Definition and Principles of Cold Isostatic Pressing
Table of Contents
- Definition and Principles of Cold Isostatic Pressing
- Advantages of Cold Isostatic Pressing
- Achievement of uniform density in materials
- Achievement of uniform strength in materials
- Versatility of cold isostatic pressing
- Increased corrosion resistance in materials
- Improvement of mechanical properties
- Applications in powder metallurgy
- Production of refractory metals
- Role in the sintering process
- Types of Cold Isostatic Pressing
Explanation of cold isostatic pressing
Cold isostatic pressing (CIP) is a method of processing materials. It involves compacting powders by enclosing them in an elastomer mold and applying uniform liquid pressure to compress the mold. This results in a highly compact solid. Cold isostatic pressing is commonly used for plastics, graphite, powdered metallurgy, ceramics, sputtering targets, and other materials.
How cold isostatic pressing works based on Pascal's law
Cold isostatic pressing works based on Pascal's law, which states that pressure applied in an enclosed fluid is transmitted in all directions throughout the fluid without any change in the magnitude of the pressure. In CIP, the elastomer mold has low resistance to deformation, allowing the pressure to be uniformly transmitted and compress the powders into a solid form.
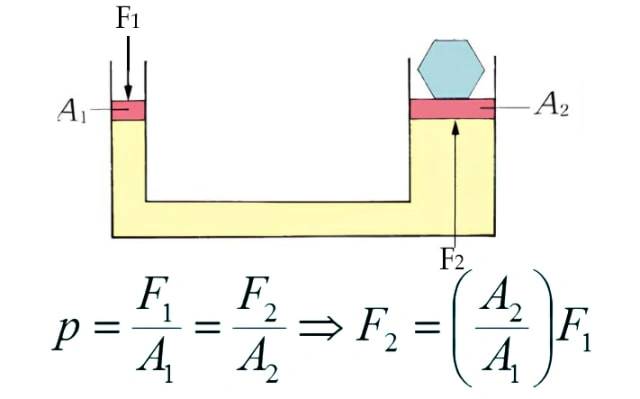
Process involved in cold isostatic pressing
The process of cold isostatic pressing starts by enclosing the powders in an elastomer mold. The mold is then subjected to uniform liquid pressure, usually using water, oil, or a glycol mixture. The pressure applied is typically between 100-600 MPa. This pressure compacts the powders and forms a "raw" part with sufficient strength for handling, processing, and further sintering to achieve final strength.
Materials and processes suitable for cold isostatic pressing
Cold isostatic pressing is suitable for a variety of materials, including plastics, graphite, powdered metallurgy, ceramics, and sputtering targets. It is commonly used to provide blanks for further sintering or hot isostatic pressing processes. In terms of density, cold isostatic pressing can achieve a theoretical density of about 100% for metals and about 95% for ceramic powders.
In summary, cold isostatic pressing is a method used to process materials by compacting powders using uniform liquid pressure. It is based on Pascal's law and involves using an elastomer mold to enclose the powders. Cold isostatic pressing is suitable for various materials and is commonly used to provide blanks for further processing.
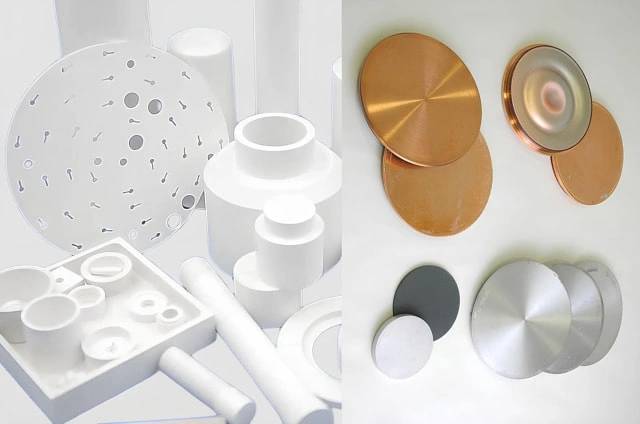
Advantages of Cold Isostatic Pressing
Achievement of uniform density in materials
- Cold isostatic pressing ensures that materials have a uniform density.
- This results in uniform shrinkage during other processes such as sintering.
- The pressure used in CIP reaches every part of the material with equal magnitude.
Achievement of uniform strength in materials
- The pressure used to compact the materials is equal in all directions, resulting in uniform strength.
- Materials with uniform strength are more efficient and reliable.
Versatility of cold isostatic pressing
- CIP can produce difficult shapes that are challenging or impossible to produce by other methods.
- It can also be used to produce large-sized materials.
- The only limitation is the size of the pressure vessel.
Increased corrosion resistance in materials
- Cold isostatic pressing improves the corrosion resistance of materials.
- Materials that undergo this process have a longer lifespan compared to others.
Improvement of mechanical properties
- Cold isostatic pressed materials have improved mechanical properties, such as ductility and strength.
- This leads to better performance and durability in industrial applications.
Applications in powder metallurgy
- CIP is used in the compacting step of powder metallurgy before sintering.
- It enables the production of complex shapes and dimensions.
Production of refractory metals
- CIP is used to produce refractory metals like tungsten, molybdenum, and tantalum.
- These metals have high melting points and are resistant to wear and tear.
Role in the sintering process
- Cold isostatic pressing is performed before sintering.
- The high green strength of CIP products allows for faster sintering compared to other materials.
6 KEY ADVANTAGES OF COLD ISOSTATIC PRESSING VERSUS UNIAXIAL PRESSING
- More uniform product properties, greater homogeneity, and more precise control of the finished product dimensions.
- Greater flexibility in the shape and size of the finished product.
- Longer aspect ratios possible, allowing for long thin pellets.
- Improved compaction of the powder, leading to improved densification.
- Ability to process materials with different characteristics and shapes.
- Reduced cycle times and improved productivity.
Advantages of Using Hot Isostatic Pressing Tools
- Hot isostatic pressing tools offer several advantages in various industries:
- Improve mechanical properties in metals, enhancing performance and durability.
- Reduce or eliminate voids, resulting in a more reliable surface.
- Consolidate powders into specific parts and components.
- Bond dissimilar metals to create cost-effective components.
Cold Isostatic Pressing
- Cold isostatic pressing is advantageous for producing parts where the high initial cost of pressing dies cannot be justified.
- It allows for the production of very large and complex spare parts.
- The uniform density distribution is a key driver for the growth of isostatic pressing systems globally.
- It also reduces human error and pressing flaws.
Advantages of Cold Isostatic Pressing for ITO Targets
- Cold isostatic pressing has advantages for the preparation of ITO targets:
- Suitable for pressing large-sized powder products due to its large pressure and uniform stress.
- Pressed powder products have high density and uniformity.
- No need for the addition of lubricants.
- Low production cost, suitable for mass production.
Cold isostatic pressing is a versatile and beneficial technique that offers advantages such as achieving uniform density and strength in materials, versatility in shape and size, increased corrosion resistance, improved mechanical properties, and various applications in powder metallurgy and production of refractory metals. It is a valuable method for achieving high-quality components in various industries.
Types of Cold Isostatic Pressing
Explanation of Wet Bag Isostatic Pressing
In the wet bag process, the powder material is enclosed in a flex mold bag and submerged into a high-pressure liquid in a pressure vessel. Isostatic pressure is then applied to the outer surfaces of the mold to compress the powder into a desired shape. This method is ideal for multi-shape and small to large quantity production, as well as the pressing of large products.
Explanation of Dry Bag Isostatic Pressing
Dry bag isostatic pressing involves fixing the mold in the pressure vessel and filling it with powder. Isostatic pressure from the pressure liquid is then applied to the external surface of the mold, compressing the powder into a solid mass with a compact microstructure. This method is faster than wet bag pressing and is suitable for mass production of materials.
Comparison between Wet and Dry Bag Isostatic Pressing
Wet bag isostatic pressing is relatively slow, taking 5 to 30 minutes to process material. However, improvements in high-volume pumps and loading mechanisms can speed up the process. On the other hand, dry bag isostatic pressing is faster and better suited for mass production. It is also more ideal for producing small carbide articles with axisymmetric geometry.
Use of Dry Bag Isostatic Pressing in the Production of Tungsten Carbide Rods
Dry bag isostatic pressing is commonly used in the production of tungsten carbide rods. This method allows for high forming pressure and fast pressing, resulting in compact tungsten carbide bars. After dry bag isostatic pressing, the bars are ground before sintering, and then they can be sintered directly. This process is efficient and cost-effective for producing tungsten carbide rods.
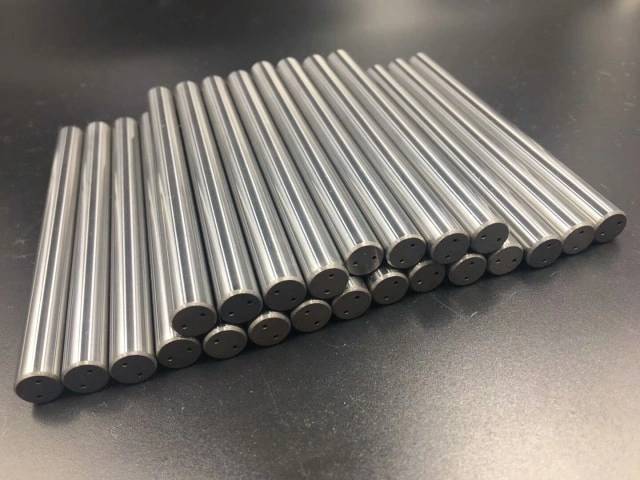
Overall, cold isostatic pressing offers advantages such as uniform density and strength, versatility in producing difficult shapes, improved corrosion resistance and mechanical properties, and its use in powder metallurgy and refractory metals. The choice between wet and dry bag isostatic pressing depends on the specific requirements and goals of the production process.
CONTACT US FOR A FREE CONSULTATION
KINTEK LAB SOLUTION's products and services have been recognized by customers around the world. Our staff will be happy to assist with any inquiry you might have. Contact us for a free consultation and talk to a product specialist to find the most suitable solution for your application needs!