Heating elements, while essential in many appliances and industrial applications, come with certain safety considerations. The safety of heating elements largely depends on their design, material, and usage conditions. Poorly designed elements, such as those with openings that allow atmosphere infiltration, can lead to soot deposition and arcing, posing significant risks. Additionally, metal heating elements can suffer from issues like low electrical insulation, surface scaling, and leakage currents, which further compromise safety. Ensuring the reliability and safety of heating elements requires careful design, proper insulation, and regular maintenance to mitigate potential hazards.
Key Points Explained:
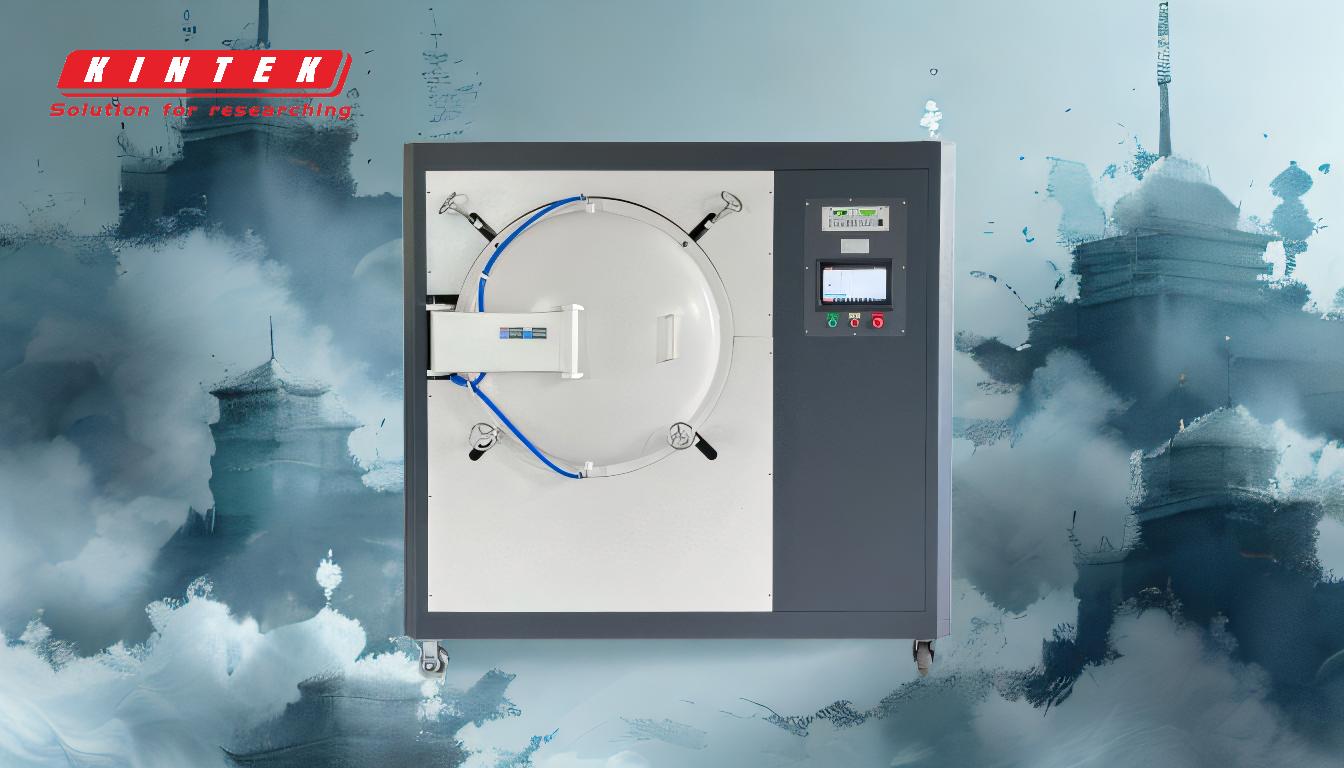
-
Design Flaws Leading to Safety Risks:
- Heating elements that pass through small openings in refractory materials into an insulator integrated into the steel casing are prone to reliability issues.
- The atmosphere can infiltrate these openings, leading to soot deposition on the insulator.
- This soot deposition can cause arcing between the lead-in and the steel casing, which is a significant safety hazard.
-
Material-Related Safety Issues:
- Metal heating elements, commonly used in electric appliances, are susceptible to several problems that can compromise safety.
- These issues include low electrical insulation, which can lead to electrical faults.
- Surface scaling and bursting are other concerns that can result in the element failing catastrophically.
- Leakage current is another risk, which can cause electric shocks or fires.
-
Mitigation Strategies:
- Proper Design: Ensuring that heating elements are designed without small openings that can allow atmosphere infiltration is crucial. This prevents soot deposition and arcing.
- Material Selection: Using materials with high electrical insulation properties can reduce the risk of electrical faults and leakage currents.
- Regular Maintenance: Periodic inspection and maintenance of heating elements can help identify and address issues like surface scaling and insulation degradation before they lead to failures.
- Safety Standards Compliance: Adhering to industry safety standards and regulations can help ensure that heating elements are safe for use in various applications.
-
Conclusion:
- While heating elements are generally safe when properly designed and maintained, there are inherent risks associated with poor design and material choices.
- By addressing these risks through careful design, material selection, and maintenance, the safety of heating elements can be significantly enhanced.
- Users should be aware of these potential hazards and take appropriate measures to mitigate them, ensuring the safe operation of heating elements in their applications.
Summary Table:
Safety Consideration | Description |
---|---|
Design Flaws | Small openings allow atmosphere infiltration, leading to soot deposition and arcing. |
Material Issues | Low electrical insulation, surface scaling, bursting, and leakage currents. |
Mitigation Strategies | Proper design, high-insulation materials, regular maintenance, and compliance. |
Ensure your heating elements are safe and reliable—contact our experts today for guidance!