Introduction
Isostatci pressing is a method of compacting powder or granulated materials into a desired shape and density. This process involves applying pressure uniformly from all directions to the material, typically using a fluid medium such as gas or liquid. Isostatic pressing is commonly used in the manufacturing of ceramics, metals, and composites. In the field of oxygen sensors, isostatic pressing is a popular technique for producing high-quality, reliable sensors with excellent sensitivity and stability. In this article, we will explore the advantages of using isostatic pressing for oxygen sensors.
Table of Contents
What is Isostatic Pressing
Isostatic pressing is a technique that applies uniform, equal force over the entire product, regardless of shape or size. This process is used to create dense, uniform materials that are ideal for a wide range of applications. The process involves the application of equal pressure to a compacted powder to achieve optimal density and microstructure uniformity. Through this process, the press uses a gas or liquid to deliver force to a hermetically sealed container filled with the metal powder using either elevated or ambient temperatures. These processes are known as hot and cold isostatic pressing, respectively.
Types of Isostatic Pressing
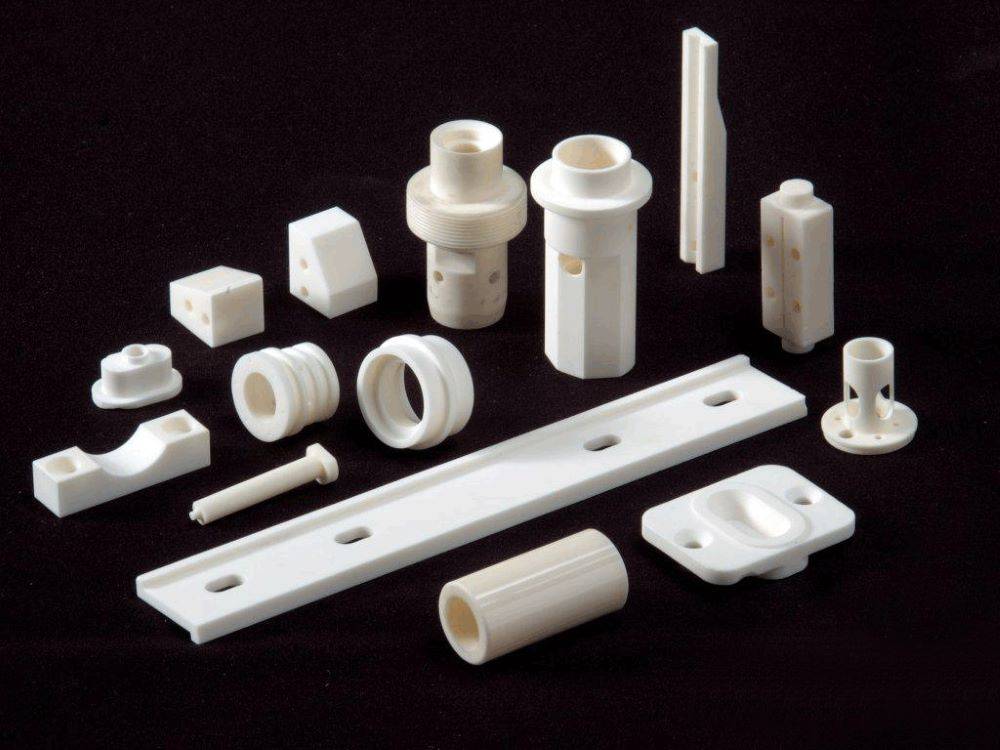
There are three basic types of isostatic pressing: cold isostatic pressing (CIP), warm isostatic pressing (WIP), and hot isostatic pressing (HIP). Cold isostatic pressing is applied to consolidate ceramic or refractory powders loaded into elastomeric bags. Warm isostatic pressing differs from CIP only in that shapes are pressed at warm temperature to about 100°C. Hot isostatic pressing involves both temperature and pressure applied simultaneously to obtain fully dense parts (to 100% theoretical density), and it is used mainly for engineered ceramics requiring optimum properties for high-performance applications.
Advantages of Isostatic Pressing
Isostatic pressing has many advantages over other methods of creating materials. It allows for greater control over the final product, improved consistency and uniformity, and the ability to create more complex shapes and designs. Additionally, isostatic pressing allows for greater control over the density of the final product, which can be critical in applications where precision is paramount. Powder is compacted with the same pressure in all directions, and, since no lubricant is needed, high and uniform density can be achieved. The process removes many of the constraints that limit the geometry of parts compacted unidirectionally in rigid dies. It is applicable to difficult-to-compact and expensive materials such as superalloys, titanium, tool steels, stainless steel, and beryllium, with material utilization that is highly efficient.
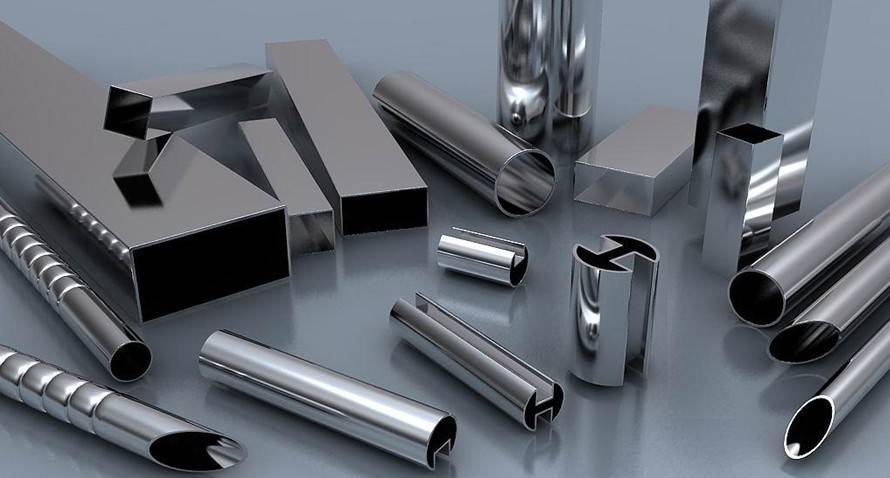
Applications of Isostatic Pressing
Isostatic pressing is widely used in many industries such as pharmaceuticals, explosives, chemicals, food, nuclear fuel, and ferrites. It is one of the most widely used pharmaceutical processing machines. The use of this pressurizing system ensures a uniform compaction pressure throughout the powder mass and a homogeneous density distribution in the final product. The rapidly growing aerospace and defense industry is significantly contributing to the growth of the isostatic pressing market. In the aerospace industry, it is used for manufacturing aerospace castings, jet aircraft engine components, and turbine blades. In the defense industry, it is used in the production of bulletproof materials, gun parts, and others.
In summary, isostatic pressing is an important technique used to create dense, uniform materials with greater control over the final product, improved consistency, and uniformity. It is applicable to difficult-to-compact and expensive materials with material utilization that is highly efficient. It has many applications in various industries such as pharmaceuticals, explosives, chemicals, food, nuclear fuel, and ferrites.
Types of Isostatic Pressing
Isostatic pressing has two primary types: Cold Isostatic Pressing (CIP) and Hot Isostatic Pressing (HIP). The main difference between the two is the temperature and pressure applied during the process.
Cold Isostatic Pressing (CIP)
Cold isostatic pressing involves compacting a dry or semi-dry powder in an elastomeric mold submerged in a pressurized liquid. It is done at ambient temperature and is typically used to produce parts that are not subjected to high temperatures or pressures. CIP is used to consolidate ceramic or refractory powders loaded into elastomeric bags. It is the preferred method for temperature-sensitive materials such as ceramics, metal powders, etc. CIP is also suitable for low-volume production of specialty parts, for prototyping, and for research and development. The process is highly efficient and produces components that are strong, durable, and have excellent electrical properties. Cold isostatic pressing offers several advantages over conventional pressing methods, including higher density, uniformity, and improved structure.
Hot Isostatic Pressing (HIP)
Hot isostatic pressing, on the other hand, is done at high temperatures and pressures and is used to produce components that require high strength and durability. It involves both temperature and pressure applied simultaneously to obtain fully dense parts, to 100% theoretical density, and is used mainly for engineered ceramics requiring optimum properties for high-performance applications. The process of hot isostatic densification can be divided into two stages. The first stage is the internal defects and pores in the external pressure are greater than the material high temperature strength of the conditions of plastic deformation, defects, and pores are destroyed, resulting in the internal surface contact with each other. The second stage is in the external pressure is lower than the material high temperature strength, the material undergoes high-temperature creep, while contact with the alloy surface mutual penetration, diffusion bonding, completely eliminate defects and porosity are completely eliminated. Hot isostatic pressing allows for the production of components with uniform density, which is essential for achieving accurate and reliable measurements. Additionally, it can be used to produce complex shapes and structures that would be difficult or impossible to achieve using other methods.
In summary, both CIP and HIP are highly effective methods of isostatic pressing that produce components with unique properties suited for different applications. Cold isostatic pressing is suitable for low-temperature materials and low-volume production, while hot isostatic pressing is suitable for high-temperature materials and high-performance applications.
Advantages of Isostatic Pressing
Uniform Density and Improved Accuracy
Isostatic pressing creates a uniform density of the sensor material, which improves its accuracy and sensitivity. The uniform pressure applied from all directions eliminates the formation of air pockets and defects in the sensor, which can affect its performance.
Enhanced Strength and Durability
Isostatic pressing improves the overall strength and durability of the sensor, making it more resistant to damage from handling or use. The process creates a uniform density, which makes the sensor material stronger and more durable.
Cost-Effective Production
Isostatic pressing provides a cost-effective alternative to other manufacturing methods, making it an attractive option for companies looking to produce high-quality oxygen sensors without breaking the bank.
Complex Sensor Shapes
Isostatic pressing can be used to create complex sensor shapes that would otherwise be difficult to achieve using other manufacturing methods. The technique is highly versatile and can be used to produce a wide range of shapes and dimensions.
Scalability and Efficiency
Isostatic pressing is scalable, meaning that manufacturers can create multiple sensors simultaneously, reducing production time and increasing efficiency. This technique is especially useful for producing large quantities of sensors in a short period.
Enhanced Alloying Possibilities
Isostatic pressing allows the enhancement of alloying elements without inducing segregation in the material, enabling the production of sensors with improved mechanical properties.
Improved Wear and Corrosion Resistance
Isostatic pressing improves wear and corrosion resistance via the hot isostatic pressing PM route through cladding, extended alloying possibilities, control of grain size and shape, and producing homogeneous microstructures.
Low Tooling Cost
For short production runs, the tooling cost is low in comparison to other manufacturing methods.
Reduction in Welds
Components can be designed and fabricated with a reduction, or complete elimination, in the number of welds and related inspections.
Consistency of Mechanical Properties
Hot Isostatic Pressing Casting improves the consistency of mechanical properties, increasing tensile strength, impact strength, and ductility.
Overall, Isostatic pressing is a powerful tool in the fabrication of oxygen sensors, providing numerous advantages that make it a preferred method for many manufacturers. It offers improved accuracy and sensitivity, enhanced strength and durability, cost-effective production, scalability and efficiency, and the ability to produce complex shapes and dimensions.
Oxygen Sensors
Oxygen sensors are essential components of many industrial and automotive applications. They are used to monitor the amount of oxygen in gas mixtures, which is critical for optimizing combustion processes, reducing emissions, and ensuring safety. Isostatic pressing is a crucial manufacturing process used in the production of oxygen sensors.
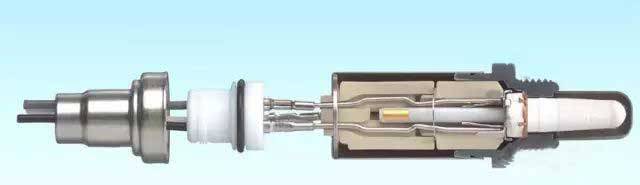
The Importance of Precision
Oxygen sensors need to fit into tight spaces and have precise dimensions to function properly. Isostatic pressing allows for the production of complex shapes with high precision. This precision is crucial for ensuring that the oxygen sensor functions accurately and reliably.
Ensuring Durability and Reliability
Isostatic pressing ensures that the material is evenly compressed, which results in a high-density oxygen sensor that is more durable and reliable. The high-density oxygen sensor is less susceptible to damage or failure due to environmental factors, such as temperature or vibration.
Versatility in Materials
Isostatic pressing can be used with a wide variety of materials, including ceramics and metals, which makes it a versatile manufacturing process for oxygen sensors. This versatility allows for the production of oxygen sensors that can withstand different environments and conditions.
Flexible Geometries
Isostatic pressing can be used to create oxygen sensors with a variety of geometries, such as cylindrical shapes or even custom shapes, which makes it a flexible process for meeting various design requirements. This flexibility allows for the production of oxygen sensors that fit specific applications and environments.
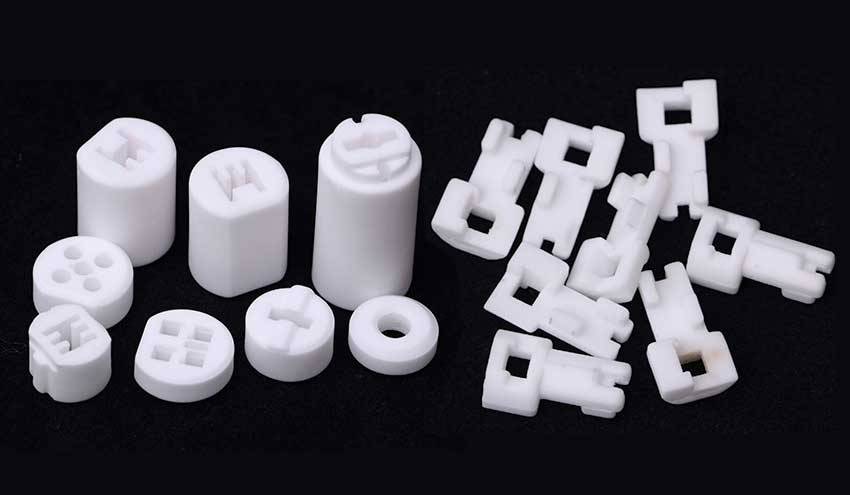
In summary, the use of isostatic pressing for oxygen sensors offers numerous advantages, including precision, durability, reliability, versatility, and flexibility, which makes it an ideal manufacturing process for producing high-quality oxygen sensors.
Advantages of Using Isostatic Pressing for Oxygen Sensors
Isostatic pressing is a popular manufacturing technique used in the production of high-quality oxygen sensors. This process involves applying equal pressure from all directions to a powdered material, resulting in a uniform and dense structure. Compared to other production methods, isostatic pressing offers several advantages for oxygen sensor manufacturing.
Precise Dimensions
Isostatic pressing allows for the production of sensors with precise dimensions, which is crucial for accurate measurements. This technique also results in a highly consistent and uniform density throughout the sensor, which improves its sensitivity and durability.
High Purity Level
Isostatic pressing can produce sensors with a higher purity level due to the reduced risk of contamination during the manufacturing process. This purity is essential for oxygen sensors used in critical applications, such as medical devices.
Versatility
Isostatic pressing enables the production of complex sensor shapes and sizes, making it a versatile option for manufacturers. This technique can produce sensors with a range of geometries, including hollow tubes, blocks, and crucibles.
Consistency
The uniform pressure applied in isostatic pressing results in a highly consistent and uniform density throughout the sensor, which improves its sensitivity and durability. This consistency is particularly important for oxygen sensors used in critical applications, such as medical devices.
Reduction of Internal Stresses
Advantages of cold isostatic presses include the creation of products with uniform density, which leads to a reduction of internal stresses, eliminating cracks, strains, and laminations. They also press products that have a higher “green strength” which allows for close tolerances, complex shapes, and better machinability.
Production of High-Quality Ceramic Bodies
Dry bag isostatic pressing is an efficient production method for small parts with axisymmetric shapes. It is used to produce high-quality ceramic bodies for spark plugs. Since the rubber tooling is integrated into the apparatus, separate immersion and removal steps are not needed, which leads to ease in automation and fast production rates.
In conclusion, the advantages of using isostatic pressing for oxygen sensors make it an attractive option for manufacturers looking to produce high-quality sensors that meet the rigorous standards of various industries. Isostatic pressing allows for the production of sensors with precise dimensions, a high purity level, and complex shapes and sizes. It also provides a highly consistent and uniform density throughout the sensor, which improves its sensitivity and durability.
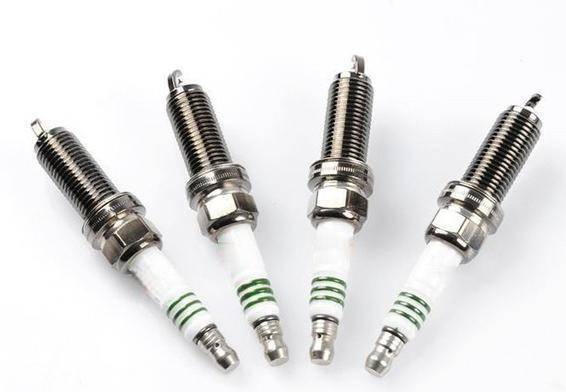
Conclusion
In conclusion, isostatic pressing offers numerous advantages in the production of oxygen sensors. This method of powder compaction enables the production of sensors with uniform density and microstructure, resulting in improved accuracy and stability of the sensors. Isostatic pressing also allows for the production of complex shapes and sizes, making it ideal for manufacturing oxygen sensors with intricate designs. Additionally, isostatic pressing can be done with various materials, further increasing the versatility of this method. Overall, using isostatic pressing for oxygen sensors results in higher quality and more reliable products, making it a popular choice in the industry.
CONTACT US FOR A FREE CONSULTATION
KINTEK LAB SOLUTION's products and services have been recognized by customers around the world. Our staff will be happy to assist with any inquiry you might have. Contact us for a free consultation and talk to a product specialist to find the most suitable solution for your application needs!