When selecting a flux for brazing or braze welding, several critical criteria must be considered to ensure optimal performance and quality of the joint. These include matching the flux to the filler metal, understanding the role of flux in oxide removal and surface wetting, and considering the specific requirements of the brazing process and application. Additionally, factors such as the type of base metal, the brazing environment, and the desired joint properties play a significant role in flux selection. Proper flux selection ensures effective oxide removal, promotes capillary action, and enhances the overall strength and durability of the brazed joint.
Key Points Explained:
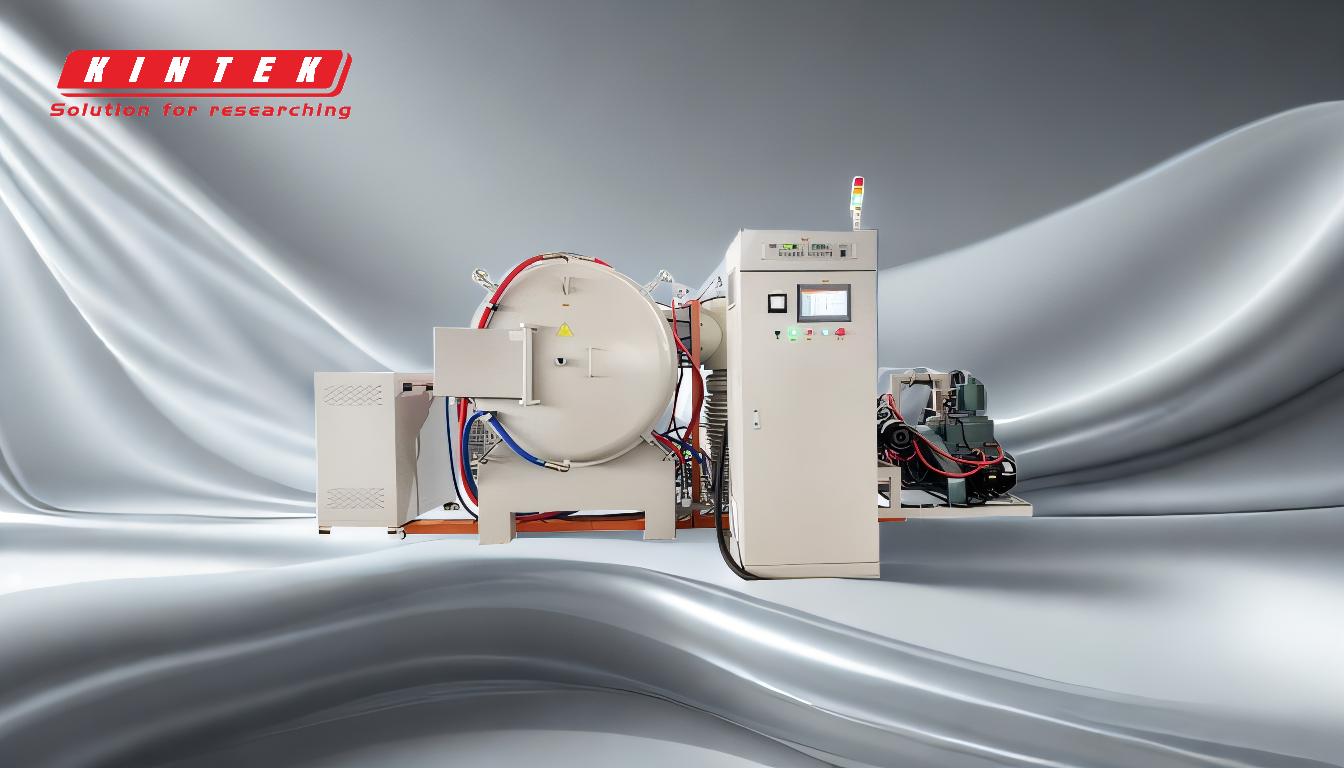
-
Matching Flux to Filler Metal:
- The flux must be compatible with the selected filler metal to ensure proper brazing performance. This compatibility ensures that the flux can effectively remove oxides and promote wetting of the surfaces by the filler metal. A mismatched flux can lead to poor joint quality, incomplete bonding, or excessive oxidation during the brazing process.
-
Role of Flux in Oxide Removal and Surface Wetting:
- Flux is essential for dissolving oxide layers on the surfaces of the materials being joined. This oxide removal is crucial for the filler metal to wet the surfaces and form a strong bond. The flux must melt before the filler metal to ensure it can perform its function effectively. After cooling, the flux forms a fine, adhesive layer that helps maintain the integrity of the joint.
-
Type of Brazing Process and Application:
- The specific brazing process and application requirements influence the choice of flux. For example, in furnace brazing, the atmosphere may remove oxides, reducing the need for flux. However, in other processes, such as torch brazing, flux is critical for oxide removal. The application's requirements, such as joint strength, corrosion resistance, and thermal stability, must also be considered when selecting a flux.
-
Base Metal and Brazing Environment:
- The type of base metal and the brazing environment are important factors in flux selection. Different base metals react differently with fluxes, and some may require specific types of flux to prevent adverse reactions. Additionally, the brazing environment, such as the presence of a protective atmosphere or vacuum, can affect the need for and type of flux used.
-
Quantity and Size of Parts:
- The quantity and size of the parts to be joined can influence the choice of flux and brazing method. For large-scale production, a flux that can be easily applied and removed may be preferred. For smaller, more intricate parts, a flux that provides precise control over oxide removal and surface wetting may be necessary.
-
Investment in Equipment:
- The required investment in brazing equipment can also impact flux selection. Some fluxes may require specialized equipment for application or removal, which can add to the overall cost. Balancing the performance requirements with the available budget is essential when selecting a flux.
By considering these criteria, you can select the most appropriate flux for your brazing or braze welding application, ensuring high-quality, durable joints that meet the specific requirements of your project.
Summary Table:
Criteria | Description |
---|---|
Matching Flux to Filler Metal | Ensure compatibility for effective oxide removal and surface wetting. |
Oxide Removal & Surface Wetting | Flux dissolves oxides, enabling strong filler metal bonds. |
Brazing Process & Application | Choose flux based on process (e.g., torch vs. furnace) and joint requirements. |
Base Metal & Environment | Select flux based on base metal type and brazing conditions (e.g., atmosphere). |
Quantity & Size of Parts | Consider flux application ease for large or intricate parts. |
Investment in Equipment | Balance flux performance with equipment costs and budget constraints. |
Need help selecting the right flux for your brazing project? Contact our experts today!