Brief History of Isostatic Pressing
Table of Contents
Isostatic pressing is a process that was pioneered in the mid-1950s and has since become a widely used production tool in various industries. Originally considered a research curiosity, it is now applied for consolidation of powders and defect healing of castings in materials such as ceramics, metals, composites, plastics, and carbon.
The main advantage of isostatic pressing is its ability to apply a uniform, equal force over the entire product, regardless of its shape or size. This feature makes it particularly beneficial for ceramic and refractory applications. By forming product shapes to precise tolerances, the process reduces the need for costly machining, making it commercially attractive.
Isostatic pressing systems utilize fluid (such as water or oil) or gas (typically argon) pressure to modify materials by uniformly pressuring them in all directions. This ensures maximum uniformity of density and can be done at both high temperatures and room temperature.
In the manufacturing and production of various materials, isostatic pressing plays a vital role. This technique involves enclosing a powdered material in a flexible mold or container and applying even pressure on all sides. Typically, a liquid medium like water or oil is used to evenly transfer force to the material. The result is products with increased density, strength, and dimensional accuracy, as the process effectively eliminates voids and air pockets.
Principle of Isostatic Pressing
Isostatic pressing is a process that applies a uniform and equal force over the entire product, regardless of its shape or size. It has become a widely used technique in various industries, including ceramics, metals, composites, plastics, and carbon.
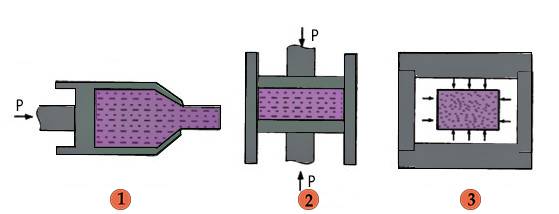
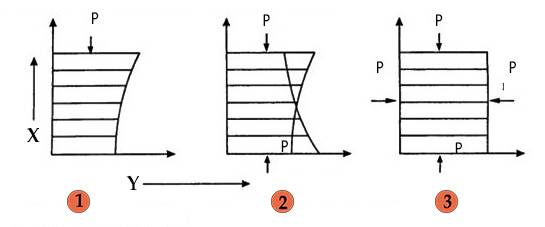
The main advantage of isostatic pressing is its ability to form products with precise tolerances, which reduces the need for costly machining. This process is particularly beneficial for ceramic and refractory applications.
Isostatic Pressing Process
In the isostatic pressing process, products are placed in a closed container filled with liquid and subjected to equal pressure on all surfaces. This high-pressure environment increases the density of the products, allowing them to take on the desired shapes. Isostatic presses are commonly used in the formation of high-temperature refractory materials, ceramics, cemented carbides, lanthanon permanent magnets, carbon materials, and rare metal powders.
Characteristics of Isostatic Pressing Process
Isostatic pressing works by reducing the porosity of powder mixtures, enabling the production of various types of materials. The powder mixture is compacted and encapsulated using isostatic pressure, which applies pressure equally from all directions. This confinement of the powder within a flexible membrane or hermetic container allows for uniform pressure transfer and prevents the escape of the pressurizing medium, whether it is a liquid or gas.
Types of Isostatic Pressing
Isostatic pressing can be performed using high-pressure vessels. The pressure is generated by an incompressible medium, which transfers the pressure uniformly to the samples from all directions. This principle of fluid mechanics ensures that the pressure applied to the samples is uniform and of the same magnitude in all directions within the pressure vessel.
Isostatic pressing has revolutionized the production of various materials, providing a cost-effective and efficient method for achieving precise shapes and densities. Its versatility and ability to work with different materials make it a valuable technique in many industries.
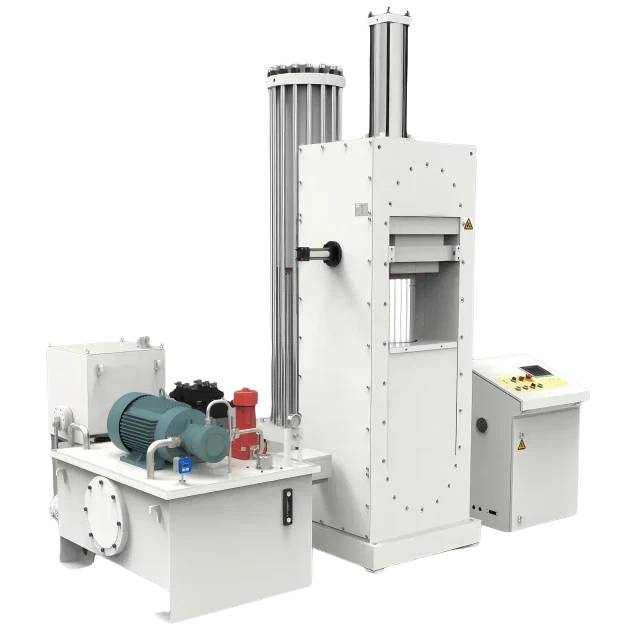
Types of Isostatic Pressing
Cold Isostatic Pressing (CIP)
Cold isostatic pressing (CIP) is a method of applying pressure from multiple directions to achieve greater uniformity of compaction and increased shape capability compared to uniaxial pressing. In CIP, the powder is encased in a rubber mold, which is then subjected to high pressure from all directions. Two methods of carrying out CIP are wet-bag isostatic pressing and dry-bag isostatic pressing.
In wet-bag isostatic pressing, the powder is encased in a rubber sheath and immersed in a liquid that transmits the pressure uniformly to the powder. In dry-bag isostatic pressing, the tooling itself is built with internal channels into which high-pressure fluid is pumped, eliminating the need for immersion in a fluid.
CIP is known for its ability to form complicated shapes that cannot be achieved with uniaxial or machine pressing. The maximum water pressure used in CIP is 400 MPa.
Warm Isostatic Pressing (WIP)
Warm isostatic pressing (WIP) is a variant of cold isostatic pressing that includes a heating element. It uses warm water or a similar medium to apply uniform pressure to powdered products from all directions. WIP enables isostatic pressing at a temperature below the boiling point of the liquid medium.
The WIP process involves heating the liquid medium and continuously injecting it into a sealed pressing cylinder through a booster source. The pressing cylinder is equipped with a heating element to ensure accurate temperature control. This cutting-edge technology utilizes flexible materials as a jacket mold and hydraulic pressure as a pressure medium to shape and press the powder material.
Hot Isostatic Pressing (HIP)
Hot isostatic pressing (HIP) is a material processing method that compresses materials by applying high temperatures and isostatic pressure simultaneously. HIP involves subjecting materials to temperatures ranging from several hundreds to 2000 °C and isostatic pressure ranging from several tens to 200 MPa. The most commonly used pressure medium in HIP is argon.
HIP is different from hot pressing, milling, forging, and extrusion processes as it applies isostatic pressure using gas pressure, whereas the others apply only uniaxial pressure. HIP is a form of heat treatment that uses high pressure to improve material properties. It allows for plastic deformation, creep, and diffusion to occur, resulting in improved mechanical properties by removing defects.
Hot isostatic pressing enables the bonding or cladding of two or more materials together, either in the solid or powder form. It is also used to eliminate internal microporosity in castings for critical applications.
Overall, isostatic pressing techniques, including cold, warm, and hot isostatic pressing, offer unique advantages in achieving uniform compaction, shaping complicated geometries, and improving material properties. These processes play a crucial role in various industries, including manufacturing, aerospace, and automotive sectors.
Working Mechanism of Isostatic Press
Isostatic pressing is a powder processing technique that utilizes fluid pressure to compact a part. Unlike other processes that exert forces on the powder through an axis, isostatic pressing applies pressure equally from all directions. This unique characteristic allows for the production of various types of materials from powder compacts.
The process begins by placing metal powders in a flexible container, which serves as the mold for the part. The container is then sealed, and fluid pressure is exerted over the entire outside surface. This pressure causes the container to press and form the powder into the correct geometry.
The use of all-around pressure in isostatic pressing offers several advantages. Firstly, it enables the powder to be compacted with the same pressure in all directions, resulting in high and uniform density. Additionally, since no lubricant is needed in the process, a high level of material utilization can be achieved. This makes isostatic pressing particularly suitable for difficult-to-compact and expensive materials such as superalloys, titanium, tool steels, stainless steel, and beryllium.
To confine the metal powder within the flexible container and create a pressure barrier, isostatic pressing utilizes a flexible membrane or hermetic container. This membrane separates the powder from the pressurizing medium, which can be either a liquid or a gas.
In the isostatic pressing process, products are placed in a closed container filled with liquid and subjected to equal pressure on all surfaces. This high-pressure environment increases the density of the products, allowing them to take on the required shapes. Isostatic presses are widely used in various industries, including the forming of high-temperature refractory, ceramics, cemented carbide, lanthanum permanent magnet, carbon material, and rare metal powder.
The working mechanism of isostatic pressing relies on the application of pressure from all directions to compact powder materials. This unique approach offers numerous advantages and makes isostatic pressing a versatile and efficient powder processing technique.
Advantages of Isostatic Pressing
Uniform compaction pressure
Isostatic pressing allows for uniform compaction pressure to be applied to the powder in all directions. This results in a compacted piece with uniform shrinkage during sintering or hot isostatic pressing. The uniform pressure also reduces the warpage of the final product.
High and uniform density
Since no lubricant is needed in the isostatic pressing process, high and uniform density can be achieved. The powder is compacted with the same pressure in all directions, resulting in a final product with consistent density throughout.
Applicability to difficult-to-compact and expensive materials
Isostatic pressing is particularly useful for compacting difficult-to-compact and expensive materials such as superalloys, titanium, tool steels, stainless steel, and beryllium. The process allows for efficient material utilization, making it cost-effective for these materials.
Highly efficient material utilization
Isostatic pressing ensures highly efficient material utilization. The powder is compacted with the same pressure in all directions, minimizing material waste and maximizing the use of expensive materials.
Isostatic pressing offers several advantages over other manufacturing methods. It allows for the production of shapes and dimensions that are difficult or impossible to produce by other methods. The process is applicable to a wide range of component sizes, from massive near net PM shapes to small MIM parts. Isostatic pressing also offers low tooling cost for short production runs, reducing production costs. Additionally, it enables the enhancement of alloying possibilities without inducing material segregation.
Isostatic pressing finds application in various industries, including pharmaceuticals, explosives, chemicals, food, nuclear fuel, and ferrites.
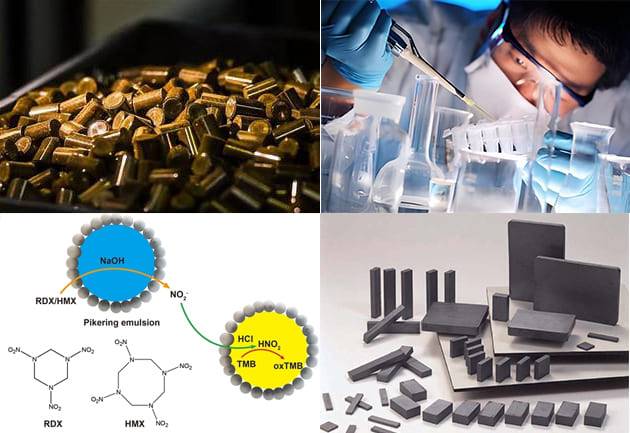
Overall, isostatic pressing provides numerous advantages, including uniform density, shape flexibility, wide component size range, low tooling cost, enhanced alloying possibilities, reduced lead times, and reduced material and machining costs. It is an efficient and cost-effective method for compacting difficult-to-compact and expensive materials.
Applications of Isostatic Press
Isostatic pressing is a versatile manufacturing process that finds applications in various industries. Here are some common applications of isostatic press:
Pharmaceutical Industry
Isostatic pressing is used in the pharmaceutical industry for the production of tablets and other solid dosage forms. The process ensures high and uniform density of the powder, resulting in consistent drug release and improved bioavailability.
Explosives Manufacturing
Isostatic press is utilized in the explosives manufacturing industry for the production of explosive components. The uniform pressure exerted during the process ensures the uniform distribution of explosive materials, enhancing the performance and safety of the final product.
Chemical Industry
In the chemical industry, isostatic pressing is employed for the production of catalysts, filters, and other chemical components. The process allows for the consolidation of difficult-to-compact materials, ensuring high material utilization and improved efficiency.
Food Industry
Isostatic press finds applications in the food industry for the production of food molds and food processing equipment. The process enables the creation of complex shapes with precise tolerances, reducing the need for costly machining and improving the overall quality of food products.
Nuclear Fuel and Ferrites Production
Isostatic pressing is widely used in the nuclear fuel and ferrites production industry. The process is employed for the manufacturing of nuclear fuel pellets, which require high density and mechanical strength. Isostatic press is also utilized for the production of ferrites, which are essential components in various electronic devices.
Isostatic pressing offers several advantages, including high and uniform density, the ability to work with difficult-to-compact materials, and the freedom to create complex shapes. The process is continuously evolving, with advancements in automation and control systems, leading to higher product quality. As the demand for advanced materials continues to grow, the isostatic press market is expected to expand, offering innovative solutions across industries.
CONTACT US FOR A FREE CONSULTATION
KINTEK LAB SOLUTION's products and services have been recognized by customers around the world. Our staff will be happy to assist with any inquiry you might have. Contact us for a free consultation and talk to a product specialist to find the most suitable solution for your application needs!