Brazing stainless steel is indeed possible and can be effectively achieved using various methods such as flame, induction, or furnace heating. The process involves several critical steps, including thorough cleaning before brazing, selecting the appropriate brazing method, and post-brazing treatments to ensure the integrity and quality of the joint. While most stainless steel types can be brazed, certain grades stabilized with titanium or niobium may present challenges. The choice of brazing method—whether in air with flux, under a reducing atmosphere, or in a vacuum—depends on the specific requirements of the application and the desired quality of the brazed joint.
Key Points Explained:
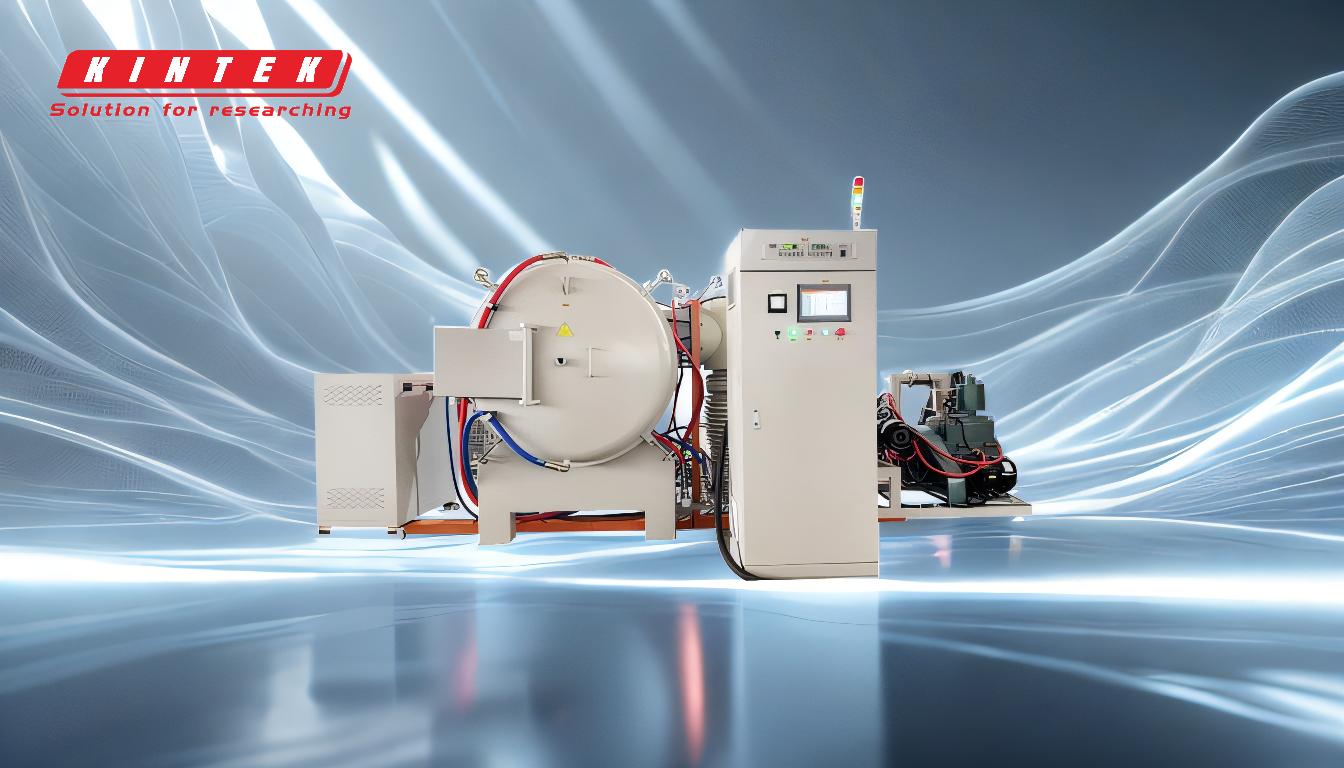
-
Brazing Methods for Stainless Steel:
- Flame Brazing: This method uses a gas flame to heat the stainless steel and the brazing filler metal until the filler melts and flows into the joint. It is suitable for small-scale or manual operations.
- Induction Brazing: Induction heating provides localized and rapid heating, making it ideal for precise and repeatable brazing of specific areas. It is commonly used in high-volume production.
- Furnace Brazing: This method involves heating the entire assembly in a controlled environment, such as a vacuum or reducing atmosphere furnace. It is suitable for complex or large components and ensures uniform heating.
-
Preparation Before Brazing:
- Cleaning: Stainless steel must be thoroughly cleaned to remove grease, oil, and other contaminants. This step is crucial to ensure proper wetting and bonding of the filler metal.
- Immediate Brazing: After cleaning, brazing should be performed promptly to prevent recontamination of the surfaces.
-
Filler Metal and Flux:
- Filler metals for brazing stainless steel typically include silver-based alloys, copper-based alloys, or nickel-based alloys, depending on the application and joint requirements.
- Flux is often used to prevent oxidation and improve the flow of the filler metal. However, residual flux must be cleaned after brazing to avoid corrosion.
-
Vacuum Brazing:
- Vacuum brazing is a preferred method for high-quality joints, especially in applications requiring high strength and corrosion resistance. It involves three main steps:
- Preparation: Cleaning and assembling the components.
- Filling: Placing the filler metal in the joint.
- Heating: Heating the assembly in a high-vacuum furnace to achieve a strong bond.
- Vacuum brazing is a preferred method for high-quality joints, especially in applications requiring high strength and corrosion resistance. It involves three main steps:
-
Post-Brazing Processes:
- Cleaning Residual Flux: After brazing, any remaining flux or flux inhibitors must be removed to prevent corrosion or contamination.
- Heat Treatment: In some cases, post-brazing heat treatment may be required to relieve stresses and improve the mechanical properties of the joint.
-
Compatibility of Stainless Steel Grades:
- Most stainless steel grades can be brazed, but those stabilized with titanium or niobium (e.g., 321 or 347 stainless steel) may not be suitable due to their tendency to form brittle intermetallic compounds during brazing.
-
Brazing Under Reducing Atmosphere:
- Brazing in a reducing atmosphere (e.g., hydrogen or nitrogen) can eliminate the need for flux by preventing oxidation. This method is particularly useful for high-purity applications.
By understanding these key points, a purchaser can make informed decisions about the brazing process, equipment, and materials required for their specific stainless steel brazing application.
Summary Table:
Key Aspect | Details |
---|---|
Brazing Methods | Flame, Induction, Furnace (vacuum or reducing atmosphere) |
Preparation | Thorough cleaning, immediate brazing to prevent contamination |
Filler Metals | Silver-based, copper-based, or nickel-based alloys |
Flux Usage | Prevents oxidation; must be cleaned post-brazing |
Vacuum Brazing Steps | Preparation, filling with filler metal, heating in a vacuum furnace |
Post-Brazing Processes | Cleaning residual flux, heat treatment (if required) |
Compatibility | Most grades can be brazed; avoid titanium- or niobium-stabilized grades |
Reducing Atmosphere Brazing | Eliminates flux by preventing oxidation; ideal for high-purity applications |
Need expert advice on brazing stainless steel? Contact us today for tailored solutions!