Brazing rods not sticking to copper can be a frustrating issue, often caused by a combination of factors such as improper surface preparation, incorrect temperature, or the use of unsuitable materials. To address this problem, it’s essential to understand the fundamentals of brazing, including the role of flux, the importance of clean surfaces, and the correct application of heat. By systematically troubleshooting these factors, you can improve the adhesion of the brazing rod to the copper and achieve a strong, durable bond.
Key Points Explained:
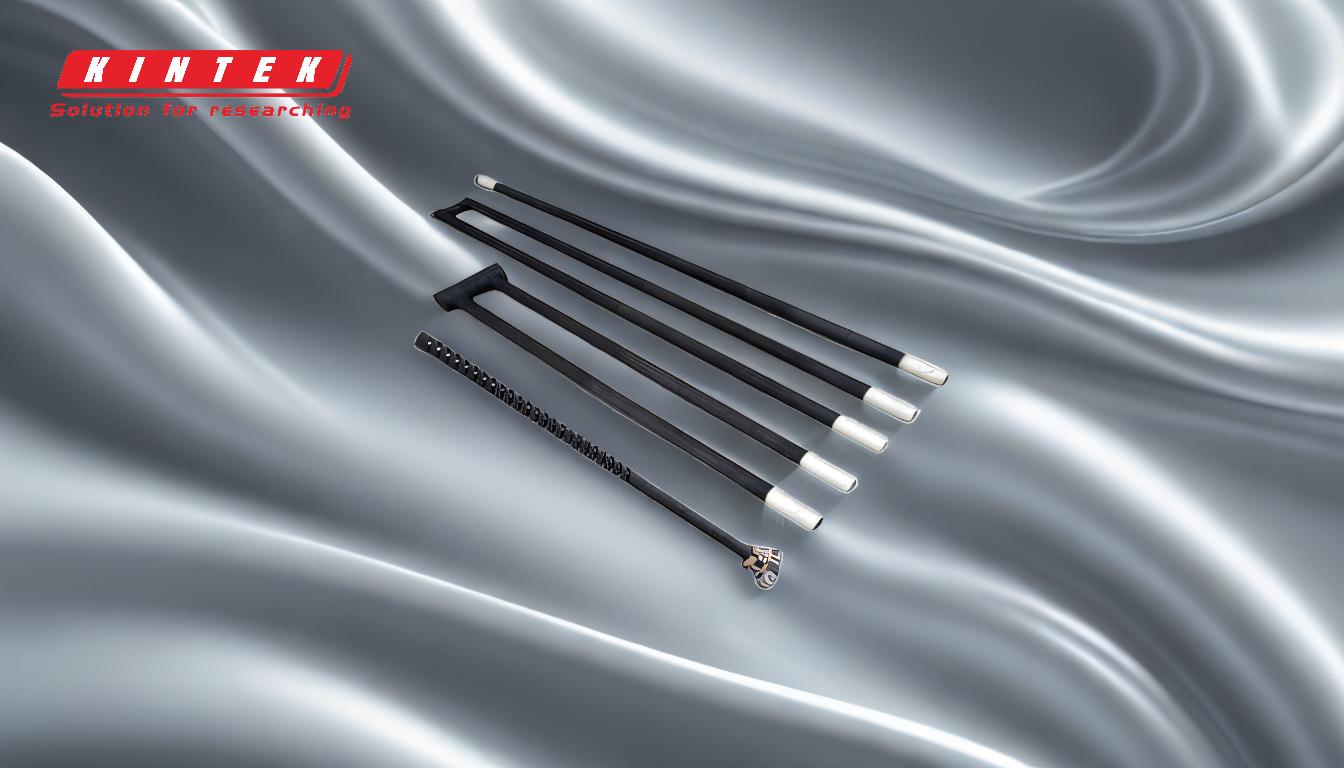
-
Surface Preparation
- Cleanliness is Critical: Copper surfaces must be free of oxidation, grease, dirt, and other contaminants. Even a thin layer of oxidation can prevent the brazing rod from adhering properly.
- Cleaning Methods: Use a wire brush, sandpaper, or a chemical cleaner specifically designed for copper to remove any impurities. Ensure the surface is shiny and clean before starting the brazing process.
- Avoid Touching the Clean Surface: After cleaning, avoid touching the area with bare hands, as oils from your skin can create a barrier between the copper and the brazing material.
-
Proper Use of Flux
- Role of Flux: Flux is essential in brazing as it prevents oxidation during the heating process and helps the brazing material flow evenly over the copper surface.
- Choosing the Right Flux: Use a flux that is compatible with both the brazing rod and the copper. For example, a borax-based flux is commonly used for copper brazing.
- Application Technique: Apply flux evenly to the joint area before heating. Too little flux can lead to incomplete bonding, while too much can cause residue buildup.
-
Temperature Control
- Correct Heating Temperature: Brazing requires a specific temperature range, typically between 800°F and 1,500°F (427°C to 815°C), depending on the brazing rod alloy. If the temperature is too low, the rod won’t melt properly; if it’s too high, the copper or the rod may oxidize or burn.
- Even Heat Distribution: Ensure that the heat is applied evenly across the joint. Uneven heating can cause the brazing material to flow unevenly or fail to bond.
- Use of a Temperature Indicator: If possible, use a temperature indicator or pyrometer to monitor the heat and ensure it stays within the optimal range.
-
Brazing Rod Compatibility
- Material Selection: Ensure the brazing rod is compatible with copper. Common brazing alloys for copper include silver-based alloys (e.g., BAg series) and phosphorus-copper alloys (e.g., BCuP series).
- Rod Diameter: Choose a brazing rod with the appropriate diameter for the joint size. A rod that’s too thick may not melt evenly, while one that’s too thin may not provide enough filler material.
- Storage Conditions: Store brazing rods in a dry, clean environment to prevent contamination or oxidation, which can affect their performance.
-
Technique and Skill
- Proper Heating Technique: Use a torch with a flame that is neither too oxidizing nor too reducing. A neutral flame is ideal for brazing copper.
- Filler Metal Application: Touch the brazing rod to the joint only after the copper has reached the correct temperature. The rod should melt and flow into the joint by capillary action, not by direct melting from the flame.
- Practice and Patience: Brazing requires practice to master. If you’re new to brazing, take the time to practice on scrap pieces of copper before working on critical projects.
-
Environmental Factors
- Avoid Drafts: Drafts or wind can cool the joint unevenly and disrupt the brazing process. Work in a controlled environment if possible.
- Moisture Control: Moisture can cause the flux to spatter or the brazing material to oxidize. Ensure the work area and materials are dry.
By addressing these key points, you can troubleshoot and resolve the issue of your brazing rod not sticking to copper. Remember that brazing is both a science and an art, and achieving consistent results often requires attention to detail and practice.
Summary Table:
Key Factor | Details |
---|---|
Surface Preparation | Clean copper thoroughly, avoid touching with bare hands. |
Flux Application | Use compatible flux, apply evenly to prevent oxidation and ensure bonding. |
Temperature Control | Maintain 800°F–1,500°F (427°C–815°C) for proper brazing. |
Brazing Rod Choice | Use copper-compatible alloys like BAg or BCuP series. |
Technique | Apply heat evenly, let the rod flow by capillary action. |
Environment | Avoid drafts and moisture to prevent bonding issues. |
Struggling with brazing? Get expert advice and solutions—contact us today!