Vacuum is essential for the deposition of thin films because it creates an environment that minimizes contamination, ensures high-quality film formation, and enables precise control over the deposition process. By reducing particle density and increasing the mean free path of evaporated atoms, a vacuum environment ensures that the material is deposited efficiently on the substrate without interference from unwanted gases or particles. This results in films with high purity, strong adhesion, and consistent properties, which are critical for applications in electronics, optics, and coatings.
Key Points Explained:
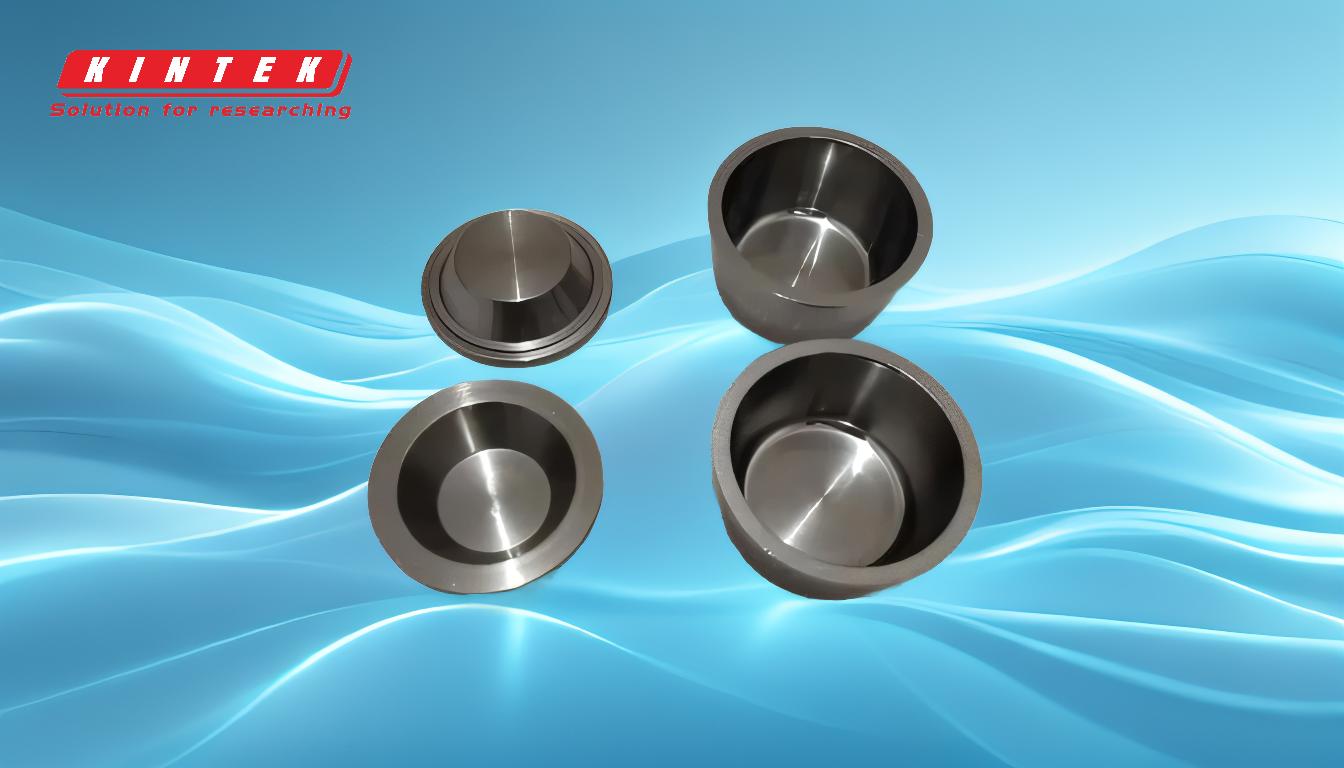
-
Reduction of Contamination
- A vacuum environment significantly reduces the presence of unwanted substances such as oxygen, nitrogen, carbon dioxide, and water vapor. These contaminants can react with the film material, leading to impurities, oxidation, or other chemical changes that degrade film quality.
- For example, in PVD (Physical Vapor Deposition) processes, maintaining a vacuum pressure of less than 10^-5 torr ensures that the target material vaporizes, transports, and condenses without interference from atmospheric gases.
-
Increased Mean Free Path
- The mean free path is the average distance an atom or molecule travels before colliding with another particle. In a vacuum, the reduced particle density allows evaporated atoms to travel longer distances without collisions, ensuring they reach the substrate efficiently.
- This is particularly important in processes like E-beam deposition, where a high mean free path ensures that most of the evaporated material is deposited on the substrate, minimizing losses and improving deposition efficiency.
-
Control Over Gas and Vapor Composition
- A vacuum environment allows precise control over the gas and vapor composition within the deposition chamber. This is critical for processes that require specific gas mixtures or plasma conditions to achieve desired film properties.
- For instance, in sputtering or plasma-enhanced deposition, the vacuum enables the creation of a low-pressure plasma environment, which is essential for ionizing gases and controlling the energy distribution of particles.
-
Minimization of Gaseous Contamination
- By maintaining a vacuum, the likelihood of gaseous contamination is reduced, which is crucial for achieving high-purity thin films. Contaminants can weaken the adhesiveness of the film or cause the film material to bond with other substances in the air, leading to defects.
- A vacuum degree better than 6 x 10^-2 Pa is typically required in vacuum evaporation processes to ensure that the evaporating atoms or molecules deposit on the substrate without interference.
-
Improved Film Adhesion and Purity
- A high vacuum ensures that the film material adheres strongly to the substrate and maintains its purity. Without a vacuum, the presence of air molecules can obstruct the movement of film particles, leading to poor adhesion and inconsistent film properties.
- This is particularly important for applications requiring high-performance films, such as in semiconductors or optical coatings, where even minor impurities can significantly impact performance.
-
Enhanced Process Control
- Vacuum conditions enable precise control over the deposition process, including mass flow control, gas pressure, and plasma conditions. This level of control is essential for achieving uniform film thickness, composition, and properties across the substrate.
- For example, in sputtering processes, the vacuum environment allows for the precise regulation of gas pressure and plasma density, which directly influence the deposition rate and film quality.
-
Influence on Plasma and Energy Distribution
- In processes involving plasma, such as sputtering or plasma-enhanced chemical vapor deposition (PECVD), the vacuum environment influences the enthalpy, density of charged and uncharged particles, and energy distribution in the plasma.
- This control is critical for optimizing the deposition process and ensuring that the film has the desired mechanical, electrical, or optical properties.
By addressing these key points, it becomes clear that vacuum is not just a technical requirement but a fundamental aspect of thin film deposition that directly impacts the quality, performance, and reliability of the final product.
Summary Table:
Key Benefit | Explanation |
---|---|
Reduction of Contamination | Minimizes unwanted substances like oxygen and water vapor, ensuring high purity. |
Increased Mean Free Path | Allows evaporated atoms to travel farther without collisions, improving efficiency. |
Control Over Gas Composition | Enables precise gas and vapor control for desired film properties. |
Minimization of Contamination | Reduces gaseous contamination, enhancing film adhesion and purity. |
Improved Film Adhesion | Ensures strong bonding and consistent film properties. |
Enhanced Process Control | Enables precise regulation of deposition parameters for uniform film quality. |
Influence on Plasma | Optimizes plasma conditions for mechanical, electrical, or optical properties. |
Ready to achieve high-quality thin films? Contact our experts today for tailored solutions!