Laminating is a process used to protect and enhance documents, photos, and other materials by encasing them in a plastic film. The two primary methods of laminating are hot and cold laminating, each with distinct characteristics, applications, and advantages. Hot laminating uses heat to activate an adhesive layer, creating a strong, durable bond, while cold laminating relies on pressure-sensitive adhesives that do not require heat. The choice between the two depends on factors such as the type of material being laminated, the desired finish, and the intended use of the laminated product.
Key Points Explained:
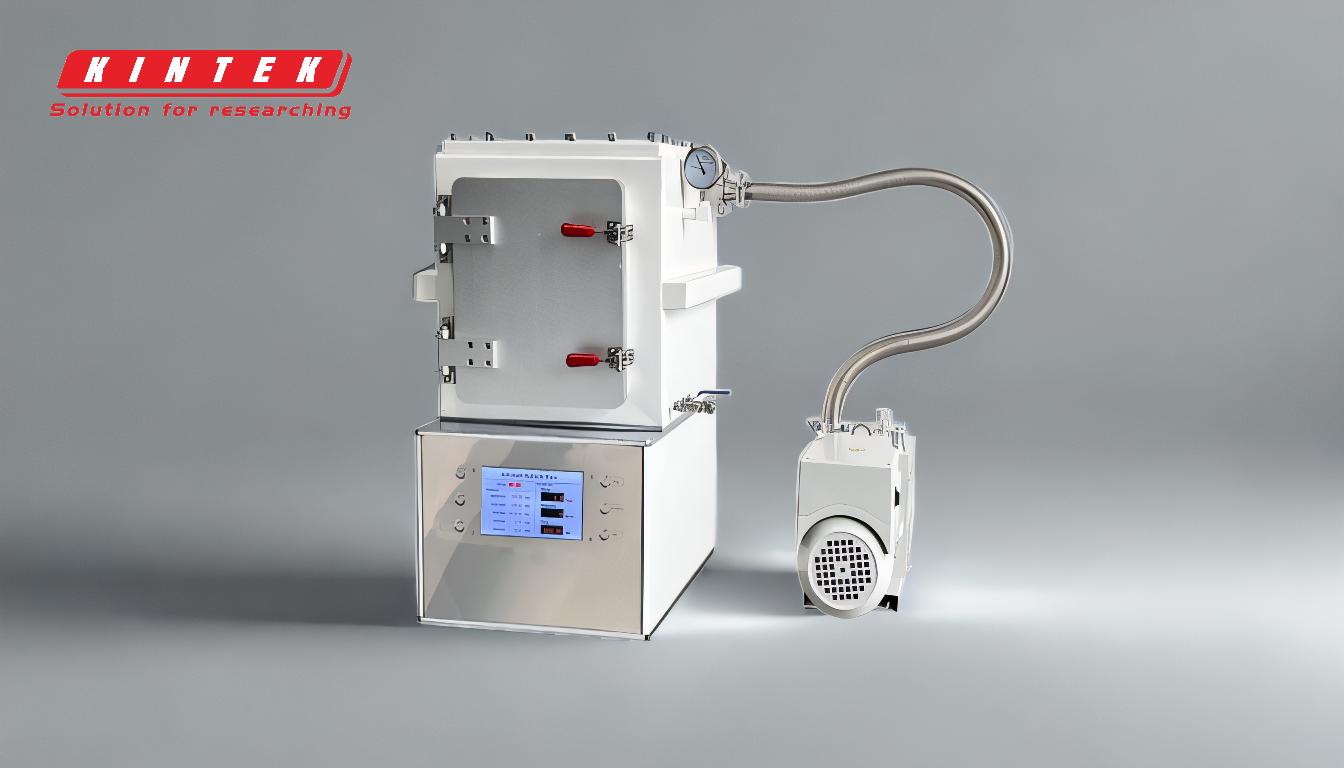
-
Mechanism of Adhesion:
- Hot Laminating: This method uses heat to activate a thermal adhesive layer on the laminating film. The heat melts the adhesive, allowing it to bond with the material being laminated. Once cooled, the adhesive solidifies, creating a strong and permanent bond.
- Cold Laminating: Cold laminating relies on pressure-sensitive adhesives that are already tacky at room temperature. When pressure is applied, the adhesive bonds to the material without the need for heat. This method is ideal for heat-sensitive materials.
-
Types of Materials Suitable for Each Method:
- Hot Laminating: Best for materials that can withstand heat, such as paper documents, posters, and photographs. It is not suitable for heat-sensitive items like thermal paper, certain plastics, or materials with ink that may smudge when exposed to heat.
- Cold Laminating: Ideal for heat-sensitive materials, including thermal paper, vinyl, and certain types of photographs. It is also suitable for materials that may warp or degrade under heat.
-
Durability and Finish:
- Hot Laminating: Provides a more durable and rigid finish, making it suitable for items that will be handled frequently or exposed to harsh conditions. The heat-sealed bond is strong and resistant to peeling.
- Cold Laminating: Offers a more flexible finish, which can be advantageous for items that need to be bent or rolled, such as banners or signs. However, the bond may not be as strong as hot laminating, and the finish may be less rigid.
-
Ease of Use and Equipment:
- Hot Laminating: Requires a laminating machine that can generate and regulate heat. These machines are typically more expensive and require more maintenance than cold laminators. The process also takes longer due to the heating and cooling phases.
- Cold Laminating: Uses simpler equipment that does not require heating elements, making the machines generally less expensive and easier to maintain. The process is faster since it does not involve heating or cooling.
-
Applications and Use Cases:
- Hot Laminating: Commonly used for creating durable items like ID cards, menu boards, and educational materials that need to withstand frequent handling and environmental exposure.
- Cold Laminating: Preferred for temporary or semi-permanent applications, such as event signage, window decals, and materials that may need to be repositioned or removed later.
-
Cost Considerations:
- Hot Laminating: Generally more expensive due to the cost of the equipment and the need for thermal laminating pouches or rolls. However, the durability and professional finish may justify the higher cost for certain applications.
- Cold Laminating: More cost-effective in terms of equipment and materials. Pressure-sensitive laminating films are often less expensive than thermal films, making cold laminating a budget-friendly option for many users.
-
Environmental Impact:
- Hot Laminating: The use of heat and thermal adhesives may have a higher environmental impact, especially if the laminating machine consumes a significant amount of energy. Additionally, thermal laminating films are often not recyclable.
- Cold Laminating: Generally considered more environmentally friendly since it does not require heat, reducing energy consumption. Some cold laminating films are also recyclable, further minimizing environmental impact.
In summary, the choice between hot and cold laminating depends on the specific needs of the project, including the type of material, desired durability, and budget. Hot laminating is ideal for creating durable, long-lasting products, while cold laminating is better suited for heat-sensitive materials and temporary applications.
Summary Table:
Aspect | Hot Laminating | Cold Laminating |
---|---|---|
Mechanism of Adhesion | Uses heat to activate thermal adhesive, creating a strong, permanent bond. | Uses pressure-sensitive adhesive, ideal for heat-sensitive materials. |
Materials | Best for heat-resistant materials like paper, posters, and photos. | Ideal for heat-sensitive materials like thermal paper, vinyl, and some plastics. |
Durability & Finish | Durable, rigid finish; resistant to peeling and harsh conditions. | Flexible finish; suitable for bending or rolling but less rigid. |
Equipment | Requires heat-generating machines; more expensive and higher maintenance. | Simpler, less expensive equipment; easier to maintain. |
Applications | ID cards, menu boards, educational materials. | Event signage, window decals, temporary applications. |
Cost | Higher cost due to equipment and thermal films. | Budget-friendly; lower equipment and material costs. |
Environmental Impact | Higher energy use; thermal films often not recyclable. | More eco-friendly; no heat required; some films recyclable. |
Still unsure which laminating method is right for you? Contact our experts today for personalized advice!