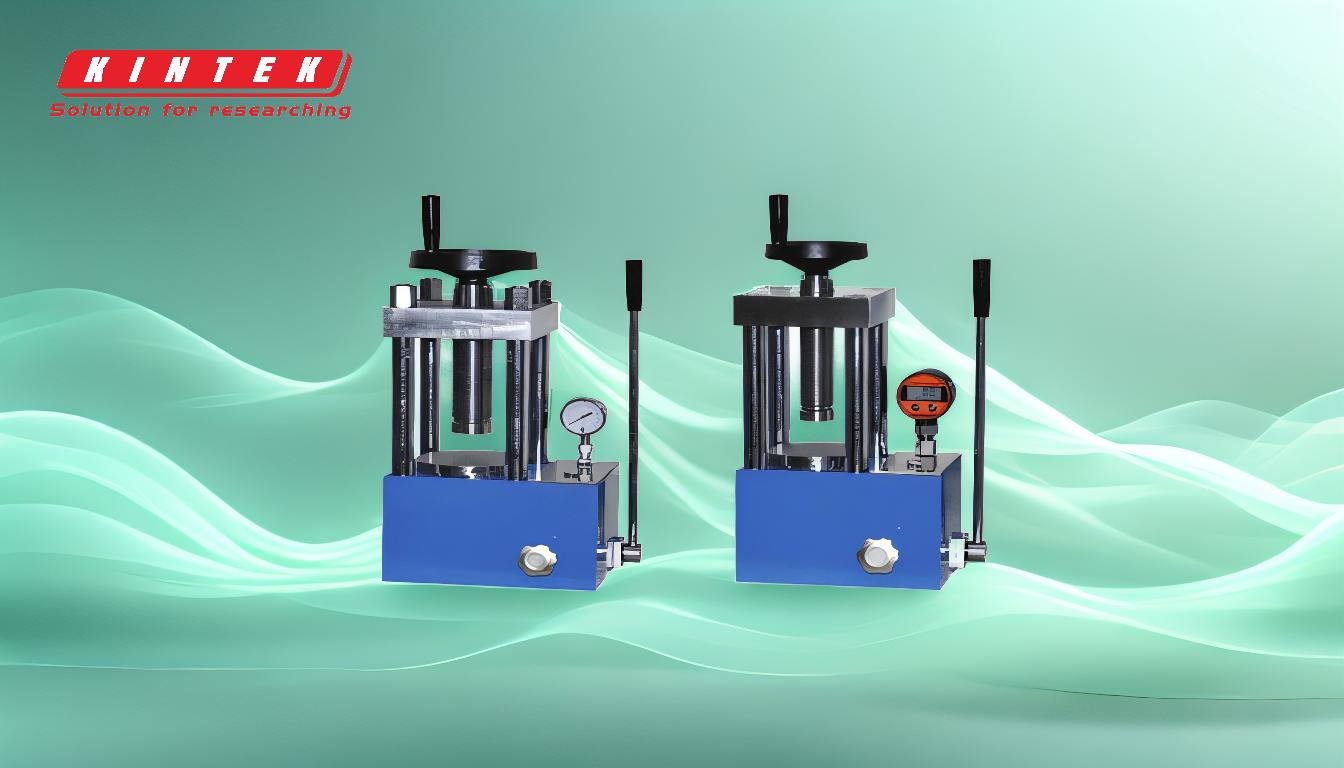
-
Excessive Heat Generation:
- Overloading a hydraulic system causes the pump to work harder, leading to increased friction and heat generation.
- Elevated temperatures can degrade the hydraulic fluid, reducing its viscosity and lubrication properties.
- This can result in accelerated wear of components such as pistons, cylinders, and seals.
- Prolonged overheating may also cause thermal expansion of components, leading to misalignment and further damage.
-
Pressure Spikes:
- When a hydraulic system is overloaded, pressure spikes can occur as the system struggles to meet the demand.
- These sudden increases in pressure can exceed the rated capacity of components, leading to burst hoses, blown seals, and damaged valves.
- Pressure spikes can also cause cavitation, where vapor bubbles form in the fluid and collapse, leading to pitting and erosion of metal surfaces.
-
Increased Wear and Tear:
- Overloading places additional stress on all components of the hydraulic system, including pumps, motors, and actuators.
- The increased load leads to faster wear of moving parts, reducing the lifespan of the system.
- Components such as bearings, gears, and seals are particularly vulnerable to premature failure under overload conditions.
-
System Inefficiency:
- An overloaded hydraulic system operates less efficiently, as more energy is required to perform the same amount of work.
- This inefficiency can lead to higher operating costs and increased energy consumption.
- The system may also experience reduced performance, such as slower operation or decreased lifting capacity.
-
Risk of Catastrophic Failure:
- In severe cases, overloading can lead to catastrophic failure of the hydraulic system.
- This could result in the sudden loss of hydraulic power, leading to equipment downtime and potential safety hazards.
- Catastrophic failure may also cause damage to surrounding equipment or pose risks to operators and nearby personnel.
-
Maintenance and Repair Costs:
- Overloading a hydraulic system increases the frequency of maintenance and the likelihood of costly repairs.
- Components that fail due to overloading may need to be replaced more frequently, increasing overall maintenance expenses.
- Downtime for repairs can also lead to lost productivity and revenue.
-
Safety Concerns:
- Overloading a hydraulic system can pose significant safety risks, especially in industrial or heavy machinery applications.
- Sudden component failure or system shutdown can lead to accidents, injuries, or even fatalities.
- Ensuring that the hydraulic system operates within its designed limits is essential for maintaining a safe working environment.
-
Preventive Measures:
- To avoid overloading, it is important to regularly monitor system pressure, temperature, and load conditions.
- Implementing pressure relief valves and load-sensing controls can help prevent overloading by automatically adjusting the system's operation.
- Regular maintenance, including fluid checks and component inspections, can help identify potential issues before they lead to overloading.
By understanding the consequences of overloading a hydraulic system and taking appropriate preventive measures, operators can ensure the system operates efficiently, safely, and reliably over its intended lifespan.
Summary Table:
Consequence | Description |
---|---|
Excessive Heat Generation | Overloading causes increased friction, overheating, and reduced fluid viscosity. |
Pressure Spikes | Sudden pressure increases can damage seals, hoses, and valves. |
Increased Wear and Tear | Faster wear of components like bearings, gears, and seals. |
System Inefficiency | Higher energy consumption and reduced performance. |
Risk of Catastrophic Failure | Sudden loss of hydraulic power, leading to downtime and safety hazards. |
Maintenance Costs | Frequent repairs and replacements increase expenses. |
Safety Concerns | Overloading poses risks of accidents and injuries. |
Preventive Measures | Monitor pressure, temperature, and load; use relief valves and regular checks. |
Protect your hydraulic system from overloading—contact our experts today for solutions and support!