Brazing is a process that involves joining two or more metal pieces using a filler metal with a melting point above 450°C but below the melting point of the base metals. A common question that arises is whether a brazed joint can be reheated after the initial brazing process. The answer depends on several factors, including the materials used, the quality of the initial joint, and the purpose of reheating. Reheating a brazed joint can be done, but it requires careful consideration of the potential effects on the joint's integrity, the base metals, and the filler material. In some cases, reheating can weaken the joint or cause oxidation, while in other cases, it may be necessary for repair or adjustment.
Key Points Explained:
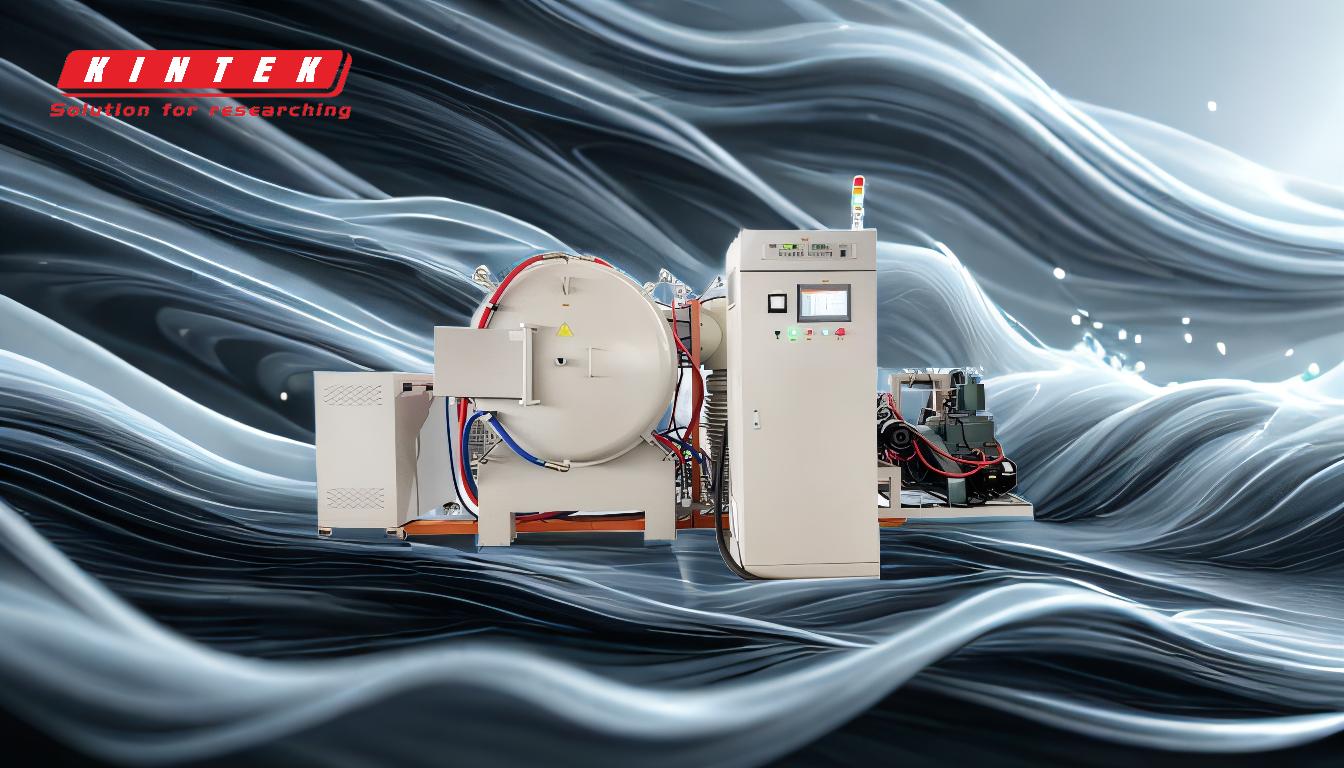
-
Understanding the Brazing Process
- Brazing involves heating the base metals and the filler metal to a temperature where the filler metal melts and flows into the joint by capillary action.
- The filler metal solidifies upon cooling, creating a strong, durable bond between the base metals.
- The integrity of the joint depends on proper heating, cleanliness, and the compatibility of the materials.
-
Reasons for Reheating a Brazed Joint
- Repair or Adjustment: If a brazed joint is imperfect or needs realignment, reheating may be necessary to melt the filler metal and make corrections.
- Stress Relief: Reheating can help relieve residual stresses in the joint or base metals caused by the initial brazing process.
- Joining Additional Components: In some cases, reheating is required to add another component to an existing brazed assembly.
-
Challenges of Reheating a Brazed Joint
- Oxidation: Repeated heating can cause oxidation of the base metals and filler material, leading to a weaker joint.
- Thermal Damage: Excessive heat or prolonged exposure can damage the base metals or alter their properties.
- Filler Metal Redistribution: Reheating may cause the filler metal to flow unevenly, potentially weakening the joint.
-
Best Practices for Reheating a Brazed Joint
- Control Temperature: Use precise temperature control to avoid overheating and ensure the filler metal melts uniformly.
- Protect Against Oxidation: Use a controlled atmosphere, such as an inert gas or flux, to prevent oxidation during reheating.
- Inspect the Joint: Before reheating, inspect the joint for cracks, voids, or other defects that could worsen with additional heating.
- Follow Material Guidelines: Adhere to the recommended heating and cooling rates for the specific base metals and filler material.
-
When Not to Reheat a Brazed Joint
- If the joint is already strong and functional, reheating may introduce unnecessary risks.
- Avoid reheating if the base metals or filler material are sensitive to thermal cycling or prone to degradation.
- In critical applications, such as aerospace or medical devices, reheating should only be done after thorough evaluation and testing.
-
Alternatives to Reheating
- If reheating is not feasible, consider alternative methods such as mechanical fastening, welding, or using adhesives.
- For minor repairs, localized heating techniques like induction heating can minimize the risk of damaging the entire joint.
By carefully considering these factors, you can determine whether reheating a brazed joint is appropriate for your specific application. Proper techniques and precautions can help maintain the joint's strength and functionality while achieving the desired results.
Summary Table:
Aspect | Details |
---|---|
Reasons for Reheating | Repair, stress relief, or adding components. |
Challenges | Oxidation, thermal damage, filler metal redistribution. |
Best Practices | Control temperature, protect against oxidation, inspect joint, follow guidelines. |
When Not to Reheat | Strong joints, sensitive materials, critical applications. |
Alternatives | Mechanical fastening, welding, adhesives, localized heating. |
Need expert advice on reheating brazed joints? Contact us today for tailored solutions!