Sintering is a versatile manufacturing process used across various industries to create durable and complex parts. It is primarily employed in ceramics, powder metallurgy, and additive manufacturing. In ceramics, sintering transforms powdered materials into solid objects with enhanced strength and durability. In powder metallurgy, it is used to form metal parts by fusing metal powders without melting, making it ideal for high-melting-point metals like tungsten and molybdenum. Additionally, sintering plays a critical role in 3D printing, enabling the creation of custom metal shapes layer by layer while conserving energy. It is also used to produce sintered plastic filters and improve material properties by reducing surface porosity.
Key Points Explained:
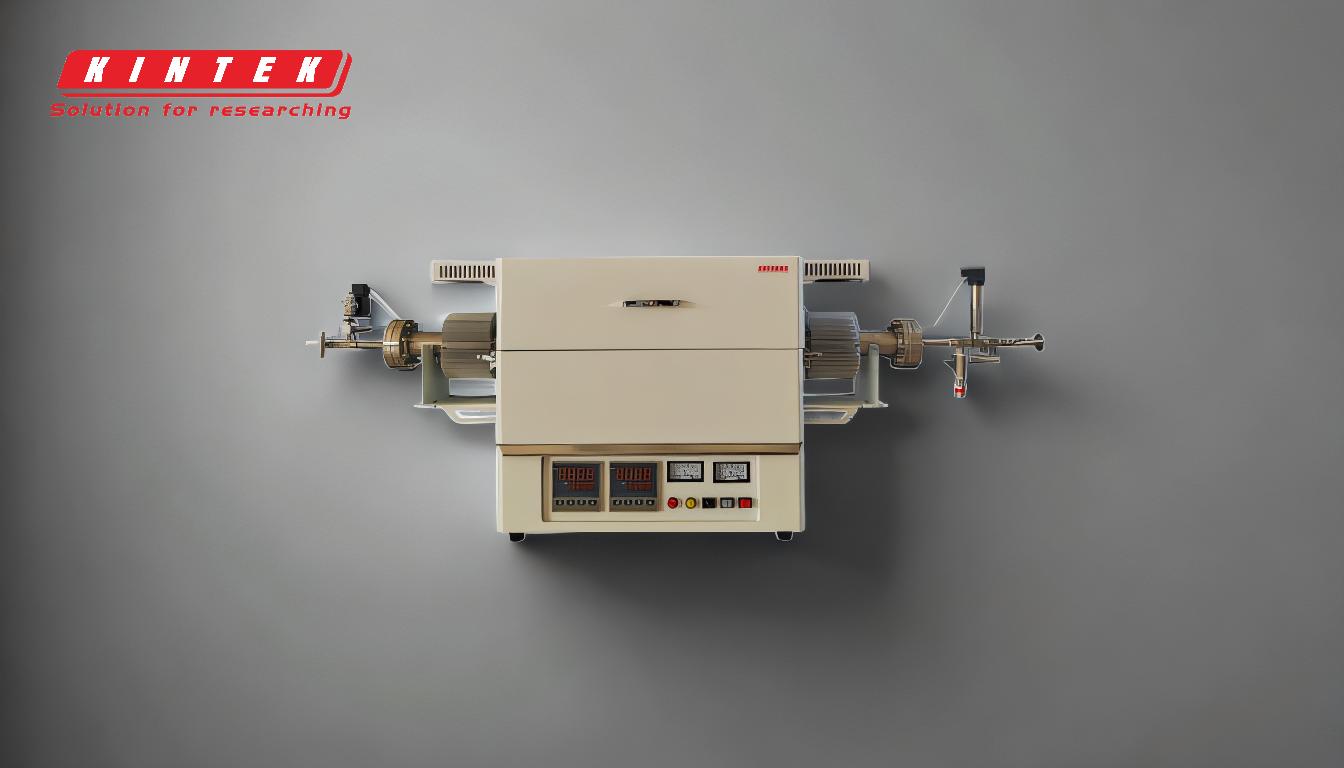
-
Ceramics Manufacturing
- Sintering is a fundamental process in ceramics production. It involves heating ceramic powders to a temperature below their melting point, causing the particles to bond and form a solid, dense structure.
- This process enhances the mechanical strength, durability, and thermal stability of ceramic products, making them suitable for applications like tiles, insulators, and advanced ceramics used in electronics and aerospace.
-
Powder Metallurgy
- Sintering is widely used in powder metallurgy to create metal parts from powdered materials.
- It is particularly beneficial for metals with high melting points, such as tungsten, molybdenum, and titanium, which are difficult to process using traditional melting methods.
- The process involves compacting metal powders into a desired shape and then heating them to bond the particles, resulting in strong, lightweight, and complex components used in automotive, aerospace, and industrial applications.
-
Additive Manufacturing (3D Printing)
- Sintering is a key technique in additive manufacturing, especially for metal 3D printing.
- It allows for the layer-by-layer creation of custom metal shapes without melting the material, which saves energy and reduces thermal stress.
- This method is ideal for producing intricate and lightweight parts with high precision, making it valuable in industries like healthcare (e.g., medical implants) and aerospace (e.g., engine components).
-
Refractory Metals and High-Temperature Applications
- Sintering is essential for processing refractory metals, such as tungsten and molybdenum, which have extremely high melting points and cannot be easily melted or cast.
- By sintering, these metals can be formed into useful shapes for applications like filaments in incandescent light bulbs, rocket nozzles, and high-temperature furnace components.
-
Surface Property Enhancement
- Sintering reduces the porosity of a material's surface, improving its density, strength, and wear resistance.
- This makes it suitable for creating components that require high durability and performance, such as bearings, gears, and filters.
-
Sintered Filters and Plastics
- Sintering is used to produce filters made from materials like sintered plastic or polyethylene (PE).
- These filters are highly porous yet strong, making them ideal for applications in water purification, air filtration, and chemical processing.
-
Energy Efficiency and Customization
- Sintering is a low-energy alternative to melting, especially for high-melting-point materials.
- It allows for the creation of custom shapes and designs with minimal material waste, making it a cost-effective and sustainable manufacturing solution.
By understanding these key applications, it becomes clear that sintering is a critical process in modern manufacturing, enabling the production of high-performance materials and components across diverse industries.
Summary Table:
Application | Key Benefits |
---|---|
Ceramics Manufacturing | Enhanced strength, durability, and thermal stability for tiles, insulators, and advanced ceramics. |
Powder Metallurgy | Ideal for high-melting-point metals like tungsten and molybdenum; creates strong, lightweight parts. |
Additive Manufacturing | Enables custom metal shapes with energy efficiency and precision for 3D printing. |
Refractory Metals | Forms high-temperature components like rocket nozzles and furnace parts. |
Surface Property Enhancement | Reduces porosity, improving density, strength, and wear resistance. |
Sintered Filters | Produces strong, porous filters for water purification and air filtration. |
Energy Efficiency | Low-energy alternative to melting, offering cost-effective and sustainable solutions. |
Learn how sintering can revolutionize your manufacturing process—contact our experts today!