Low-pressure casting and vacuum permanent mold casting are both advanced casting methods used in the manufacturing of high-quality metal components. Low-pressure casting involves filling a mold with molten metal using low-pressure gas, which ensures precise control over the filling process and reduces turbulence. Vacuum permanent mold casting, on the other hand, uses a vacuum to draw molten metal into the mold, minimizing air entrapment and improving the quality of the cast. The choice between the two depends on factors such as the desired material properties, production volume, and specific application requirements. Low-pressure casting is often preferred for its simplicity and cost-effectiveness, while vacuum permanent mold casting is favored for producing high-integrity, defect-free components.
Key Points Explained:
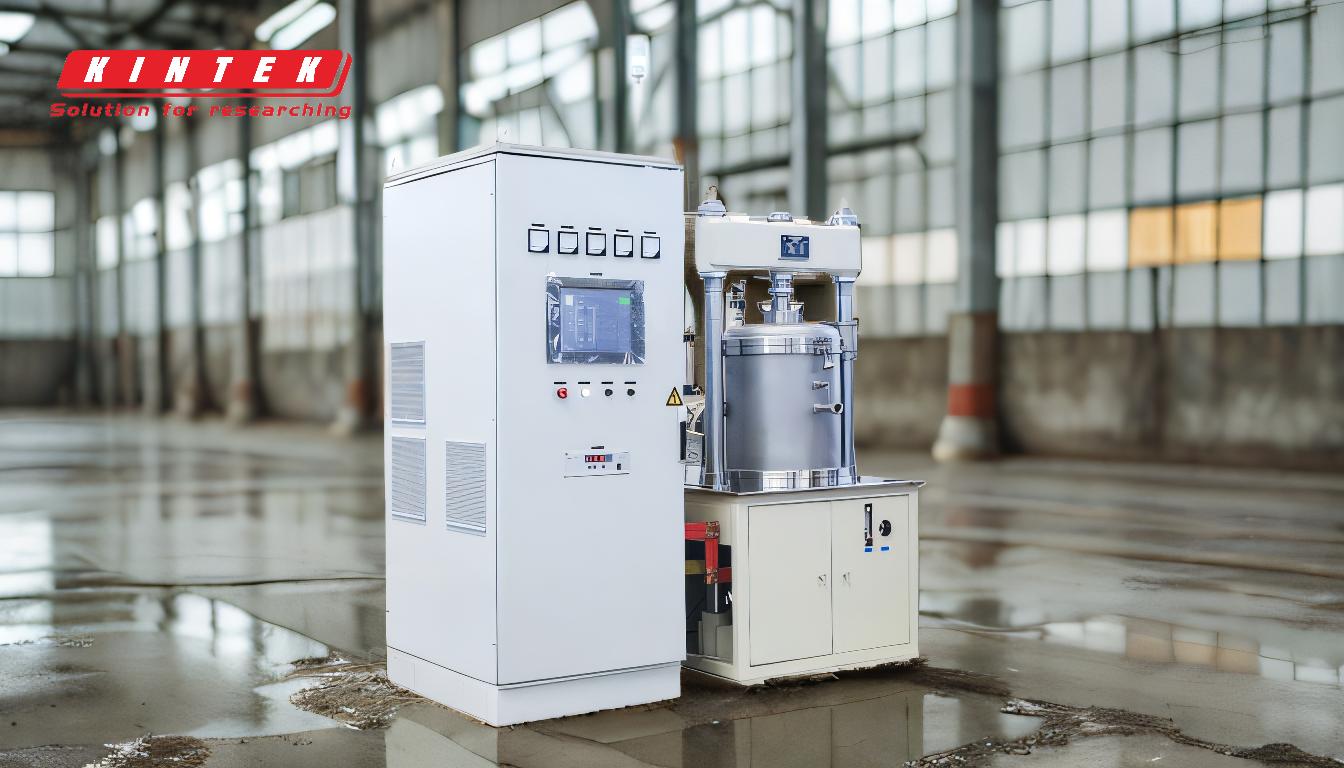
-
Process Overview:
- Low-Pressure Casting: This method uses a low-pressure gas (typically 0.5 to 1 bar) to push molten metal from a furnace into a mold. The process is controlled and gradual, reducing turbulence and minimizing the risk of defects.
- Vacuum Permanent Mold Casting: In this method, a vacuum is created in the mold cavity, which draws the molten metal into the mold. This process helps to eliminate air pockets and gas entrapment, resulting in a higher-quality cast.
-
Quality of Castings:
- Low-Pressure Casting: Produces castings with good surface finish and dimensional accuracy. However, there is a slight risk of porosity due to gas entrapment, although this is less than in traditional gravity casting.
- Vacuum Permanent Mold Casting: Known for producing castings with very low porosity and excellent mechanical properties. The vacuum ensures that the molten metal fills the mold completely, reducing the likelihood of defects.
-
Material Utilization:
- Low-Pressure Casting: Efficient use of material with minimal waste. The controlled filling process ensures that the exact amount of metal required is used.
- Vacuum Permanent Mold Casting: Also efficient in material utilization, but the vacuum process may require more precise control over the metal flow, which can sometimes lead to higher material costs.
-
Production Volume and Cost:
- Low-Pressure Casting: Generally more cost-effective for medium to high production volumes. The equipment is simpler and less expensive compared to vacuum casting systems.
- Vacuum Permanent Mold Casting: More suitable for high-integrity applications where cost is less of a concern. The equipment and process are more complex, leading to higher initial and operational costs.
-
Application Suitability:
- Low-Pressure Casting: Ideal for producing components that require good mechanical properties and surface finish but do not need the highest level of integrity. Commonly used in automotive and aerospace industries.
- Vacuum Permanent Mold Casting: Best suited for applications where the highest level of casting integrity is required, such as in critical aerospace components or medical devices.
-
Flexibility and Control:
- Low-Pressure Casting: Offers good control over the casting process, but the pressure used is relatively low, which can limit the complexity of the parts that can be cast.
- Vacuum Permanent Mold Casting: Provides excellent control over the filling process, allowing for the casting of more complex and intricate parts with fewer defects.
-
Environmental Impact:
- Low-Pressure Casting: Generally has a lower environmental impact due to lower energy consumption and simpler equipment.
- Vacuum Permanent Mold Casting: May have a higher environmental impact due to the energy required to maintain the vacuum and the complexity of the equipment.
In conclusion, the choice between low-pressure casting and vacuum permanent mold casting depends on the specific requirements of the application. Low-pressure casting is more cost-effective and suitable for a wide range of applications, while vacuum permanent mold casting offers superior quality and is ideal for high-integrity components.
Summary Table:
Aspect | Low-Pressure Casting | Vacuum Permanent Mold Casting |
---|---|---|
Process | Uses low-pressure gas to push molten metal into the mold. | Uses a vacuum to draw molten metal into the mold. |
Quality | Good surface finish, dimensional accuracy; slight risk of porosity. | Very low porosity, excellent mechanical properties, and defect-free castings. |
Material Utilization | Efficient with minimal waste. | Efficient but may require more precise control, potentially increasing material costs. |
Production Volume & Cost | Cost-effective for medium to high volumes; simpler equipment. | Higher cost due to complex equipment; ideal for high-integrity applications. |
Applications | Automotive, aerospace (good mechanical properties, surface finish). | Critical aerospace, medical devices (highest integrity requirements). |
Flexibility & Control | Good control but limited complexity for parts. | Excellent control for complex, intricate parts with fewer defects. |
Environmental Impact | Lower energy consumption, simpler equipment. | Higher energy consumption due to vacuum maintenance and complex equipment. |
Need help choosing the right casting method for your project? Contact our experts today for personalized advice!