Molybdenum begins to evaporate at temperatures of 650°C or higher, forming molybdenum trioxide (MoO₃), which appears as a white substance. This evaporation occurs due to the oxidation of molybdenum at elevated temperatures. While molybdenum is highly resistant to corrosion and maintains stability in non-oxidizing environments up to 1100°C, its interaction with oxygen at high temperatures leads to the formation of volatile oxides. This property is critical for applications involving high-temperature environments, as it dictates the operational limits of molybdenum in oxidizing conditions.
Key Points Explained:
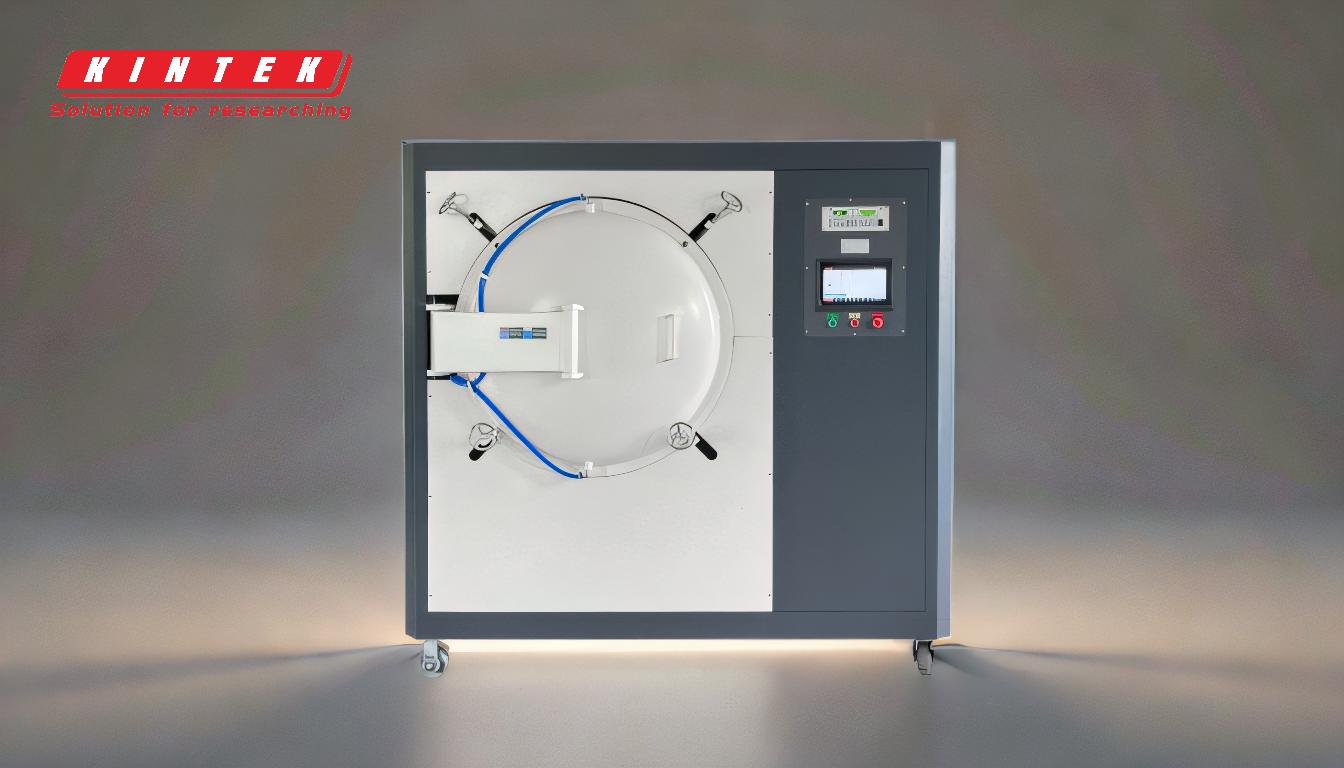
-
Evaporation Temperature of Molybdenum:
- Molybdenum begins to evaporate at 650°C or higher when exposed to oxygen, forming molybdenum trioxide (MoO₃).
- This process is a result of oxidation, as molybdenum reacts with oxygen at elevated temperatures.
-
Oxidation Behavior:
- At room temperature, molybdenum is stable and does not react with dried oxygen.
- However, at 500°C or higher, molybdenum rapidly oxidizes, leading to the formation of oxides.
- The evaporation at 650°C is a continuation of this oxidation process, where the oxide (MoO₃) becomes volatile.
-
High-Temperature Stability in Non-Oxidizing Environments:
- Molybdenum exhibits excellent resistance to corrosion and remains stable in non-oxidizing environments such as hydrogen, ammonia, and nitrogen up to 1100°C.
- This makes it suitable for applications in high-temperature, non-oxidizing atmospheres, such as in furnaces or reactors.
-
Physical and Thermal Properties:
- Molybdenum has a melting point of 2610°C and a boiling point of 5560°C, indicating its exceptional thermal stability.
- Its low thermal expansion and high thermal conductivity contribute to its performance in high-temperature applications.
- The low vapor pressure of molybdenum ensures minimal evaporation in inert or reducing environments.
-
Applications and Implications:
- The evaporation temperature of molybdenum is a critical factor in applications involving high-temperature oxidizing environments, such as in aerospace, electronics, and glass manufacturing.
- In non-oxidizing environments, molybdenum's stability up to 1100°C allows it to be used in high-temperature furnaces, heat shields, and other thermal management systems.
-
Comparison with Tungsten:
- While molybdenum evaporates at 650°C in the presence of oxygen, tungsten, another refractory metal, has a much higher boiling point of 5660°C.
- This makes tungsten more suitable for extremely high-temperature applications, but molybdenum's lower density and cost make it preferable for many industrial uses.
-
Alloying for Improved Properties:
- Pure molybdenum's properties, including its evaporation temperature, can be enhanced through alloying.
- Alloys such as TZM (Titanium-Zirconium-Molybdenum) offer improved high-temperature strength and creep resistance, extending the operational limits of molybdenum in demanding environments.
In summary, molybdenum's evaporation at 650°C in oxidizing conditions is a key consideration for its use in high-temperature applications. Its stability in non-oxidizing environments and excellent thermal properties make it a valuable material, but its susceptibility to oxidation at elevated temperatures must be carefully managed. Alloying and environmental control are essential strategies to maximize its performance in specific applications.
Summary Table:
Property | Details |
---|---|
Evaporation Temperature | 650°C or higher (in oxidizing conditions) |
Oxidation Behavior | Stable at room temperature; oxidizes rapidly at 500°C or higher |
Stability in Non-Oxidizing | Up to 1100°C in hydrogen, ammonia, or nitrogen |
Melting Point | 2610°C |
Boiling Point | 5560°C |
Thermal Properties | Low thermal expansion, high thermal conductivity, low vapor pressure |
Key Applications | Aerospace, electronics, glass manufacturing, high-temperature furnaces |
Alloying for Enhancement | TZM alloys improve high-temperature strength and creep resistance |
Discover how molybdenum can enhance your high-temperature applications—contact us today for expert guidance!