Thin film deposition processes, such as Chemical Vapor Deposition (CVD) and Physical Vapor Deposition (PVD), often require a vacuum system to achieve high-quality, uniform, and precise coatings. A vacuum environment is essential for several reasons: it minimizes contamination, ensures the efficient transfer of material to the substrate, and allows for precise control over the deposition process. Without a vacuum, the presence of air or other gases would interfere with the deposition mechanisms, leading to poor film quality, reduced adhesion, and inconsistent results. The vacuum system also enables the creation of specific film properties, such as high purity, hardness, and wear resistance, which are critical for advanced applications in industries like electronics, optics, and aerospace.
Key Points Explained:
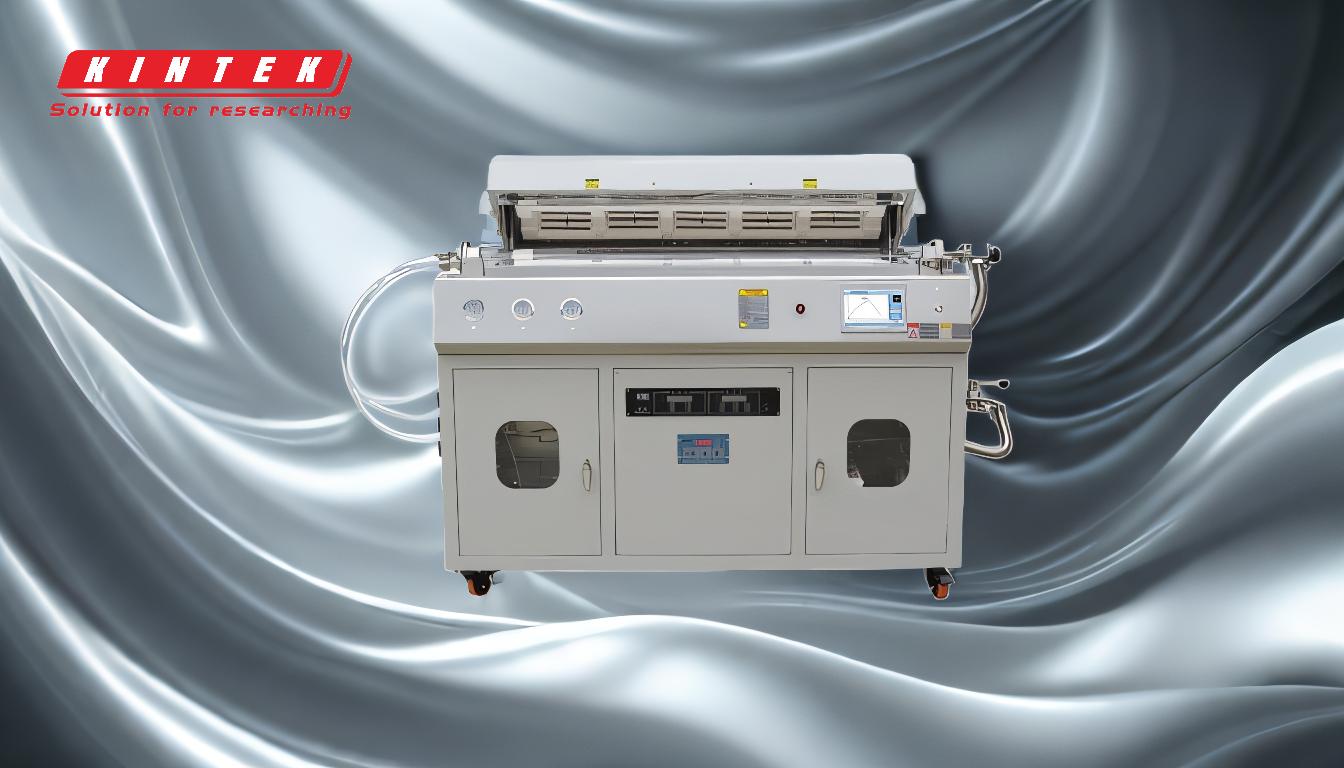
-
Minimizing Contamination:
- In a vacuum environment, the absence of air and other gases reduces the risk of impurities being incorporated into the thin film. Contaminants such as oxygen, nitrogen, or water vapor can react with the deposited material, leading to defects, reduced purity, or altered properties. For example, in CVD, even small amounts of contamination can affect the film's density and uniformity. A vacuum ensures a clean environment, which is crucial for producing high-purity films.
-
Efficient Material Transfer:
- In PVD processes like sputtering, a vacuum is necessary to allow ejected atoms or molecules to travel freely from the target to the substrate without being obstructed by air molecules. At atmospheric pressure, collisions with air molecules would slow down the particles, reducing their energy and adhesion to the substrate. A vacuum ensures that the material reaches the substrate with sufficient energy, resulting in a strong and durable bond.
-
Controlled Deposition Process:
- A vacuum provides a controlled environment where parameters such as pressure, temperature, and gas composition can be precisely regulated. This level of control is essential for achieving consistent and reproducible thin film characteristics. For instance, in sputtering, maintaining the correct pressure is critical to sustain a plasma and ensure proper ionization of the target material. Too high or too low pressure can disrupt the process, leading to uneven or incomplete coatings.
-
Enhanced Film Properties:
- Thin films deposited in a vacuum often exhibit superior properties, such as high hardness, wear resistance, and thermal stability. For example, PVD coatings are known for their extreme hardness and corrosion resistance, making them ideal for industrial applications. Similarly, CVD can produce films with very high purity and density, which are difficult to achieve with other methods. The vacuum environment plays a key role in enabling these advanced properties.
-
Versatility and Uniformity:
- A vacuum system allows for the uniform deposition of thin films on complex geometries, including irregular surfaces, recesses, and screw threads. This is particularly important in CVD, where the ability to evenly coat intricate shapes is a major advantage. The vacuum ensures that the deposition process is not hindered by air resistance, enabling consistent coverage across the entire substrate.
-
Environmental and Economic Benefits:
- Vacuum-based deposition processes are considered environmentally friendly because they typically produce fewer harmful byproducts compared to traditional coating methods. Additionally, these processes are relatively economical, as they can coat multiple parts simultaneously, reducing production time and costs. The use of a vacuum system contributes to the overall efficiency and sustainability of the deposition process.
In summary, a vacuum system is indispensable for thin film deposition because it ensures a clean, controlled, and efficient environment for producing high-quality coatings. It minimizes contamination, enhances material transfer, and enables the creation of films with specific, desirable properties, making it a critical component in advanced manufacturing and technology applications.
Summary Table:
Key Benefit | Explanation |
---|---|
Minimizing Contamination | Reduces impurities like oxygen and nitrogen, ensuring high-purity films. |
Efficient Material Transfer | Enables particles to travel freely, ensuring strong adhesion and durable bonds. |
Controlled Deposition | Allows precise regulation of pressure, temperature, and gas composition. |
Enhanced Film Properties | Produces films with high hardness, wear resistance, and thermal stability. |
Uniformity & Versatility | Ensures even coating on complex geometries, including irregular surfaces. |
Environmental & Economic | Reduces harmful byproducts and lowers production costs. |
Ready to achieve superior thin film coatings? Contact our experts today to learn more about vacuum systems!