When deciding between soldering and brazing, the choice depends on the specific requirements of the application, such as joint strength, appearance, and the materials being joined. Brazing generally offers stronger joints, with brazed joints being as strong as the base metals themselves. It is a versatile and widely used method in industries like cookware, automotive, and HVAC systems, making it ideal for applications requiring durability and reliability. Additionally, vacuum brazing ensures oxidation-free and clean-finished parts, with high joint strength and excellent consistency in appearance and size. Soldering, while suitable for less demanding applications, typically results in weaker joints compared to brazing. Therefore, brazing is often the better choice for high-strength and precision applications.
Key Points Explained:
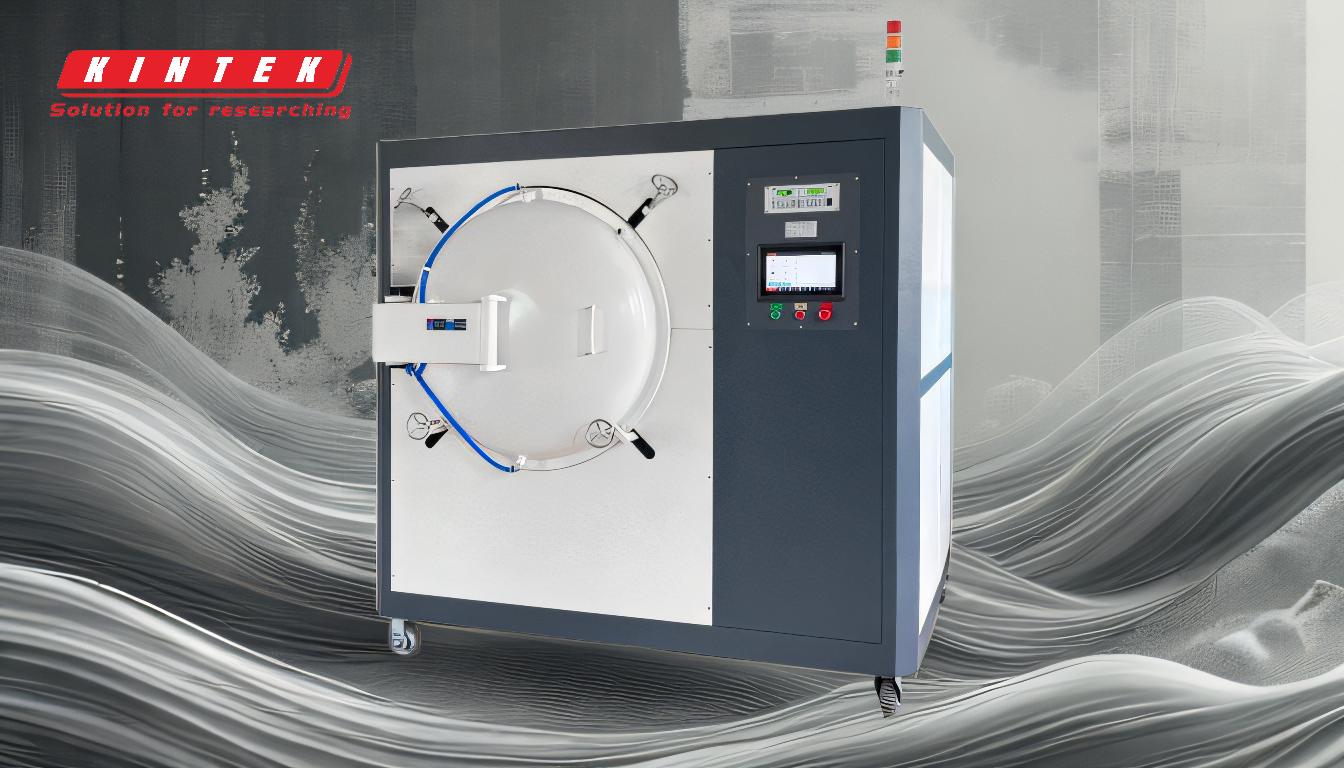
-
Joint Strength:
- Brazing produces joints that are as strong as the base metals, making it superior to soldering in terms of mechanical strength. This is particularly important in industries where durability and reliability are critical, such as automotive and HVAC systems.
-
Versatility and Industry Applications:
- Brazing is a versatile joining solution used across various industries, including cookware, automotive, and HVAC systems. Its adaptability to different materials and complex geometries makes it a preferred choice for many applications.
-
Oxidation and Clean Appearance:
- Unlike soldering, vacuum brazing keeps the finished part free from oxidation, maintaining a clean and polished appearance. This is crucial for applications where aesthetics and surface integrity are important.
-
Consistency and Precision:
- Brazed parts exhibit excellent part-to-part consistency in both appearance and size. This high level of precision is beneficial for complex joining geometries and ensures uniformity in mass production.
-
Comparison with Soldering:
- While soldering is suitable for less demanding applications, it generally results in weaker joints compared to brazing. Soldering is often used in electronics and plumbing where high joint strength is not a primary requirement.
In summary, brazing is generally the better choice for applications requiring strong, durable, and precise joints, while soldering is more appropriate for less demanding tasks where joint strength is not a critical factor.
Summary Table:
Aspect | Brazing | Soldering |
---|---|---|
Joint Strength | As strong as the base metals, ideal for high-strength applications. | Weaker joints, suitable for less demanding tasks. |
Versatility | Widely used in cookware, automotive, and HVAC systems. | Commonly used in electronics and plumbing. |
Oxidation & Appearance | Oxidation-free, clean, and polished finish with vacuum brazing. | May show oxidation, less polished appearance. |
Precision & Consistency | Excellent part-to-part consistency in appearance and size. | Less consistent, suitable for simpler geometries. |
Applications | High-strength, durable, and precise joints. | Less demanding applications where joint strength isn't critical. |
Need help choosing between soldering and brazing? Contact our experts today for tailored advice!