Compression molding is a critical manufacturing process due to its ability to produce high-strength, durable, and structurally sound parts efficiently and cost-effectively. It is particularly important in industries like automotive manufacturing, where it is used to create interior components such as sun visors and gear knobs. The process involves applying heat and high pressure to raw materials like metal, plastic compounds, or rubber, ensuring dense packing and minimal material waste. Hydraulic presses enhance the speed and efficiency of compression molding, making it a preferred method for producing complex parts with varying thicknesses. Additionally, the process accommodates precise material flow into molds, resulting in high-quality finished products with minimal excess material.
Key Points Explained:
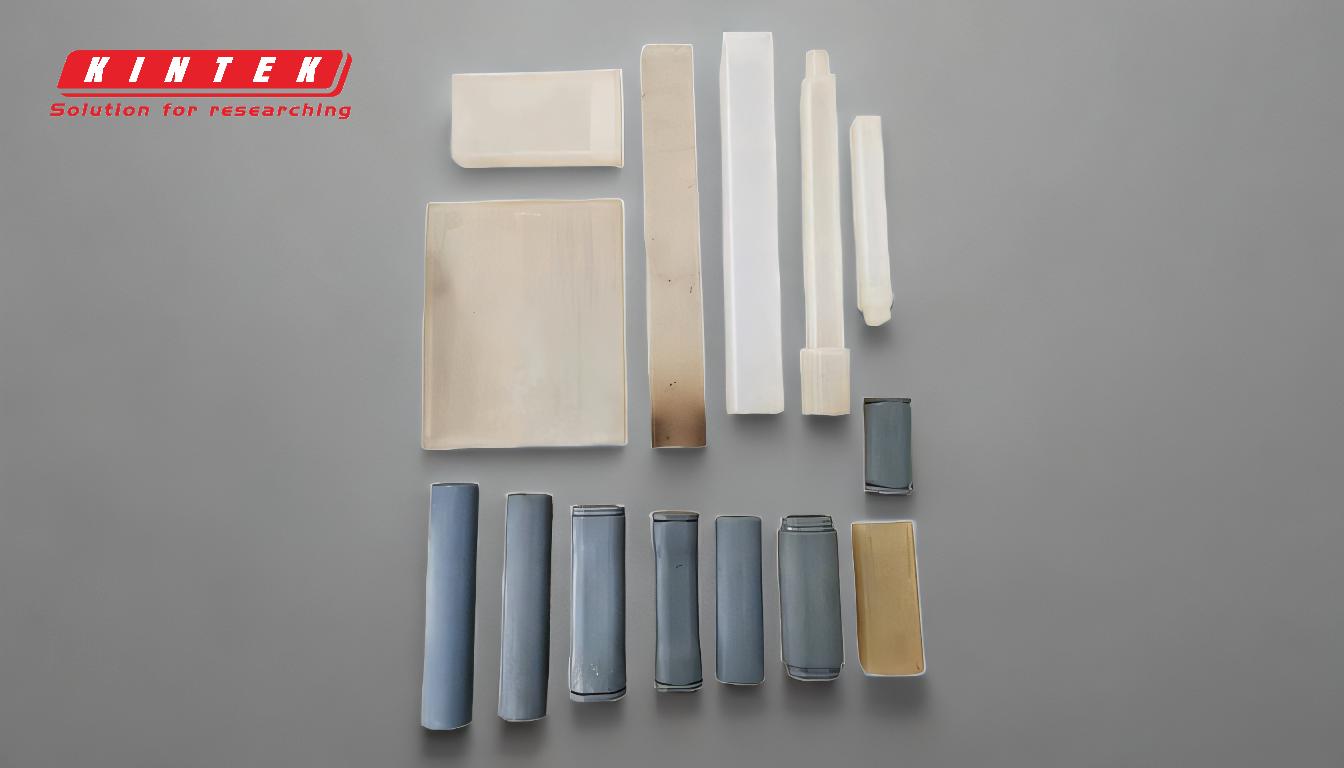
-
Produces High-Strength and Durable Parts:
- Compression molding applies high pressure during the manufacturing process, ensuring that materials are densely packed. This results in parts with excellent strength and durability, making them suitable for demanding applications.
- The dense packing of materials reduces voids and inconsistencies, enhancing the structural integrity of the final product.
-
Accommodates Varying Thicknesses:
- Unlike some other molding processes, compression molding can handle parts with varying thicknesses. This flexibility is crucial for manufacturing complex components, such as automotive interior parts, which often require intricate designs and diverse thickness profiles.
-
Ideal for Automotive Applications:
- Compression molding is widely used in the automotive industry to produce interior components like sun visors, gear knobs, and trim covers. These parts require high precision, durability, and aesthetic appeal, all of which are achievable through this process.
- The ability to use materials like rubber, plastic compounds, and metals makes it versatile for creating a wide range of automotive parts.
-
Efficient and Cost-Effective:
- Hydraulic presses play a significant role in making compression molding fast and efficient. They reduce material waste and labor costs, contributing to the overall cost-effectiveness of the process.
- The process minimizes excess material, known as mold flash, which flows out of special grooves in the mold. This reduces post-processing work and material costs.
-
Precision and Material Flow:
- Compression molding involves placing well-shaped, un-branched rubber stock into mold cavities. The mold is then closed and maintained at a fixed temperature under pressure, allowing the material to flow and fill the cavity precisely.
- This controlled flow ensures that the final product meets exact specifications, reducing the need for additional machining or finishing.
-
Versatility with Materials:
- The process can handle a variety of raw materials, including metals, plastic compounds, and rubber. This versatility makes it suitable for a wide range of industries and applications beyond automotive manufacturing.
-
Reduced Environmental Impact:
- By minimizing material waste and optimizing the use of raw materials, compression molding contributes to more sustainable manufacturing practices. This is increasingly important in industries aiming to reduce their environmental footprint.
In summary, compression molding is important because it combines strength, durability, and precision with cost-efficiency and versatility. Its ability to produce high-quality parts with varying thicknesses and minimal waste makes it a preferred choice for industries like automotive manufacturing, where performance and aesthetics are critical.
Summary Table:
Key Benefits | Explanation |
---|---|
High-Strength Parts | Dense packing ensures durability and structural integrity. |
Accommodates Varying Thicknesses | Ideal for complex parts like automotive interiors. |
Ideal for Automotive Applications | Produces precise, durable, and aesthetically appealing components. |
Efficient and Cost-Effective | Hydraulic presses reduce waste and labor costs. |
Precision Material Flow | Ensures exact specifications with minimal post-processing. |
Versatile Material Compatibility | Works with metals, plastics, and rubber for diverse applications. |
Reduced Environmental Impact | Minimizes waste, supporting sustainable manufacturing practices. |
Want to learn more about how compression molding can benefit your production process? Contact us today!