Brazing can indeed stick to cast iron, but it requires careful preparation and the right techniques to ensure a strong and durable bond. Cast iron is known for its high carbon content and porosity, which can make brazing more challenging compared to other metals. However, with proper surface preparation, the correct choice of brazing filler material, and controlled heating, brazing can be successfully used to join or repair cast iron components. The process involves cleaning the surface thoroughly to remove any impurities, using a flux to prevent oxidation, and applying the brazing filler material at the appropriate temperature. This method is often preferred for its ability to create strong, leak-proof joints without the need for high temperatures that could potentially damage the cast iron.
Key Points Explained:
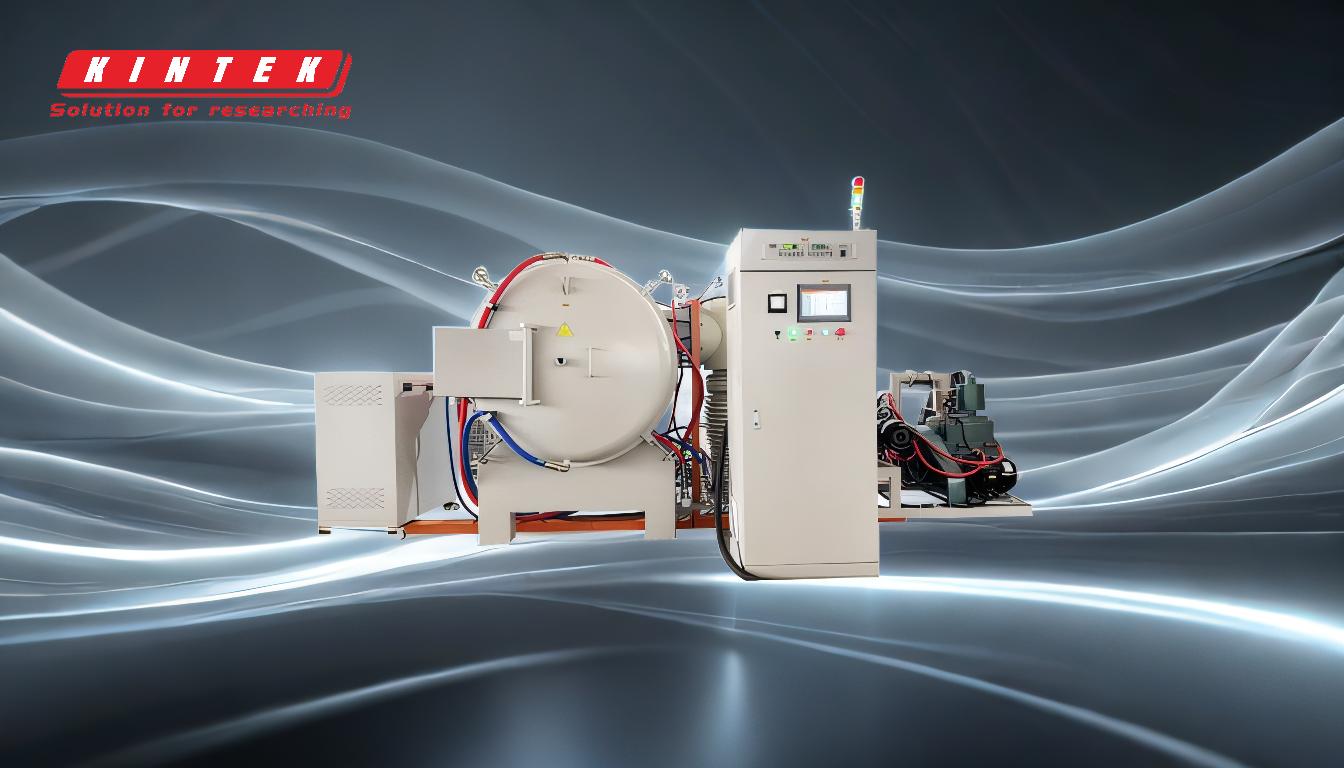
-
Understanding the Challenges of Brazing Cast Iron:
- Cast iron's high carbon content and porosity can make it difficult to braze. The carbon can react with the brazing filler material, leading to weak joints.
- Porosity in cast iron can trap contaminants, which can interfere with the brazing process and result in poor adhesion.
-
Surface Preparation:
- Cleaning: The surface of the cast iron must be thoroughly cleaned to remove any grease, oil, or rust. This can be done using solvents, wire brushing, or sandblasting.
- Machining: In some cases, machining the surface to remove the outer layer of cast iron can help expose a cleaner, more uniform surface for brazing.
-
Choosing the Right Brazing Filler Material:
- Silver-Based Alloys: These are commonly used for brazing cast iron due to their lower melting points and good wetting properties.
- Nickel-Based Alloys: These are stronger and more suitable for high-stress applications but require higher temperatures.
- Copper-Based Alloys: These are less common but can be used in specific applications where a strong, ductile joint is needed.
-
Using Flux:
- Flux is essential to prevent oxidation during the brazing process. It helps the brazing filler material flow evenly and adhere to the cast iron surface.
- The type of flux used should be compatible with the brazing filler material and the specific application.
-
Controlled Heating:
- Temperature Control: Brazing cast iron requires precise temperature control to avoid overheating, which can cause the cast iron to crack or warp.
- Uniform Heating: Ensuring that the entire joint area is heated evenly is crucial for a strong bond. This can be achieved using a torch, furnace, or induction heating.
-
Post-Brazing Treatment:
- Cooling: Allow the brazed joint to cool slowly to prevent thermal stress and cracking.
- Cleaning: Remove any residual flux to prevent corrosion and ensure a clean finish.
-
Applications of Brazing Cast Iron:
- Repair: Brazing is often used to repair cracks or broken parts in cast iron components, such as engine blocks or machinery parts.
- Joining: It can also be used to join cast iron parts to other metals, creating strong, leak-proof joints.
By following these steps and considerations, brazing can be effectively used to join or repair cast iron components, providing a durable and reliable solution.
Summary Table:
Key Step | Details |
---|---|
Surface Preparation | Clean thoroughly using solvents, wire brushing, or sandblasting. Machine if needed. |
Brazing Filler Material | Silver-based (lower melting point), Nickel-based (high strength), Copper-based (specific applications). |
Flux Application | Use compatible flux to prevent oxidation and ensure even filler flow. |
Controlled Heating | Maintain precise temperature control with uniform heating to avoid damage. |
Post-Brazing Treatment | Cool slowly to prevent cracking; clean residual flux for corrosion prevention. |
Applications | Repair cracks or broken parts; join cast iron to other metals. |
Need expert advice on brazing cast iron? Contact us today for tailored solutions!