Sintered parts can be conductive, but their conductivity depends on the material used in the sintering process. For example, sintered metals like copper, aluminum, or steel retain their conductive properties, while sintered ceramics are typically non-conductive. The porosity and microstructure of sintered parts can influence their electrical conductivity, as pores may reduce the effective cross-sectional area for electron flow. However, the primary constituent material's inherent conductivity plays the dominant role. Sintered metal parts are widely used in applications requiring both structural integrity and electrical conductivity, such as in electrical contacts or heat sinks.
Key Points Explained:
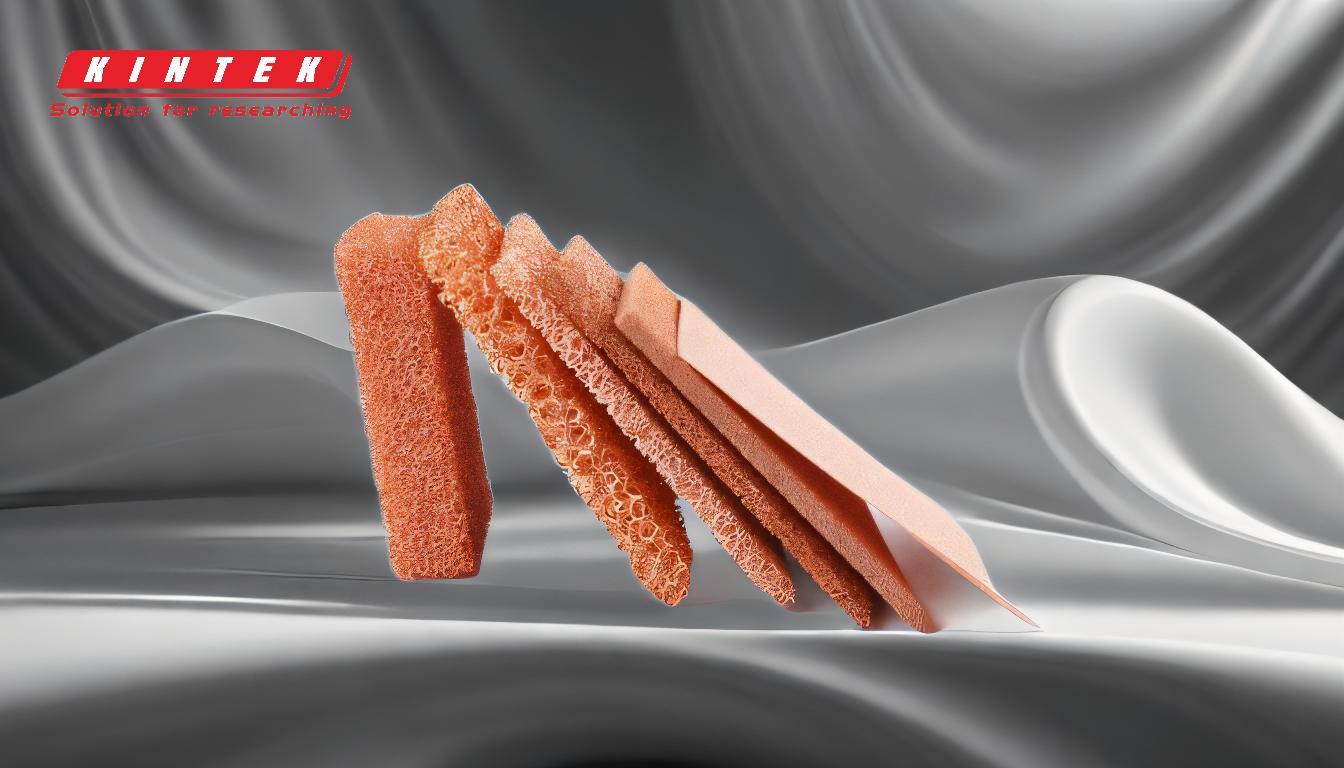
-
Material Dependency:
- Sintered parts' conductivity is primarily determined by the base material used. Metals like copper, aluminum, and steel, which are inherently conductive, will produce conductive sintered parts.
- Ceramics, which are generally non-conductive, will result in non-conductive sintered parts regardless of the sintering process.
-
Porosity and Microstructure:
- Sintered parts often have a certain level of micro-porosity due to the nature of the sintering process. This porosity can reduce the effective cross-sectional area available for electron flow, potentially lowering conductivity.
- The microstructure, including grain size and distribution, also plays a role. Larger grain sizes and uneven distributions can affect electrical pathways.
-
Applications of Conductive Sintered Parts:
- Conductive sintered metal parts are used in applications requiring both structural integrity and electrical conductivity. Examples include electrical contacts, heat sinks, and components in electronic devices.
- The ability to create complex shapes through sintering makes it a preferred method for manufacturing such components.
-
Comparison with Other Manufacturing Methods:
- Sintered metal parts can achieve similar conductivity levels as machined or forged parts, provided the sintering process is well-controlled and the material properties are optimized.
- However, sintered parts may have slightly lower conductivity due to porosity and microstructure differences compared to fully dense machined or forged parts.
-
Measurement of Properties:
- Properties like relative density, porosity, and pore size distribution are measured to assess the quality of sintered parts. These properties indirectly influence conductivity by affecting the material's density and microstructure.
- For conductive applications, ensuring minimal porosity and a uniform microstructure is crucial to maintain high conductivity.
-
Advantages of Sintering for Conductive Parts:
- Sintering allows for the production of complex shapes with high precision, which is beneficial for creating intricate conductive components.
- The process is cost-effective and environmentally friendly, as it minimizes material waste and can use recycled materials.
In summary, sintered parts can be conductive if made from inherently conductive materials like metals. However, their conductivity may be influenced by factors such as porosity and microstructure, which are inherent to the sintering process. Understanding these factors is essential for designing sintered parts for applications requiring electrical conductivity.
Summary Table:
Factor | Impact on Conductivity |
---|---|
Material Dependency | Metals (e.g., copper, aluminum, steel) are conductive; ceramics are non-conductive. |
Porosity | Pores reduce effective cross-sectional area, potentially lowering conductivity. |
Microstructure | Grain size and distribution affect electrical pathways. |
Applications | Used in electrical contacts, heat sinks, and electronic components. |
Advantages | Complex shapes, cost-effective, eco-friendly, and precise manufacturing. |
Need conductive sintered parts for your project? Contact our experts today to get started!