Introduction to Warm Isostatic Pressing (WIP)
Warm Isostatic Pressing (WIP) represents a sophisticated technology in the realm of material processing, offering a unique approach to enhancing material properties through controlled heating and pressure. This article delves into the fundamental principles of WIP, distinguishing it from its counterparts, Cold Isostatic Pressing (CIP) and Hot Isostatic Pressing (HIP). By exploring the technological advancements, diverse applications, and significant benefits of WIP, we aim to provide a comprehensive understanding of how this method contributes to the advancement of manufacturing processes. Join us as we uncover the intricacies of WIP and its pivotal role in shaping the future of material processing.
Technological Advancements in Warm Isostatic Pressing (WIP)
Warm Isostatic Pressing (WIP) technology has seen significant advancements in recent years, enhancing its efficiency and applicability across various industries. These advancements primarily focus on improvements in heating elements, pressure mediums, and uniform pressure distribution techniques, making WIP a more versatile and effective method for material processing.
Improvements in Heating Elements
One of the key areas of innovation in WIP technology is the development of advanced heating elements. Traditional heating elements often faced limitations in terms of temperature control precision and energy efficiency. Modern WIP systems now incorporate advanced heating elements such as induction heaters and ceramic heaters, which offer better temperature uniformity and faster heating rates. These new heating elements can maintain precise temperatures within a narrow range, ensuring consistent processing conditions and improving the quality of the final product.
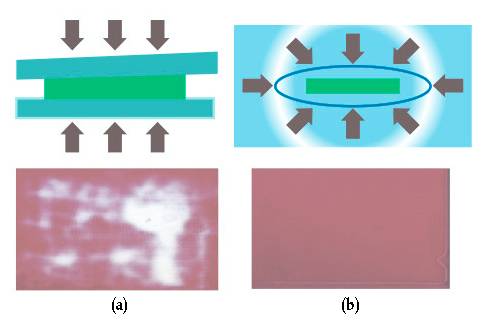
Innovations in Pressure Mediums
The choice of pressure medium in WIP systems has also undergone significant improvements. Traditionally, water and oil were commonly used as pressure mediums due to their ability to evenly distribute pressure. However, these mediums had limitations in terms of temperature stability and compatibility with certain materials. Recent advancements have led to the development of new pressure mediums, such as specialized gases and hybrid fluids, which offer better thermal stability and are compatible with a wider range of materials. These new mediums allow for more controlled and uniform pressure application, leading to improved material properties and reduced processing times.
Enhanced Uniform Pressure Distribution Techniques
Uniform pressure distribution is crucial in WIP to ensure consistent material compaction and avoid dimensional variations. Technological advancements in pressure distribution techniques have led to the development of sophisticated pressure vessels and control systems. These systems use advanced sensors and feedback mechanisms to monitor and adjust pressure distribution in real-time, ensuring that pressure is evenly applied across all surfaces of the material. This level of precision helps to eliminate defects and improve the overall quality of the processed materials.
Applications and Benefits
The advancements in WIP technology have expanded its applications across various industries, including aerospace, automotive, electronics, and medical. In the aerospace industry, WIP is used to produce high-performance components with improved strength and durability. In the automotive industry, WIP helps in manufacturing lightweight and high-strength parts, contributing to fuel efficiency and performance. In the electronics industry, WIP is utilized for compacting different shaped parts with uniform pressure, resulting in consistent dimensional accuracy and reliability.
Conclusion
The latest technological advancements in Warm Isostatic Pressing equipment have significantly enhanced its capabilities and efficiency. Improvements in heating elements, pressure mediums, and uniform pressure distribution techniques have made WIP a more reliable and versatile method for material processing. These advancements not only improve the quality of the final products but also increase productivity and reduce costs, making WIP an attractive option for manufacturers across various industries.
Applications of Warm Isostatic Pressing
Warm Isostatic Pressing (WIP) is a versatile technology that has found applications across various industries, including ceramics, metals, composites, and electronic components. This process involves applying both pressure and heat to materials, typically at temperatures below 100°C, to achieve high-density, near-net-shape components with superior mechanical and electrical properties. The technology is particularly beneficial for producing advanced materials and components that require precise control over their microstructures and properties.
Ceramics Industry
In the ceramics industry, WIP is extensively used to produce high-quality monolithic multilayer ceramic electronic components such as Multi-Layer Ceramic Capacitors (MLCC), Multi-Layer Ceramic Inductors (MLCI), and Low Temperature Co-fired Ceramics (LTCC). These components are critical in various electronic devices, including smartphones, computers, and automotive electronics. The WIP process allows for the compression of green sheets to produce components with higher quality and density than those manufactured by conventional uniaxial pressing methods.
Metal Industry
The metal industry also benefits from WIP, particularly in the production of complex-shaped metal components. WIP enables the consolidation of metal powders into dense, fully-formed parts with minimal porosity. This is crucial for applications in aerospace, automotive, and medical devices where component strength and reliability are paramount. The ability to achieve near-net-shape components reduces material waste and machining requirements, making the process more cost-effective and environmentally friendly.
Composites and Electronic Components
WIP is also applied in the composites industry, where it is used to produce high-performance composite materials with enhanced mechanical properties. These materials are used in applications ranging from aerospace and defense to sporting goods. In the electronic components sector, WIP is used to produce components such as hybrid chips, Bluetooth modules, and fuel cells. These components require precise control over their internal structures to ensure optimal performance and reliability.
Specific Applications
Multi-Layer Ceramic Capacitors (MLCC)
MLCCs are among the most common electronic components produced using WIP. These capacitors are used in a wide range of electronic devices for filtering, decoupling, and energy storage. The WIP process ensures that MLCCs are produced with high density and uniformity, which is critical for their performance and reliability.
Low Temperature Co-fired Ceramics (LTCC)
LTCC technology involves the co-firing of ceramic layers with embedded conductive traces at low temperatures. WIP is essential in this process to achieve the necessary density and dimensional accuracy of the ceramic layers. LTCC components are used in high-frequency applications, such as in wireless communication devices and radar systems.
Medical Electronics and Implants
In the medical field, WIP is used to produce high-precision components for medical electronics and implants. These components must meet stringent requirements for biocompatibility, strength, and reliability. WIP allows for the production of these components with the necessary properties to ensure patient safety and device effectiveness.
Conclusion
Warm Isostatic Pressing is a critical technology that enables the production of high-quality, high-performance materials and components across various industries. Its ability to combine pressure and controlled temperatures allows for the production of components with superior properties and reliability. As industries continue to demand more advanced materials and components, the applications of WIP are expected to expand, further solidifying its importance in modern manufacturing.
Benefits of Using WIP in Material Processing
Warm Isostatic Pressing (WIP) is a sophisticated technique that enhances the processing of materials by applying uniform pressure at elevated temperatures, typically up to 100°C. This method is particularly advantageous in industries such as electronics, where precision and uniformity in material properties are critical. Unlike traditional pressing methods that often result in uneven pressure distribution, WIP ensures that all surfaces of the material receive equal pressure, leading to consistent dimensional accuracy and material integrity.
Improved Material Density
One of the primary benefits of using WIP is the significant improvement in material density. By applying pressure uniformly at a warm temperature, WIP facilitates the consolidation of powder materials into dense compacts without the need for extremely high temperatures or pressures. This results in a more uniform distribution of particles, which enhances the overall density of the material. Studies have shown that materials processed through WIP can achieve densities close to their theoretical maximum, which is crucial for applications requiring high strength and durability.
Microstructure Uniformity
The uniform pressure applied during WIP not only improves density but also leads to a more uniform microstructure. This uniformity is essential for ensuring consistent mechanical properties across the entire material. In traditional pressing methods, variations in pressure can lead to differences in grain size and distribution, which can affect the material's performance. With WIP, the controlled environment ensures that the microstructure remains consistent, leading to improved material reliability and performance.
Enhanced Mechanical Properties
Materials processed through WIP exhibit enhanced mechanical properties, including improved strength, ductility, and fatigue resistance. The uniform pressure and temperature conditions during WIP help eliminate internal porosity, which is a common issue in materials processed through conventional methods. By reducing internal defects, WIP-processed materials can withstand higher stresses and exhibit better overall performance. This is particularly beneficial in applications where the material is subjected to repeated loading and unloading cycles, such as in the aerospace and automotive industries.
Cost-Effectiveness and Efficiency
WIP is also recognized for its cost-effectiveness and efficiency in material processing. Unlike Hot Isostatic Pressing (HIP), which requires higher temperatures and pressures, WIP operates at relatively lower conditions, reducing energy consumption and equipment costs. Additionally, the ability to process a wide range of materials and shapes makes WIP a versatile and efficient choice for manufacturers. The reduced variability in mechanical properties also means fewer rejects and reworks, further enhancing the economic benefits of using WIP.
Environmental and Safety Benefits
From an environmental and safety perspective, WIP offers several advantages. The lower operating temperatures and pressures compared to HIP reduce the risk of thermal degradation and hazardous emissions. Moreover, the uniform pressure distribution minimizes the risk of material defects that could lead to safety issues in end-use applications. These factors make WIP a safer and more environmentally friendly option for material processing.
In conclusion, Warm Isostatic Pressing (WIP) provides numerous benefits over other pressing methods, including improved material density, microstructure uniformity, and enhanced mechanical properties. Its cost-effectiveness, efficiency, and safety benefits make it an attractive choice for various industries, particularly those requiring high precision and reliability in material processing. As technology continues to advance, the applications and benefits of WIP are expected to expand, further solidifying its position as a preferred method in material processing.
Operating Parameters and Safety Considerations
In the realm of high-pressure glass reactors, understanding and adhering to the key operating parameters is crucial for both the efficiency of the process and the safety of the personnel involved. This section delves into the critical aspects of temperature control, pressure management, and the essential safety measures that must be implemented to ensure the safe and effective operation of these reactors.
Temperature Control
Temperature is a fundamental parameter in chemical reactions, influencing the rate of reaction, the selectivity of products, and the overall efficiency of the process. High-pressure glass reactors are typically equipped with sophisticated temperature control systems that allow for precise regulation of the reaction environment. These systems can maintain temperatures within a narrow range, ensuring consistent and predictable outcomes.
For instance, the temperature range for many high-pressure reactions can span from ambient to several hundred degrees Celsius. It is imperative that the reactor's temperature control system is capable of handling these extremes without compromising the integrity of the vessel or the quality of the reaction. Advanced sensors and feedback mechanisms are often employed to continuously monitor and adjust the temperature, ensuring that it remains within the desired parameters.
Pressure Management
Pressure is another critical parameter that must be carefully managed in high-pressure glass reactors. The pressure within the reactor can significantly affect the outcome of the reaction, and excessive pressure can lead to catastrophic failures of the vessel. Therefore, it is essential to operate the reactor at the appropriate pressure for the specific reaction being run.
Pressure vessels used in these reactors are designed to withstand specific pressure ratings, and it is crucial to verify that the vessel is rated for the intended operating conditions. Before initiating any reaction, users must ensure that the pressure vessel has been tested and is suitable for use at the required temperature and pressure. Additionally, it is important to check for any residual pressure in the vessel before opening it to prevent any potential hazards.
Safety Measures
Safety is paramount when operating high-pressure glass reactors. These reactors can be dangerous if not handled correctly, and it is essential to follow the manufacturer's instructions and safety guidelines meticulously. Several safety measures must be implemented to ensure the safe operation of the reactor:
-
Pressure Relief Systems: High-pressure reactors should be equipped with pressure relief systems to prevent the buildup of excessive pressure. These systems can safely vent the pressure in case of an overpressure situation, preventing potential vessel failure.
-
Interlocks and Safety Valves: Interlocks and safety valves are critical components that ensure the reactor operates within safe limits. Interlocks can prevent the reactor from being operated outside of its specified parameters, while safety valves can release pressure if it exceeds safe levels.
-
Personal Protective Equipment (PPE): Operators should always wear appropriate PPE, including safety glasses, gloves, and protective clothing, to shield themselves from potential hazards.
-
Regular Maintenance and Inspection: Regular maintenance and inspection of the reactor and its components are essential to ensure its continued safe operation. This includes checking the integrity of the pressure vessel, the functionality of the temperature control system, and the proper operation of safety devices.
Regulatory Compliance and Advancements
Pressure vessel designs have evolved to meet and exceed regulatory standards, with increased cycle life, higher pressure processing, and enhanced safety being the primary drivers. New furnace designs and materials, such as molybdenum, steel, and graphite, have expanded the process's temperature parameters, allowing for greater flexibility and efficiency.
Advanced computer controls now play a pivotal role in monitoring and controlling high-pressure reactors. These systems can manage one or multiple reactors within a plant, providing real-time data and automated adjustments to ensure optimal operation. The integration of advanced controls has significantly improved the safety and reliability of high-pressure processes, making them more accessible and manageable.
In conclusion, the safe and efficient operation of high-pressure glass reactors hinges on the meticulous management of temperature and pressure parameters and the implementation of robust safety measures. By adhering to these guidelines and leveraging advanced technologies, operators can ensure the successful execution of their reactions while maintaining a high level of safety.
Future Trends in Warm Isostatic Pressing
Warm Isostatic Pressing (WIP) technology is poised for significant advancements and broader applications in the coming years. As industries continue to seek materials with enhanced performance and reliability, WIP is expected to play a crucial role in the development of new materials and the integration with other advanced technologies. This section explores the potential future trends in WIP, focusing on emerging materials, integration with other technologies, and sustainability considerations.
Emerging Materials
The demand for high-quality, durable materials is driving the innovation in WIP. Researchers and manufacturers are exploring new materials that can benefit from the uniform pressure and temperature conditions provided by WIP. Ceramics, advanced alloys, and composites are among the materials that are being investigated for their potential in WIP applications. For instance, the aerospace and automotive sectors are showing increasing interest in ceramic additive manufacturing, which can be enhanced through WIP to achieve superior density and microstructure uniformity.
Integration with Other Technologies
One of the significant trends in WIP is its integration with other advanced manufacturing and heat treatment processes. Combining WIP with technologies such as additive manufacturing, spark plasma sintering, and other heat treatment processes can lead to the creation of high-integrity, near-net-shaped parts from metal powders. This integration not only reduces processing costs and energy consumption but also improves the delivery time of components. For example, the combination of WIP with additive manufacturing allows for the production of complex geometries with enhanced mechanical properties, making it a valuable tool for industries requiring high-performance components.
Sustainability Considerations
Sustainability is becoming a critical factor in the development of manufacturing processes, and WIP is no exception. The energy efficiency of WIP equipment is being improved to reduce its environmental impact. Additionally, the use of WIP in recycling processes is being explored to enhance the sustainability of material production. By enabling the consolidation of recycled materials into high-performance components, WIP can contribute to the circular economy and reduce the reliance on raw materials.
Market Trends and Innovations
The isostatic pressing market is witnessing a growing emphasis on the combination of WIP with other heat treatment processes. This trend is driven by the need for more efficient and reliable solutions in various industries. Manufacturers are constantly innovating to improve processes, develop new materials, and explore new applications. The integration of WIP with other technologies is expected to expand rapidly, as interest in advanced manufacturing processes continues to grow.
Conclusion
The future of Warm Isostatic Pressing is promising, with significant potential for advancements in emerging materials, integration with other technologies, and sustainability considerations. As industries seek to enhance material performance and reliability, WIP will play a crucial role in meeting these demands. The ongoing innovations in WIP technology are expected to drive its broader adoption and application in various sectors, contributing to the advancement of manufacturing processes and the development of high-performance materials.
Conclusion: The Role of WIP in Advanced Manufacturing
In conclusion, Warm Isostatic Pressing (WIP) stands out as a pivotal technology in advanced manufacturing, offering unparalleled enhancements in material properties through its sophisticated application across various industries. The advancements in WIP technology, coupled with its diverse applications and significant benefits, underscore its critical role in achieving superior material density, microstructure uniformity, and mechanical properties. As we look to the future, WIP's integration with emerging technologies and materials promises to further revolutionize material processing techniques, ensuring its continued relevance and innovation in the field of advanced manufacturing.
CONTACT US FOR A FREE CONSULTATION
KINTEK LAB SOLUTION's products and services have been recognized by customers around the world. Our staff will be happy to assist with any inquiry you might have. Contact us for a free consultation and talk to a product specialist to find the most suitable solution for your application needs!