A sintering furnace is a critical piece of equipment used in various industrial processes, particularly in metallurgy and materials science, to bond powdered materials into a solid mass through heat and pressure. The essential parts of a sintering furnace vary depending on the type of furnace (e.g., vacuum, hydrogen, hot press, or discharge plasma sintering furnace). However, common components include the vacuum chamber, heating elements, vacuum pumps, temperature control systems, charging system, water cooling system, and control systems. These components work together to create the necessary conditions for sintering, such as high temperatures, controlled atmospheres, and precise temperature and pressure management. Understanding these components is crucial for selecting the right furnace for specific applications.
Key Points Explained:
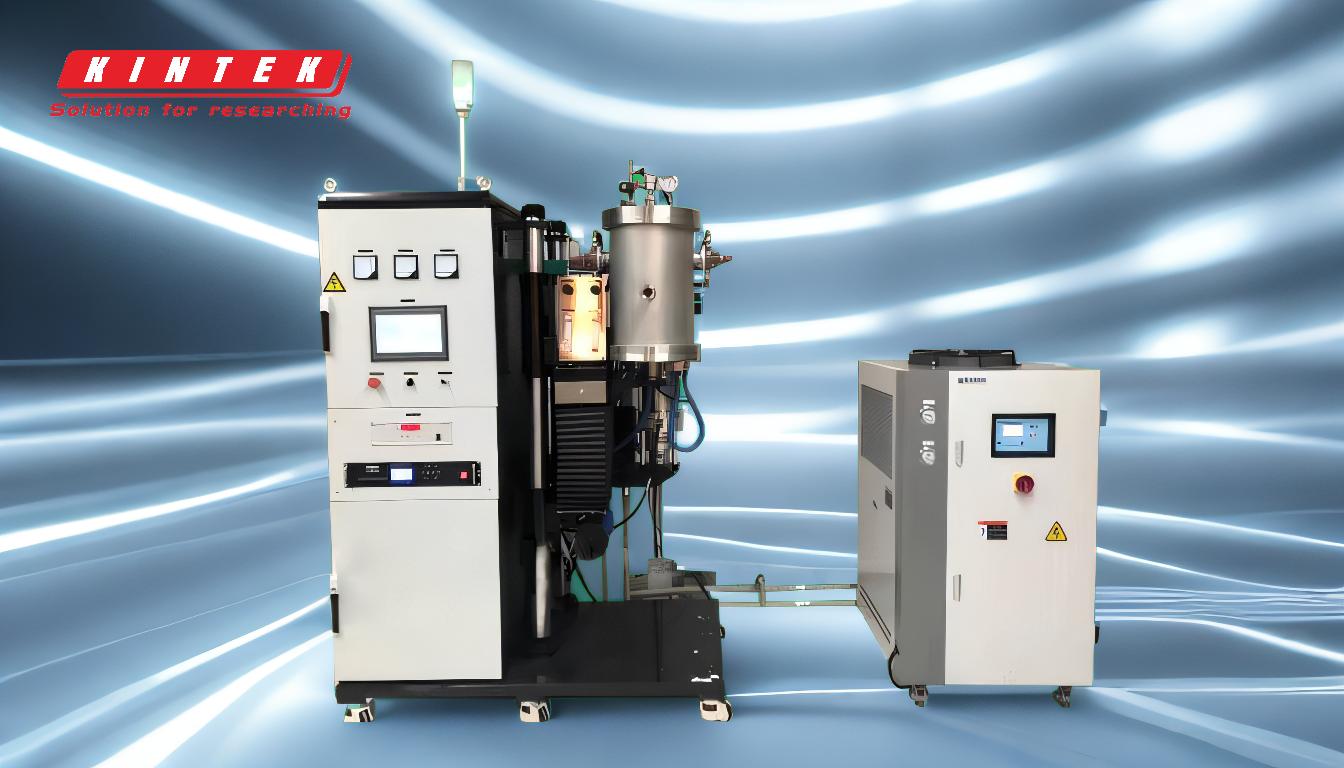
-
Vacuum Chamber:
- The vacuum chamber is a critical component designed to withstand high temperatures and vacuum conditions. It provides an environment free from contaminants, which is essential for achieving high-quality sintering results. The chamber must be robust and well-sealed to maintain the vacuum integrity during the sintering process.
-
Heating Elements:
- Heating elements are responsible for generating the high temperatures required for sintering. These elements must be capable of reaching and maintaining the desired temperatures consistently. Common materials used for heating elements include molybdenum, tungsten, and graphite, depending on the maximum temperature required.
-
Vacuum Pumps:
- Vacuum pumps are used to create and maintain the vacuum within the chamber. They remove air and other gases to prevent oxidation and contamination of the materials being sintered. The efficiency and reliability of the vacuum pumps are crucial for the overall performance of the sintering furnace.
-
Temperature Control Systems:
- Temperature control systems are essential for managing the heating and cooling rates during the sintering process. Precise temperature control ensures that the materials are sintered uniformly and to the desired specifications. These systems often include thermocouples, controllers, and software for monitoring and adjusting temperatures.
-
Charging System:
- The charging system is used for loading and unloading materials into and out of the furnace. This system must be designed to handle the specific types of materials being sintered and to operate efficiently within the high-temperature and vacuum environment of the furnace.
-
Water Cooling System:
- The water cooling system is used to cool the furnace shell and other components, such as the vacuum pumps, to prevent overheating. Effective cooling is necessary to maintain the structural integrity of the furnace and to ensure safe operation.
-
Control Systems:
- Control systems integrate all the components of the sintering furnace, allowing for automated and precise control of the sintering process. These systems include software and hardware for monitoring and controlling temperature, pressure, vacuum levels, and other critical parameters.
-
Specialized Components for Different Types of Sintering Furnaces:
- Hydrogen Sintering Furnace: Includes a furnace cover (door), bottom (head), furnace body, and electric control system. The furnace body must be designed to handle the specific requirements of hydrogen atmospheres.
- Hot Press Sintering Furnace: Features high working temperatures, high vacuum degrees, large pressure forces, and good cooling conditions. The furnace body is strongly cooled, except for the heating and heat preservation parts.
- Discharge Plasma Sintering Furnace: Includes an axial pressure device, water-cooled punch electrode, vacuum chamber, atmosphere control system, DC pulse and cooling water, displacement measurement, temperature measurement, and safety control unit. The on-off pulse power supply is the most critical component, generating discharge plasma and other necessary effects.
Understanding these essential parts and their functions is crucial for anyone involved in the selection, operation, or maintenance of a sintering furnace. Each component plays a vital role in ensuring the successful sintering of materials, and the specific requirements may vary depending on the type of furnace and the materials being processed.
Summary Table:
Component | Function |
---|---|
Vacuum Chamber | Provides a contaminant-free environment for high-quality sintering. |
Heating Elements | Generates and maintains high temperatures for sintering. |
Vacuum Pumps | Creates and maintains vacuum conditions to prevent oxidation. |
Temperature Control Systems | Ensures precise heating and cooling for uniform sintering. |
Charging System | Handles material loading/unloading in high-temperature environments. |
Water Cooling System | Prevents overheating of furnace components. |
Control Systems | Automates and monitors temperature, pressure, and vacuum levels. |
Need help selecting the right sintering furnace for your needs? Contact our experts today!