Heating elements can indeed overheat, and this overheating can lead to various issues that compromise their performance and safety. Overheating is often caused by factors such as the formation of hot spots, oxidation, embrittlement, contamination, and poor design. These issues can result in reduced efficiency, failure of the heating element, and even safety hazards like electrical arcing or leakage currents. Understanding the causes and effects of overheating is crucial for maintaining the longevity and reliability of heating elements in various applications.
Key Points Explained:
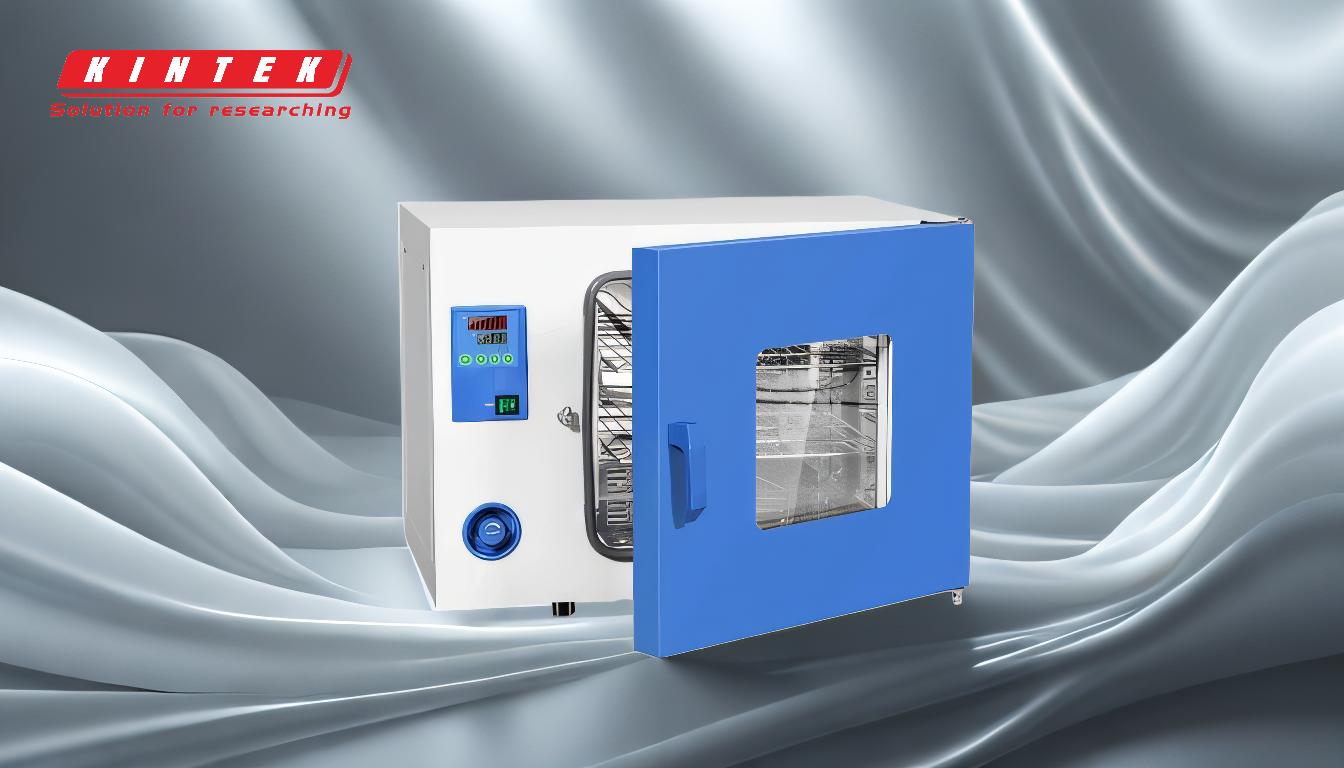
-
Formation of Hot Spots:
- Explanation: Hot spots occur when certain areas of the heating element become significantly hotter than the rest of the element. This can be due to high local oxidation or shielding by supports, which disrupts the uniform distribution of heat.
- Impact: Hot spots can lead to localized overheating, which accelerates the degradation of the heating element. This can cause the element to fail prematurely and may also pose a safety risk.
-
Oxidation and Intermittency of Operation:
- Explanation: Frequent heating and cooling cycles can cause the oxide layer on the heating element to crack and flake off. This exposes fresh metal to further oxidation, leading to a cycle of degradation.
- Impact: The repeated exposure of fresh metal to oxidation can significantly reduce the lifespan of the heating element. It also increases the risk of overheating as the metal becomes more susceptible to high temperatures.
-
Embrittlement Due to Grain Growth:
- Explanation: At high temperatures, heating alloys containing iron can form large, brittle grains. This process, known as grain growth, makes the material more prone to cracking and breaking.
- Impact: Embrittlement can lead to mechanical failure of the heating element, especially under thermal stress. This not only reduces the element's effectiveness but also increases the risk of overheating as the material becomes less able to withstand high temperatures.
-
Contamination and Corrosion:
- Explanation: The presence of gases or fumes in the furnace environment can contaminate the heating elements, leading to dry corrosion. This contamination can alter the material properties of the element.
- Impact: Contamination and corrosion can weaken the heating element, making it more susceptible to overheating. Additionally, the altered material properties can lead to unpredictable behavior under high temperatures.
-
Design Flaws:
- Explanation: Poor design, such as heating elements that pass through small openings in the refractory into an insulator integrated into the steel casing, can be unreliable. The endo atmosphere can bleed through these openings, depositing soot onto the insulator and causing arcing.
- Impact: Design flaws can lead to electrical arcing between the lead-in and steel casing, which is a significant safety hazard. This arcing can cause localized overheating and potentially lead to catastrophic failure of the heating element.
-
Electrical Insulation and Security Issues:
- Explanation: Metal heating elements often face issues such as low electrical insulation and low security levels. These issues can lead to surface scaling, bursting, and leakage currents.
- Impact: Low electrical insulation and security levels can result in electrical faults, which can cause the heating element to overheat. Leakage currents and surface scaling further exacerbate the problem, leading to potential safety risks.
In conclusion, overheating of heating elements is a multifaceted issue that can arise from various causes, including hot spots, oxidation, embrittlement, contamination, design flaws, and electrical insulation problems. Addressing these issues requires careful consideration of material selection, design, and operational conditions to ensure the longevity and safety of heating elements.
Summary Table:
Cause of Overheating | Explanation | Impact |
---|---|---|
Formation of Hot Spots | Localized areas become hotter due to oxidation or shielding by supports. | Accelerated degradation, premature failure, and safety risks. |
Oxidation | Frequent heating/cooling cycles crack the oxide layer, exposing fresh metal. | Reduced lifespan and increased susceptibility to overheating. |
Embrittlement | High temperatures cause grain growth, making the material brittle. | Mechanical failure under thermal stress and increased overheating risk. |
Contamination & Corrosion | Gases or fumes in the furnace environment cause dry corrosion. | Weakened material and unpredictable behavior under high temperatures. |
Design Flaws | Poor design leads to arcing between lead-in and steel casing. | Electrical arcing, localized overheating, and potential catastrophic failure. |
Electrical Insulation Issues | Low insulation and security levels cause leakage currents and surface scaling. | Electrical faults, overheating, and safety hazards. |
Need help preventing overheating in your heating elements? Contact our experts today for tailored solutions!