Sputter coating is a widely used technique in various industries, including electronics, optics, and materials science, for depositing thin films onto substrates. The necessity of a vacuum in sputter coating is fundamental to the process's success. A vacuum environment ensures that ejected atoms from the target material can travel unimpeded to the substrate, minimizing collisions with gas molecules that could otherwise scatter the atoms and degrade the quality of the coating. Additionally, maintaining the correct pressure is crucial for sustaining the plasma required for sputtering. Too low a pressure results in insufficient collisions to sustain the plasma, while too high a pressure causes excessive collisions, preventing electrons from gaining enough energy to ionize atoms effectively. This balance is essential for achieving high-quality, uniform coatings.
Key Points Explained:
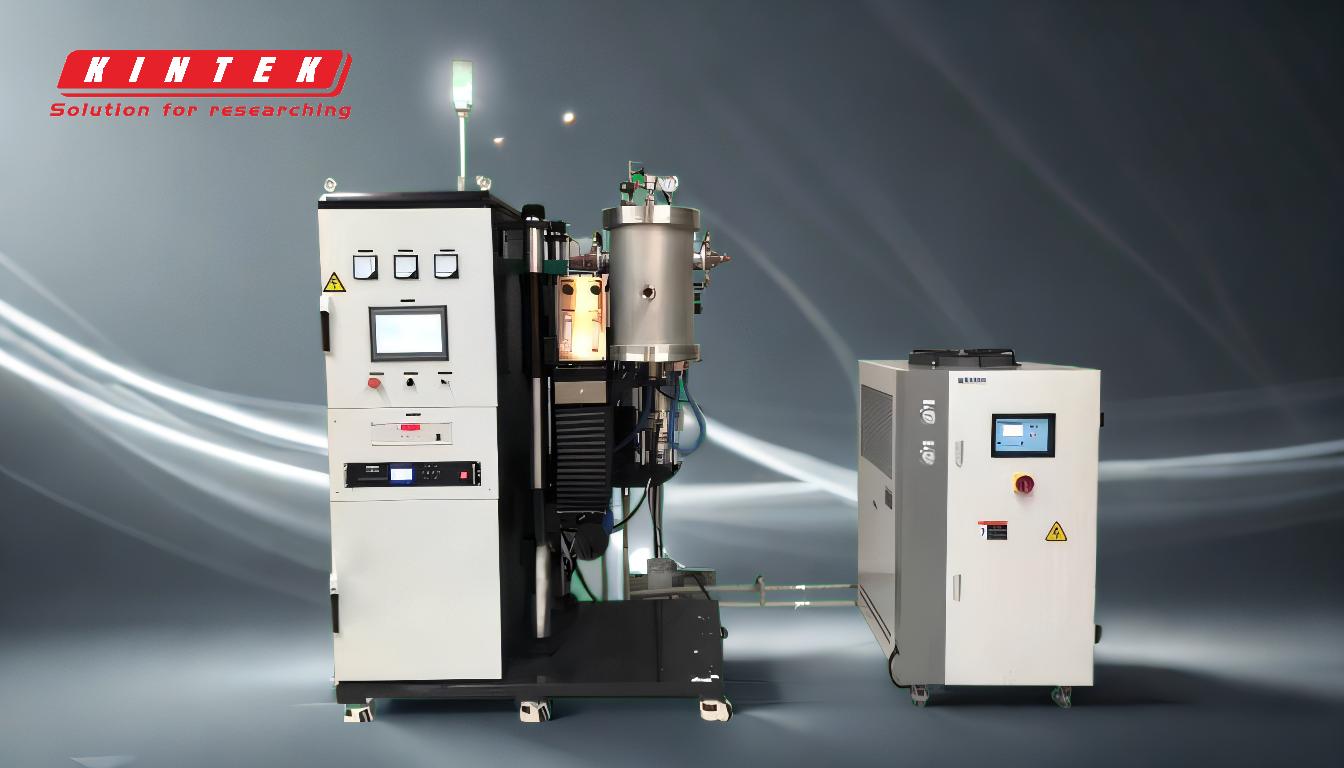
-
Minimizing Atomic Scattering:
- In a vacuum, the mean free path of ejected atoms from the sputtering target is significantly increased. This means that atoms can travel directly to the substrate without being scattered by gas molecules. In a non-vacuum environment, frequent collisions with air molecules would cause the atoms to deviate from their intended path, leading to uneven or poor-quality coatings.
-
Sustaining Plasma:
- Sputter coating relies on the generation of a plasma, which is a highly ionized gas containing free electrons and ions. The plasma is essential for bombarding the target material with ions, causing atoms to be ejected. A vacuum environment helps maintain the plasma by ensuring that electrons can gain sufficient energy to ionize gas atoms. If the pressure is too high, electrons lose energy through excessive collisions, making it difficult to sustain the plasma.
-
Preventing Contamination:
- A vacuum environment significantly reduces the presence of contaminants such as oxygen, water vapor, and other reactive gases. These contaminants can react with the sputtered atoms, forming oxides or other compounds that degrade the quality of the thin film. By operating in a vacuum, the purity of the deposited material is preserved, leading to better performance of the coated product.
-
Controlling Deposition Rate:
- The vacuum environment allows for precise control over the deposition rate of the thin film. By adjusting the pressure and the power applied to the target, operators can fine-tune the rate at which atoms are deposited onto the substrate. This control is crucial for applications requiring specific thicknesses or properties of the coating.
-
Enhancing Film Uniformity:
- Uniformity is critical in many applications of sputter coating, such as in the production of optical coatings or semiconductor devices. A vacuum ensures that the sputtered atoms are evenly distributed across the substrate, leading to a consistent and uniform film. This uniformity is difficult to achieve in a non-vacuum environment due to the unpredictable scattering of atoms.
-
Improving Adhesion:
- The adhesion of the thin film to the substrate is another critical factor influenced by the vacuum environment. In a vacuum, the substrate surface can be cleaned more effectively, often through ion bombardment, which removes any contaminants or oxides. This clean surface allows for better bonding between the substrate and the deposited film, enhancing the overall durability and performance of the coating.
In summary, the vacuum environment in sputter coating is essential for ensuring the quality, uniformity, and performance of the deposited thin films. It minimizes atomic scattering, sustains the plasma, prevents contamination, controls deposition rates, enhances film uniformity, and improves adhesion. These factors collectively make the vacuum a critical component of the sputter coating process.
Summary Table:
Key Factor | Role in Sputter Coating |
---|---|
Minimizing Atomic Scattering | Ensures atoms travel directly to the substrate, reducing collisions for uniform coatings. |
Sustaining Plasma | Maintains plasma stability by allowing electrons to ionize gas atoms effectively. |
Preventing Contamination | Reduces reactive gases, preserving the purity and performance of the thin film. |
Controlling Deposition Rate | Enables precise tuning of coating thickness and properties. |
Enhancing Film Uniformity | Ensures even distribution of atoms for consistent, high-quality coatings. |
Improving Adhesion | Provides a clean substrate surface for better bonding and durability. |
Want to achieve high-quality sputter coatings? Contact our experts today for tailored solutions!