Brazing is extensively used in industrial practice due to its versatility, ability to join dissimilar materials, and cost-effectiveness. Unlike welding, brazing does not melt the base metals, which allows for the joining of materials with different melting points and reduces the risk of thermal distortion. The process involves using a filler metal with a lower melting point than the base materials, which flows into the joint by capillary action, creating strong and reliable bonds. Brazing is also suitable for complex geometries and can be automated for high-volume production. Additionally, it produces clean joints with minimal post-processing, making it a preferred method in industries like automotive, aerospace, and electronics.
Key Points Explained:
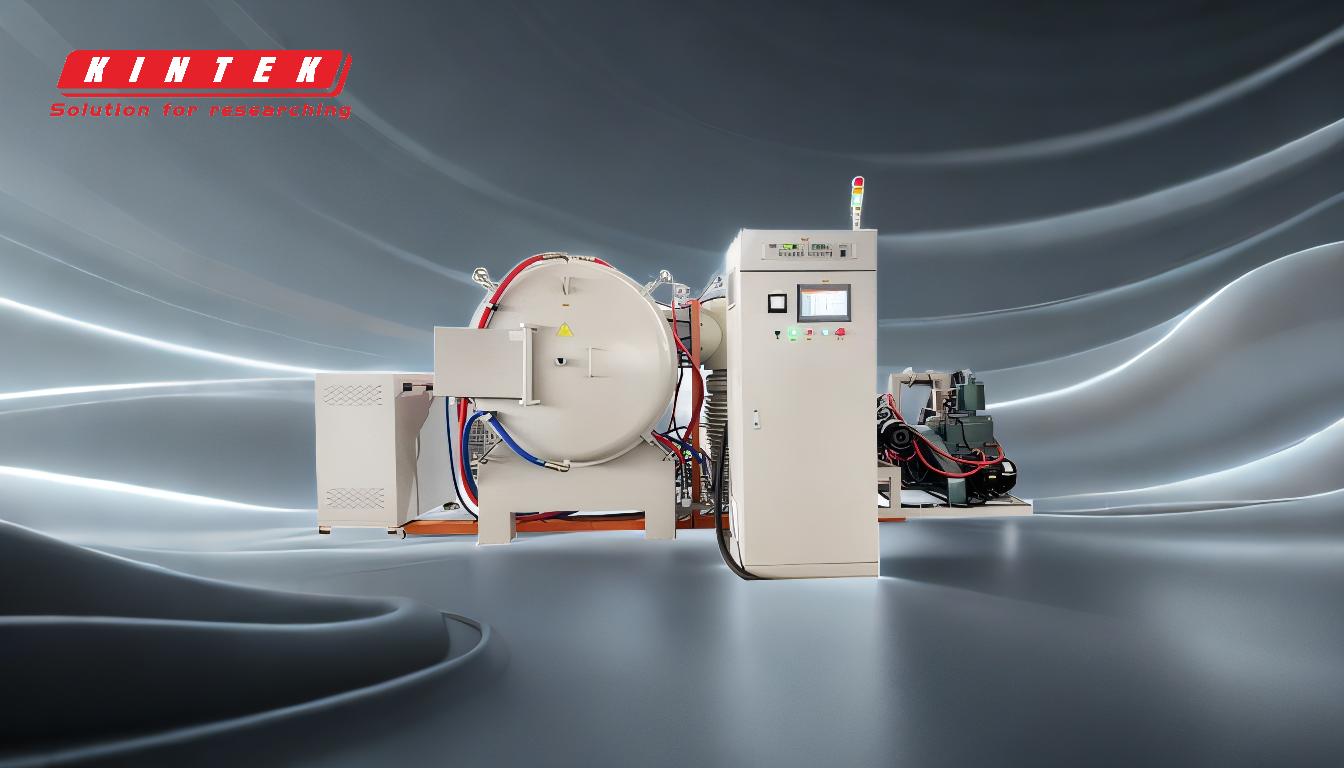
-
Versatility in Joining Dissimilar Materials
- Brazing is ideal for joining materials with different compositions, such as metals and ceramics, which is challenging for welding.
- The process does not require melting the base metals, allowing for the combination of materials with varying melting points without compromising their structural integrity.
-
Minimized Thermal Distortion
- Since brazing operates at lower temperatures compared to welding, it reduces the risk of warping or distortion in the base materials.
- This is particularly advantageous for delicate components or thin materials that are sensitive to heat.
-
Capillary Action for Strong Joints
- The filler metal flows into the joint by capillary action, ensuring uniform distribution and strong metallurgical bonds.
- This results in joints that are often stronger than the base materials themselves.
-
Suitability for Complex Geometries
- Brazing can be used to join intricate or hard-to-reach areas, making it suitable for components with complex designs.
- This flexibility is valuable in industries like aerospace and electronics, where precision is critical.
-
Cost-Effectiveness and Automation
- Brazing is a cost-effective process, especially for high-volume production, as it can be easily automated.
- The reduced need for post-processing, such as grinding or polishing, further lowers production costs.
-
Clean and Aesthetic Joints
- Brazed joints are typically clean and require minimal finishing, making them visually appealing and suitable for applications where aesthetics matter.
- The process also produces joints with excellent corrosion resistance, enhancing the durability of the final product.
-
Wide Range of Industrial Applications
- Brazing is widely used in industries such as automotive (for radiators and heat exchangers), aerospace (for turbine components), and electronics (for circuit boards).
- Its ability to create reliable and repeatable bonds makes it a preferred choice for critical applications.
In summary, brazing's unique advantages, including its ability to join dissimilar materials, create strong bonds, and minimize thermal distortion, make it a highly effective and widely adopted process in industrial practice. Its cost-effectiveness and suitability for automation further contribute to its extensive use across various industries.
Summary Table:
Advantage | Description |
---|---|
Versatility | Joins dissimilar materials like metals and ceramics without melting base metals. |
Minimized Thermal Distortion | Lower temperatures reduce warping, ideal for delicate or thin materials. |
Strong Joints via Capillary Action | Filler metal flows uniformly, creating durable metallurgical bonds. |
Complex Geometries | Suitable for intricate or hard-to-reach areas, ideal for precision industries. |
Cost-Effectiveness | Easily automated for high-volume production, reducing post-processing costs. |
Clean and Aesthetic Joints | Produces visually appealing joints with minimal finishing required. |
Wide Industrial Applications | Used in automotive, aerospace, and electronics for reliable, repeatable bonds. |
Learn how brazing can enhance your industrial processes—contact our experts today for tailored solutions!