Sintering is a versatile manufacturing process used across various industries to create durable and functional materials. It is traditionally associated with ceramics and powder metallurgy, where it is used to form solid objects from powdered materials. Sintering is particularly valuable for metals with high melting points, as it allows for the creation of custom metal forms without requiring full melting. Additionally, sintering plays a significant role in 3D printing, enabling the layer-by-layer construction of complex metal shapes while conserving energy. Beyond metals, sintering is also applied in the production of ceramics, glass, and even sintered plastics and filters. Its ability to reduce porosity and enhance material properties makes it a critical process in industries ranging from automotive to electronics.
Key Points Explained:
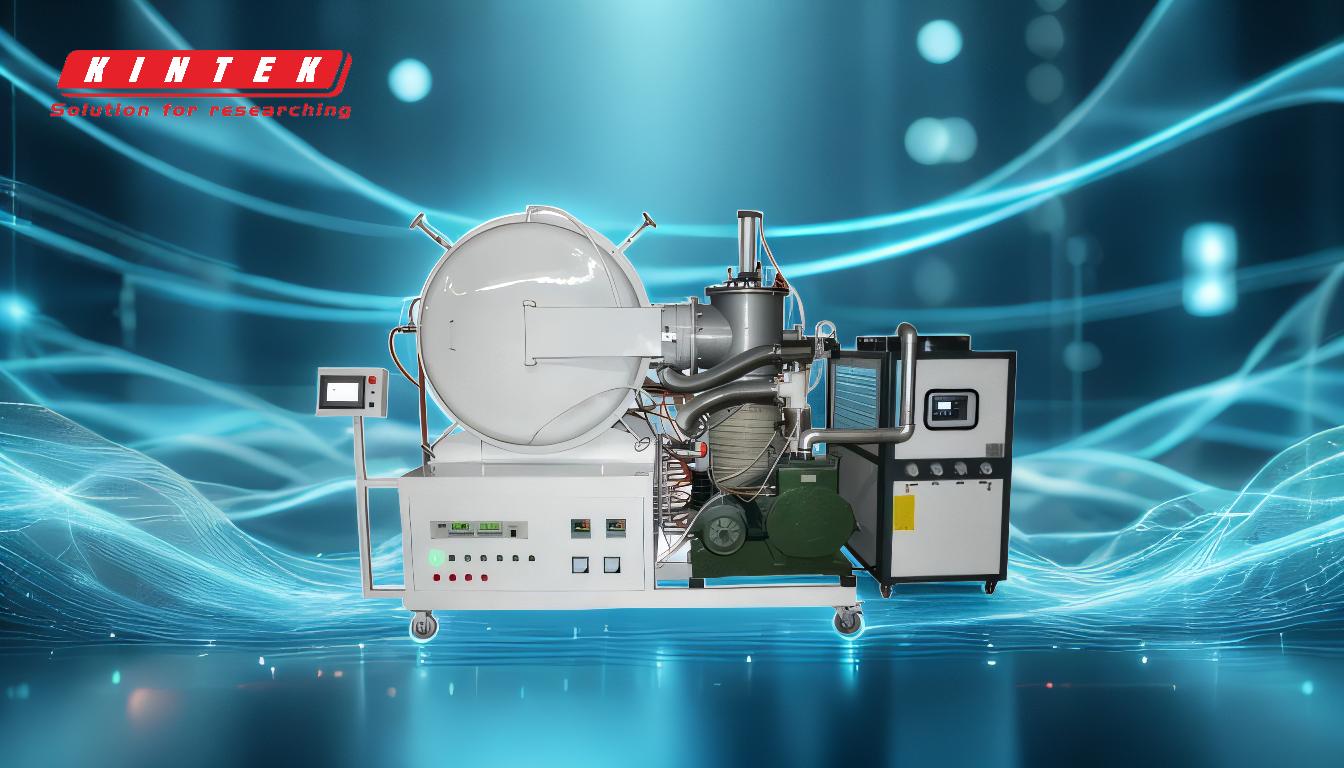
-
Traditional Use in Ceramics:
- Sintering has long been used in the production of ceramic objects. By heating powdered ceramic materials below their melting point, sintering bonds the particles together, creating a solid and durable structure. This process is essential for manufacturing items like tiles, pottery, and advanced ceramic components used in electronics and aerospace.
-
Powder Metallurgy:
- In powder metallurgy, sintering is a key step in forming metal parts from powdered metals. This method is particularly useful for metals with high melting points, such as tungsten and titanium, which are difficult to process using traditional melting techniques. Sintered metal parts are widely used in automotive, aerospace, and industrial applications due to their strength and precision.
-
3D Printing and Additive Manufacturing:
- Sintering is integral to 3D printing, especially in metal additive manufacturing. By sintering metal powders layer by layer, complex and custom metal shapes can be created without the need for high-energy melting processes. This approach is energy-efficient and allows for the production of intricate designs that would be challenging to achieve through conventional methods.
-
Reduction of Porosity:
- One of the key benefits of sintering is its ability to reduce the porosity of materials. By bonding particles together, sintering creates a denser and more uniform structure, enhancing the material's mechanical properties, such as strength, durability, and thermal conductivity. This makes sintered materials ideal for applications requiring high performance and reliability.
-
Industrial Applications:
- Sintering is used in various industrial processes, including the production of steel. For example, powdered iron mixed with coke is sintered to form lumps suitable for blast furnace operations. This step is crucial in steel manufacturing, as it improves the efficiency of the smelting process. Sintering is also employed in the production of glass and advanced ceramics.
-
Sintered Plastics and Filters:
- Beyond metals and ceramics, sintering is used to create sintered plastics and porous filters. Sintered plastic components are valued for their durability and resistance to wear, making them suitable for industrial and consumer applications. Sintered filters, often made from materials like polyethylene (PE), are used in filtration systems for their ability to trap fine particles while maintaining airflow or liquid flow.
-
Energy Efficiency:
- Sintering is an energy-efficient alternative to melting, especially for high-melting-point materials. By operating at temperatures below the material's melting point, sintering reduces energy consumption and minimizes thermal stress, making it a sustainable choice for manufacturing.
In summary, sintering is a critical process in modern manufacturing, with applications spanning ceramics, metals, 3D printing, and beyond. Its ability to create strong, precise, and energy-efficient materials makes it indispensable across a wide range of industries.
Summary Table:
Key Aspect | Description |
---|---|
Traditional Use in Ceramics | Bonds ceramic powders into durable structures, used in tiles, pottery, and aerospace components. |
Powder Metallurgy | Forms metal parts from powdered metals, ideal for high-melting-point metals like tungsten. |
3D Printing | Enables layer-by-layer construction of complex metal shapes, conserving energy. |
Reduction of Porosity | Creates denser, stronger materials by bonding particles, enhancing mechanical properties. |
Industrial Applications | Used in steel production, glass manufacturing, and advanced ceramics. |
Sintered Plastics & Filters | Produces durable plastic components and porous filters for industrial use. |
Energy Efficiency | Operates below melting points, reducing energy consumption and thermal stress. |
Learn how sintering can enhance your manufacturing process—contact our experts today!