Introduction
Table of Contents
Cold Isostatic Pressing (CIP) is a unique technique used in the manufacturing industry for compacting and shaping materials. It involves subjecting a material to uniform pressure from all directions, resulting in a highly dense and uniform product. CIP is particularly useful for machining and metal forming tools, as well as for large parts that don't require high precision. By utilizing this method, manufacturers can produce high-integrity billets or preforms without the risk of distortion or cracking during the firing process. In this article, we will explore the features and advantages of Cold Isostatic Pressing, specifically focusing on its electrical variant.
The Concept of Cold Isostatic Pressing (CIP)
Definition of CIP
Cold isostatic pressing (CIP) is a method of compacting powdered materials into a solid homogeneous mass before machining or sintering. In CIP, the powder is subjected to equal pressure from all directions, resulting in high-integrity billets or preforms with little distortion or cracking when fired. This process is sometimes referred to as hydrostatic pressing.
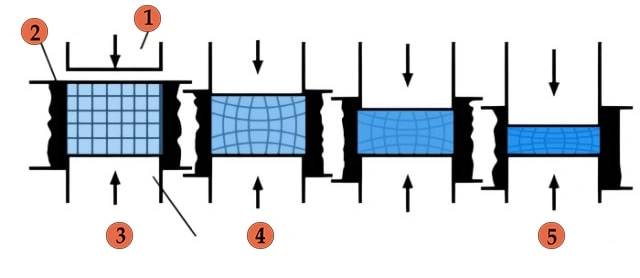
Use of CIP in machining and metal forming tools
CIP is commonly used in the production of wear and metal forming tools. It allows for the compaction of powdered materials that are too large to be pressed in uniaxial presses. By subjecting the powder to equal pressure from all directions, CIP ensures uniform compaction and minimizes distortion or cracking. This makes it an effective method for producing high-quality tools with accurate dimensions.
CIP as a solution for large parts that do not require high precision
CIP is particularly suitable for parts that are too large to be pressed in traditional presses and do not require high precision in the sintered state. It offers a simple and cost-effective solution for compacting powdered materials into solid homogeneous masses. The resulting parts may not have the same level of precision as those produced using other methods, but they are still suitable for applications where high precision is not necessary.
Please note that the content provided is for informational purposes only and should not be considered as professional advice.
Features of Cold Isostatic Pressing
Reference to hydrostatic pressing
Cold isostatic pressing (CIP) is a process that involves compacting green parts at ambient temperatures using hydrostatic conditions. Unlike uniaxial pressing, CIP applies pressure equally in all directions, reducing die wall friction and achieving maximum uniformity of density and microstructure. This method utilizes elastomeric molds, and the pressure is transmitted to the part via a liquid. CIP is also known as cold isostatic pressing to distinguish it from hot isostatic pressing (HIP), which is carried out at high temperatures.
Production of high-integrity billets or preforms
CIP is used to produce very large and complex spare parts where the initial cost of hot isostatic pressing is unjustified. This process ensures a uniform density distribution, which is crucial for the production of high-integrity billets or preforms. The use of elastomeric molds allows for the production of complex shapes, although the achievable dimensional tolerances are typically near-net due to the flexible nature of the molds. By applying pressure uniformly over the entire surface of the mold, CIP eliminates die-wall friction and achieves more uniform densities.
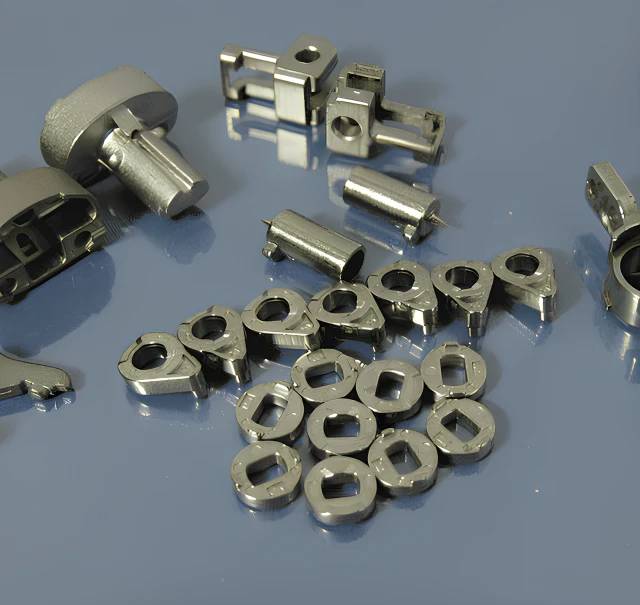
Prevention of distortion or cracking when fired
One of the advantages of CIP is the prevention of distortion or cracking when the green compact is fired. The powder is compacted to a very uniform density, which reduces the likelihood of defects such as pores, cracks, and segregation in the final product. This results in improved material performance, service life, and stability. CIP is particularly beneficial for materials used in extreme working environments, such as power units and submarine oil pipelines, where the failure of materials can have serious consequences.
In summary, Cold Isostatic Pressing is a valuable manufacturing process that offers several advantages. It allows for the production of high-integrity billets or preforms, prevents distortion or cracking when fired, and ensures a uniform density distribution. While CIP may have limitations in terms of dimensional tolerances, it is an effective method for achieving optimal material performance in various industries and applications.
Advantages of Electrical CIP over Manual CIP
Superior pressure control
Electrical CIP (CIP stands for Cold Isostatic Pressing) offers several advantages over manual CIP processes. One of the key advantages is superior pressure control. The door locking system of electrical CIP is engineered for high-pressure operations, increasing the door seal lifetime. This ensures a tight seal and prevents any leakage during the pressing process.
In addition, electrical CIP utilizes a high vacuum pumping system, which is based on mechanical and oil diffusion pumps. Optional turbomolecular or cryogenic pumps are also available for achieving even higher levels of vacuum. This superior vacuum system allows for a more efficient and uniform gas flow through the load, resulting in better overall pressure control.
Another advantage of electrical CIP is its universal furnace, which has a wide range of applicable technologies. This furnace enables the heat treatment of various materials, including steel and alloys, as well as hard brazing. It complies with industry specifications such as SAE AMS and MIL-8-99728, making it suitable for use in the aerospace and power generation industries.
Furthermore, electrical CIP meets both European and North American safety standards, ensuring a safe operating environment for users.
Control system advantages
The control system of electrical CIP provides several key advantages, especially in a laboratory setting. These advantages include reduced cost, faster loading and unloading, and a larger chamber diameter compared to piston-style CIP machines. Despite its larger size, electrical CIP is five times lighter than traditional machines, eliminating the need for additional heavy presses.
Additionally, electrical CIP requires reduced maintenance due to its use of a static O-ring instead of a dynamic O-ring. This prolongs the O-ring's lifespan, as it is not subjected to the wear and tear caused by sliding motion. Moreover, the compact design of electrical CIP saves space in the laboratory and allows for easy movement between labs if required.
Operating electrical CIP is also easy, making it accessible to laboratory professionals with varying levels of expertise.
Examples of when CIP might be used in the lab
Electrical CIP is particularly useful in specific laboratory scenarios. Here are some examples of when CIP might be used:
-
When you want to reach a higher density before sintering: Electrical CIP allows for achieving a higher density in powder compaction, which is beneficial before the sintering process.
-
When your pellet keeps falling apart before sintering: If your powder pellet tends to disintegrate during the pressing process, electrical CIP can provide a solution by ensuring better compaction.
-
When you have a large aspect ratio: Electrical CIP is suitable for pressing long and thin items with a large aspect ratio, such as a 5 mm diameter ceramic rod that is 100 mm long.
-
When pressing an irregular shape: Electrical CIP is effective for pressing irregular shapes, such as donuts or shapes with changing dimensions along their length.
Cold isostatic press
In industries like cemented carbide, ceramics, and magnetic materials, electrical CIP is widely used for powder forming due to its efficiency and reliability.
Overall, electrical CIP offers superior pressure control, reduced cost, faster processing times, and improved product quality. It is an excellent choice for laboratory professionals looking to optimize their powder compaction processes.
Conclusion
In conclusion, Cold Isostatic Pressing (CIP) offers numerous advantages in the field of machining and metal forming tools. Its ability to produce high-integrity billets or preforms and prevent distortion or cracking when fired makes it a valuable technique for manufacturing large parts. Furthermore, the use of Electrical CIP provides superior pressure control, enhancing the precision and efficiency of the process. Overall, CIP proves to be a reliable and effective solution for businesses in need of high-quality components without compromising on size or complexity. Embracing this technology can lead to improved productivity and cost-effectiveness in various industries.
CONTACT US FOR A FREE CONSULTATION
KINTEK LAB SOLUTION's products and services have been recognized by customers around the world. Our staff will be happy to assist with any inquiry you might have. Contact us for a free consultation and talk to a product specialist to find the most suitable solution for your application needs!