Densification Treatment
Elimination of Internal Defects
Hot isostatic pressing (HIP) is a transformative technology that significantly enhances the performance of various castings by eliminating internal defects. This process is particularly effective for materials such as aluminum alloys, titanium alloys, and high-temperature alloys, which are critical in industries demanding high reliability and performance.
By applying uniform pressure and heat, HIP densifies these materials, effectively closing pores and microcracks that could otherwise lead to premature failure. This densification process not only removes existing defects but also prevents the formation of new ones, ensuring a more uniform and dense material structure.
The benefits of HIP in defect elimination are manifold. For instance, aluminum alloys, known for their lightweight and high strength, become even more robust and durable after HIP treatment. Similarly, titanium alloys, which are essential in aerospace and medical applications, achieve superior mechanical properties, making them more suitable for high-stress environments. High-temperature alloys, used in jet engines and gas turbines, experience a significant boost in their resistance to thermal fatigue and oxidation, thereby extending their operational life.
In summary, HIP's ability to eliminate internal defects elevates the overall performance of castings to an unprecedented level, making it an indispensable technology in modern manufacturing.
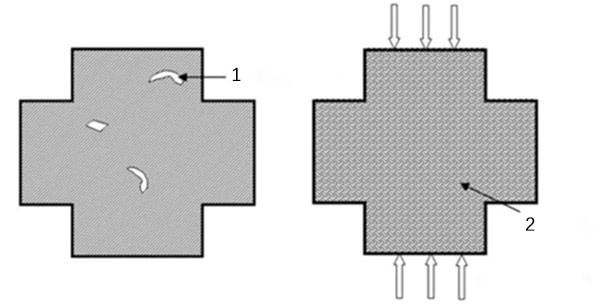
Improvement in Mechanical Properties
The enhancement of mechanical properties through hot isostatic pressing (HIP) is a significant advancement in material science. This process notably increases the fatigue life, ductility, fracture toughness, wear resistance, and corrosion resistance of materials, ultimately achieving 100% theoretical density. These improvements are not merely incremental but transformative, allowing materials to withstand harsher conditions and longer operational durations.
For instance, the fatigue life of components is extended, meaning they can endure repeated stress cycles without failure. This is crucial in applications where mechanical parts are subject to continuous or intermittent stress, such as in aerospace or automotive industries. Ductility, the ability of a material to deform under tensile stress, is also enhanced, making the material more adaptable to various forms and shapes without cracking or breaking.
Fracture toughness, a measure of a material's resistance to crack propagation, is significantly improved. This means that materials treated with HIP are less likely to develop cracks under stress, which is vital in high-stress environments like heavy machinery or structural engineering. Wear resistance is another critical property enhanced by HIP, ensuring that components maintain their integrity over extended periods of friction and contact.
Corrosion resistance is also a notable benefit, protecting materials from environmental degradation. This is particularly important in industries where components are exposed to corrosive elements, such as marine or chemical processing environments. The achievement of 100% theoretical density ensures that the materials are free from porosity and other internal defects, leading to a more reliable and durable product.
In summary, the mechanical properties of materials subjected to hot isostatic pressing are markedly improved across multiple dimensions, making them suitable for a wide range of high-performance applications.
Diffusion Bonding
Integration of Multiple Materials
Hot isostatic pressing (HIP) excels in creating seamless and robust connections between various materials, including solid-solid, solid-powder, and powder-powder interfaces. This advanced technique ensures that the junctions formed are not only defect-free but also exhibit superior mechanical performance. The process leverages high temperatures and uniform pressure to facilitate diffusion bonding, which is crucial for integrating materials with disparate properties.
One of the key advantages of HIP in material integration is its ability to handle materials with significant performance differences. For instance, it can effectively bond high-temperature alloys with more common metals, creating composites that leverage the strengths of each component. This versatility is particularly beneficial in industries requiring complex material combinations, such as aerospace and automotive engineering.
Moreover, HIP's precision in controlling dimensional aspects during the bonding process ensures that the final product maintains its intended shape and size. This level of control is essential for applications where component integrity is paramount, such as in critical structural parts. The process's ability to achieve near-perfect density and eliminate internal voids further enhances the reliability and longevity of the integrated materials.
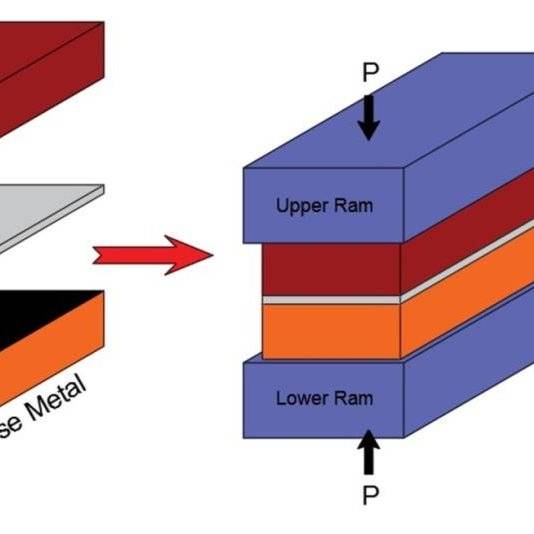
In summary, HIP's capability to create high-performance, defect-free junctions between diverse materials makes it an indispensable tool in modern manufacturing. Its superior bonding strength and dimensional accuracy offer significant advantages over traditional methods, making it a preferred choice for industries demanding the highest standards of material integrity and performance.
Advantages Over Traditional Methods
Hot isostatic pressing (HIP) technology stands out from traditional methods in several key aspects, particularly in its ability to achieve superior bonding strength, precise dimensional control, and the seamless integration of materials with vastly different performance characteristics. Unlike conventional bonding techniques, HIP creates defect-free junctions by applying uniform pressure and heat, which minimizes the risk of weak spots and ensures a robust connection.
One of the most significant advantages of HIP is its ability to handle materials with significant performance differences. Whether it's connecting metals with varying degrees of hardness, ductility, or thermal resistance, HIP ensures that the final product maintains its integrity and performance. This versatility is particularly valuable in industries where material performance is critical, such as aerospace and automotive engineering.
Moreover, HIP offers unparalleled dimensional control, which is crucial for creating components that meet exacting specifications. The process allows for the precise shaping and sizing of materials, reducing the need for additional machining and minimizing waste. This not only enhances the efficiency of the manufacturing process but also contributes to cost savings and environmental sustainability.
In summary, HIP's ability to deliver superior bonding strength, precise dimensional control, and the seamless integration of diverse materials makes it a superior choice over traditional methods. This technology not only ensures the production of high-performance components but also optimizes the manufacturing process, making it a valuable tool in various industrial applications.
Powder Metallurgy Near-Net Forming
High-Performance and Cost-Effective Forming
Hot isostatic pressing (HIP) is a transformative technology that consolidates powdered materials into high-performance, near-net shape products. This process not only maximizes material utilization but also enhances the mechanical properties of the final product. By applying uniform pressure at elevated temperatures, HIP ensures that the powdered materials are uniformly densified, resulting in components with superior mechanical integrity and performance.
The cost-effectiveness of HIP lies in its ability to minimize material waste and reduce the need for extensive post-processing. Traditional manufacturing methods often require additional machining to achieve the desired shape, which can lead to significant material loss. In contrast, HIP allows for the production of near-net shape components directly from powdered materials, thereby reducing both material waste and manufacturing costs.
Moreover, the mechanical properties of components formed through HIP are exceptional. The process ensures that the final product exhibits high strength, ductility, and resistance to wear and corrosion. These properties are crucial for applications in aerospace, automotive, and other high-performance industries where reliability and longevity are paramount.
In summary, HIP offers a high-performance and cost-effective solution for forming complex, near-net shape components from powdered materials, making it an indispensable technology in modern manufacturing.

Uniform and Dense Material Structure
Hot isostatic pressing (HIP) technology plays a pivotal role in achieving a uniform and dense material structure, which is critical for the performance of various components. This process ensures that the material exhibits isotropic mechanical properties, meaning that its strength, ductility, and other mechanical characteristics are consistent in all directions. This uniformity is particularly important in applications where directional properties could lead to failure under stress.
One of the key advantages of HIP is its ability to eliminate element segregation, a common issue in traditional manufacturing methods. Element segregation occurs when the elements within an alloy do not distribute evenly, leading to weak spots and inconsistencies in the material. By applying uniform pressure and heat, HIP effectively redistributes these elements, resulting in a more homogeneous material.
Moreover, HIP is capable of preparing high-temperature alloy materials and bimetallic ingots with exceptional properties. High-temperature alloys, which are often used in aerospace and energy sectors, require a stable and consistent microstructure to withstand extreme conditions. Bimetallic ingots, on the other hand, benefit from the seamless integration of two different metals, which is made possible by HIP's precise control over temperature and pressure.
In summary, HIP's ability to create a uniform and dense material structure not only enhances the mechanical properties of the material but also broadens its applicability in demanding industries.
CONTACT US FOR A FREE CONSULTATION
KINTEK LAB SOLUTION's products and services have been recognized by customers around the world. Our staff will be happy to assist with any inquiry you might have. Contact us for a free consultation and talk to a product specialist to find the most suitable solution for your application needs!