Brazing and welding are two distinct methods for joining aluminum, each with unique processes, advantages, and applications. Brazing involves melting a filler metal into the joint between aluminum components without melting the base metal, while welding melts the base metal to create a metallurgical bond. Brazing is performed at higher temperatures than soldering but lower than welding, typically above 840°F, and uses stronger filler materials to create joints that are as strong as the base metals. Welding, on the other hand, requires high energy to melt the base materials, often with a filler, forming a mixed alloy. The choice between brazing and welding depends on factors like joint strength, temperature sensitivity, and application requirements.
Key Points Explained:
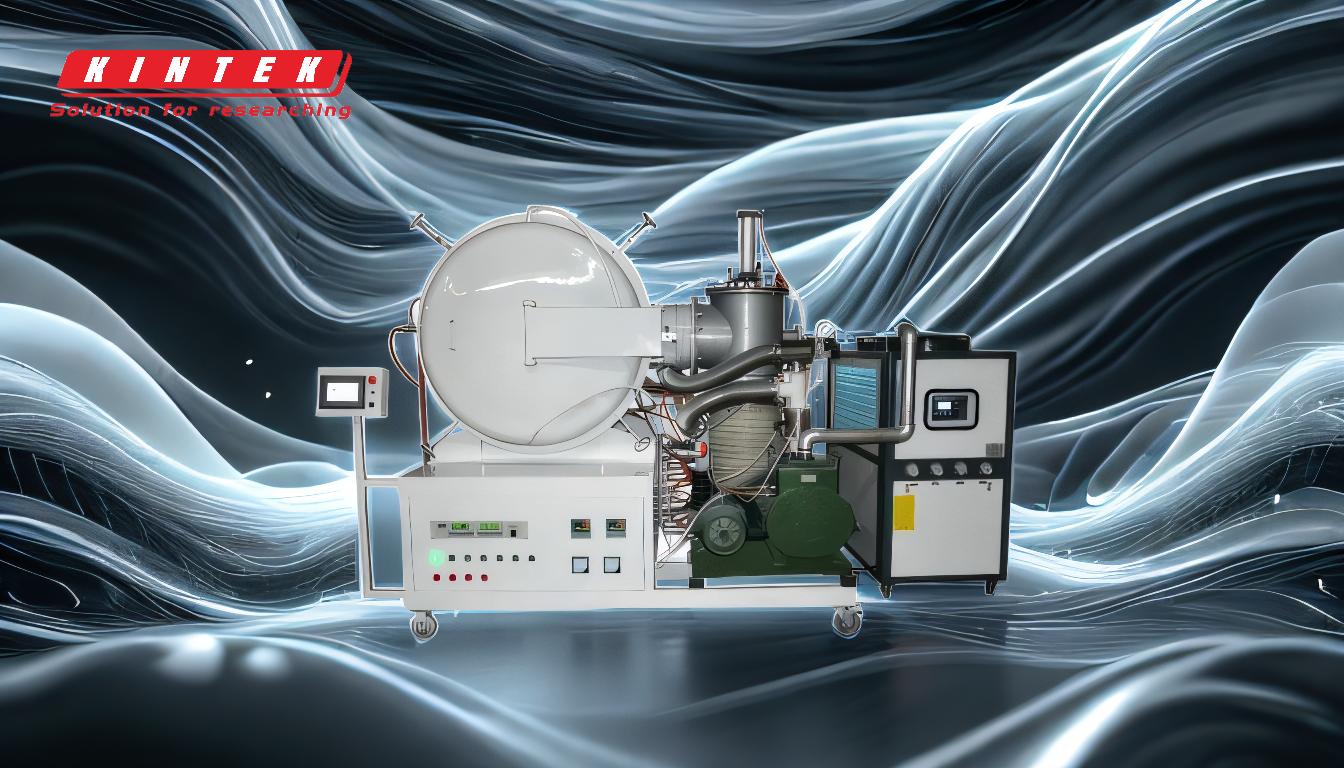
-
Definition and Process:
- Brazing: A joining process where a filler metal is melted into the joint between aluminum components without melting the base metal. The filler metal flows into the gap by capillary action, creating a strong bond. Brazing is performed at temperatures above 840°F but below the melting point of the base metal.
- Welding: A process that involves melting the base metal to create a metallurgical bond between two components. A filler material may or may not be used, and the high energy required for welding results in a mixed alloy at the joint. Welding typically occurs at much higher temperatures than brazing.
-
Temperature Requirements:
- Brazing is performed at temperatures above 840°F but below the melting point of the base metal, making it suitable for heat-sensitive applications.
- Welding requires significantly higher temperatures to melt the base metal, which can affect the material's properties and is less suitable for heat-sensitive applications.
-
Joint Strength:
- Brazed joints are as strong as the base metals, making brazing a preferred choice for applications requiring high joint strength without altering the base material's properties.
- Welded joints are typically stronger than brazed joints because the base metal is melted and fused, creating a mixed alloy. However, this can also lead to changes in the base metal's properties.
-
Filler Materials:
- Brazing uses filler materials with lower melting points than the base metal but higher than those used in soldering. These fillers are designed to create strong, durable joints.
- Welding may or may not use filler materials, depending on the process. When used, the filler material melts along with the base metal, forming a mixed alloy.
-
Applications:
- Brazing is ideal for joining aluminum in applications where heat sensitivity is a concern, such as in electronics, HVAC systems, and automotive components. It is also preferred for complex assemblies where precise control over the joint is required.
- Welding is used in applications requiring the highest joint strength, such as structural components, heavy machinery, and aerospace parts. It is also suitable for thick aluminum sections where brazing may not provide sufficient strength.
-
Advantages and Disadvantages:
-
Brazing Advantages:
- Lower heat input reduces the risk of warping or damaging the base metal.
- Suitable for joining dissimilar metals.
- Produces clean, aesthetically pleasing joints.
-
Brazing Disadvantages:
- Limited to thinner materials due to the reliance on capillary action.
- Requires precise joint preparation and fit-up.
-
Welding Advantages:
- Creates extremely strong joints, often stronger than the base metal.
- Suitable for thick materials and heavy-duty applications.
-
Welding Disadvantages:
- High heat input can alter the base metal's properties.
- More complex and requires skilled operators.
-
Brazing Advantages:
-
Equipment and Consumables:
- Brazing typically requires a torch, furnace, or induction heating equipment, along with flux and filler rods. The equipment is generally less expensive and easier to operate than welding equipment.
- Welding requires specialized equipment such as arc welders, TIG welders, or MIG welders, along with shielding gases and electrodes. The equipment is more complex and costly, requiring skilled operators.
By understanding these key differences, equipment and consumable purchasers can make informed decisions based on the specific requirements of their applications.
Summary Table:
Aspect | Brazing | Welding |
---|---|---|
Temperature | Above 840°F, below base metal melting point | High temperatures to melt base metal |
Joint Strength | As strong as base metals | Stronger than base metals (mixed alloy) |
Filler Materials | Lower melting point than base metal, stronger than soldering | May or may not use filler; melts with base metal |
Applications | Heat-sensitive (electronics, HVAC, automotive), complex assemblies | High-strength needs (structural, heavy machinery, aerospace) |
Advantages | Lower heat input, suitable for dissimilar metals, clean joints | Extremely strong joints, suitable for thick materials |
Disadvantages | Limited to thinner materials, precise joint prep required | Alters base metal properties, complex process, skilled operators needed |
Equipment | Torch, furnace, induction heating; less expensive and easier to operate | Arc, TIG, MIG welders; complex, costly, requires skilled operators |
Still unsure which method is right for your aluminum joining needs? Contact our experts today for personalized advice!