Plastic pyrolysis is a process that converts plastic waste into valuable products like oil, gas, and char by breaking down the polymer chains at high temperatures in the absence of oxygen. Catalysts play a crucial role in enhancing the efficiency and selectivity of this process. The choice of catalyst depends on the desired end products and the specific reactions needed to achieve them. Common catalysts used in plastic pyrolysis include zeolites, biochar-based catalysts, and metal-based catalysts like titanium and gallium compounds. These catalysts help crack heavy hydrocarbons into lighter fractions, improve the quality of the pyrolysis oil, and promote the formation of valuable chemicals. Below, we explore the key catalysts used in plastic pyrolysis and their roles in the process.
Key Points Explained:
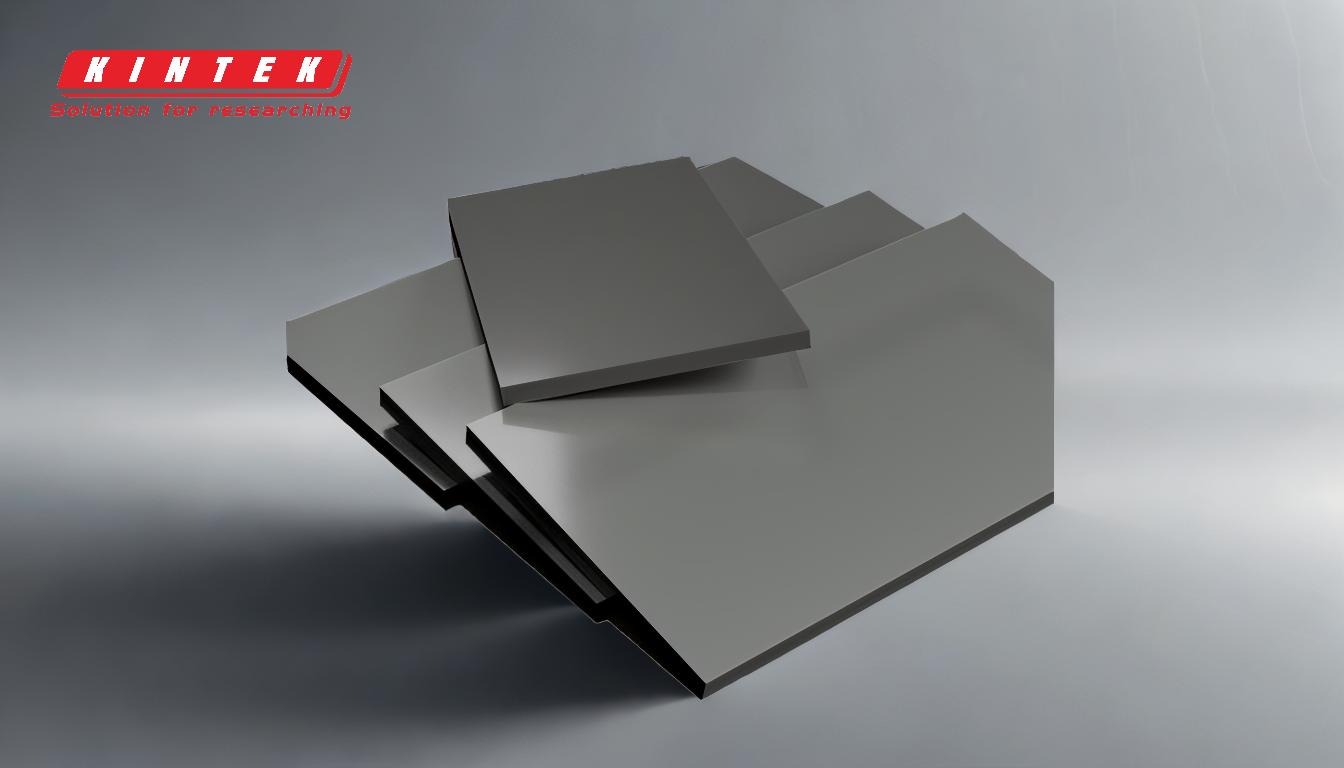
-
Zeolites as Catalysts
- Composition: Zeolites are porous materials made of aluminum and silicon oxides.
- Function: They are widely used in plastic pyrolysis due to their ability to selectively crack heavy hydrocarbons into lighter fractions like C1, C2, and C3 hydrocarbons.
-
Advantages:
- High selectivity for specific hydrocarbon products.
- Ability to condense light hydrocarbons, improving the quality of the pyrolysis oil.
- Versatility in handling different types of plastic feedstocks.
- Applications: Used in processes targeting the production of fuels and chemicals from plastic waste.
-
Biochar-Based Catalysts
- Composition: Derived from biomass, biochar-based catalysts are rich in carbon and often contain trace metals.
- Function: They promote desirable chemical reactions during pyrolysis, enhancing the yield of valuable biofuels and chemicals.
-
Advantages:
- Sustainable and environmentally friendly, as they are derived from renewable sources.
- Improve the quality of pyrolysis oil by reducing unwanted byproducts.
- Can be tailored to specific reactions by modifying their composition.
- Applications: Ideal for processes aiming to produce high-quality biofuels from plastic waste.
-
Metal-Based Catalysts (e.g., Titanium and Gallium Compounds)
- Composition: Includes compounds like titanium nitride (TiN) and gallium nitride (GaN).
- Function: These catalysts are particularly effective in promoting the production of specific chemical compounds, such as furfural, during pyrolysis.
-
Advantages:
- High activity in breaking down complex polymer structures.
- Selective promotion of desired chemical reactions.
- Suitable for processes targeting the production of specialty chemicals.
- Applications: Used in advanced pyrolysis processes for the production of high-value chemicals from plastic waste.
-
Role of Catalysts in Plastic Pyrolysis
- Cracking Heavy Hydrocarbons: Catalysts help break down long-chain polymers into smaller, more manageable hydrocarbon fractions.
- Improving Product Quality: By promoting specific reactions, catalysts enhance the quality of the pyrolysis oil, making it easier to upgrade into drop-in fuels.
- Selectivity: Different catalysts can be chosen to target specific end products, such as fuels, chemicals, or gases.
- Process Efficiency: Catalysts reduce the energy requirements and improve the overall efficiency of the pyrolysis process.
-
Catalyst Selection Criteria
- Feedstock Type: The type of plastic being pyrolyzed influences the choice of catalyst. For example, polyethylene and polypropylene may require different catalysts for optimal results.
- Desired End Products: Catalysts are selected based on whether the goal is to produce fuels, chemicals, or gases.
- Process Conditions: Temperature, pressure, and reaction time also play a role in determining the most suitable catalyst.
- Cost and Availability: Practical considerations like cost and availability of the catalyst are important for large-scale applications.
-
Challenges and Future Directions
- Catalyst Deactivation: Over time, catalysts can become deactivated due to coke formation or poisoning by impurities in the feedstock.
- Regeneration: Developing methods to regenerate or recycle catalysts is crucial for sustainable and cost-effective processes.
- Novel Catalysts: Research is ongoing to develop new catalysts with higher activity, selectivity, and durability for plastic pyrolysis.
- Integration with Other Processes: Combining pyrolysis with other technologies, such as gasification or hydrogenation, could further enhance the efficiency and versatility of the process.
In conclusion, catalysts are essential for optimizing the plastic pyrolysis process, enabling the production of high-quality fuels and chemicals from waste plastics. The choice of catalyst depends on the specific requirements of the process, including the type of plastic, desired end products, and operating conditions. Continued research and development in catalyst technology will play a key role in advancing plastic pyrolysis as a sustainable solution for plastic waste management.
Summary Table:
Catalyst Type | Composition | Function | Advantages | Applications |
---|---|---|---|---|
Zeolites | Aluminum and silicon oxides | Selectively crack heavy hydrocarbons into lighter fractions (C1, C2, C3). | High selectivity, improves oil quality, versatile for different plastics. | Production of fuels and chemicals from plastic waste. |
Biochar-Based | Carbon-rich, trace metals | Promote chemical reactions, enhance biofuel and chemical yields. | Sustainable, reduces byproducts, customizable for specific reactions. | Ideal for high-quality biofuel production. |
Metal-Based | Titanium nitride (TiN), gallium nitride (GaN) | Promote specific chemical compounds like furfural. | High activity, selective reactions, suitable for specialty chemicals. | Advanced pyrolysis for high-value chemical production. |
Ready to optimize your plastic pyrolysis process? Contact our experts today for tailored catalyst solutions!