Electric kilns, including electric rotary kilns, do consume electricity, but the amount varies significantly depending on factors like size, design, and operational efficiency. Smaller kilns typically use between 1.5 and 1.8 kilowatts, while larger or industrial-grade kilns, such as electric rotary kilns, can consume up to 300 kW during peak operation. However, once the kiln reaches stable operation, power consumption decreases. Understanding these factors helps in estimating energy use and optimizing efficiency.
Key Points Explained:
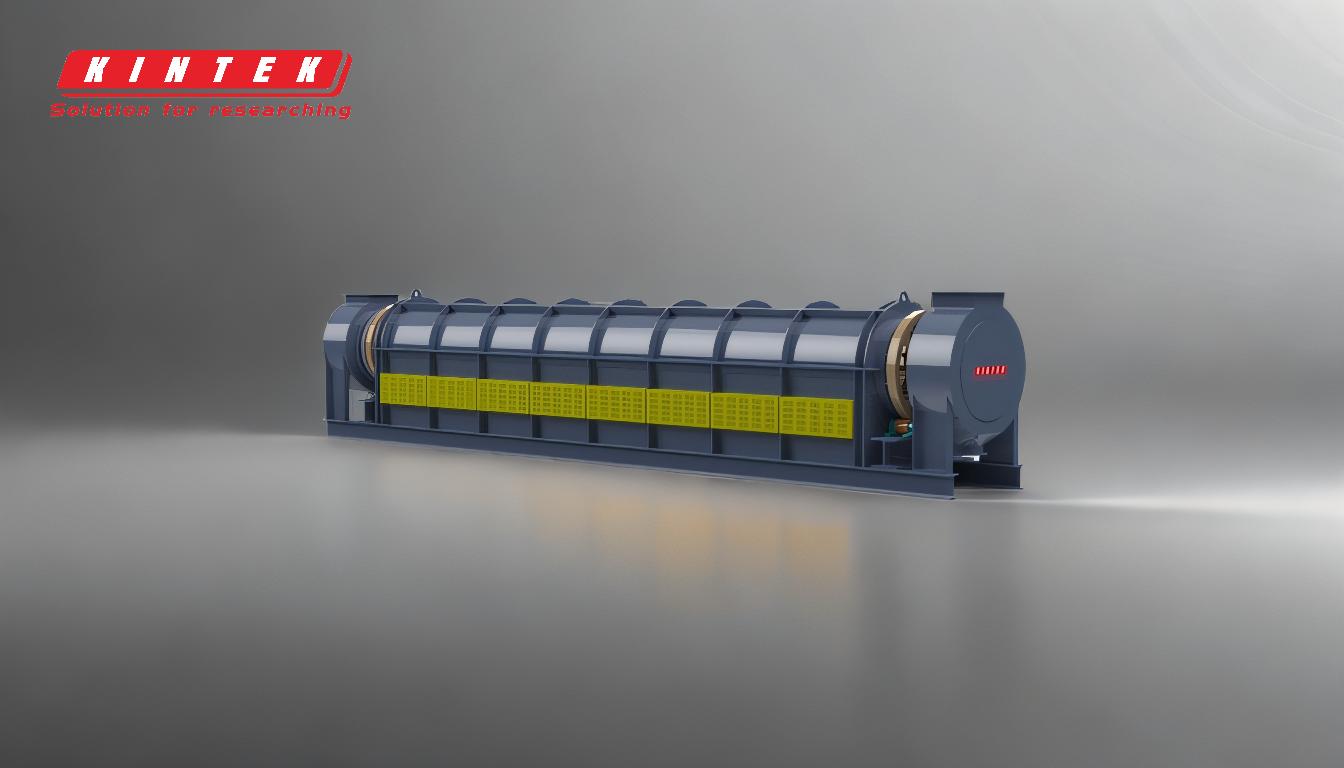
-
Power Consumption Depends on Kiln Size and Design:
- Smaller kilns, often used for pottery or small-scale projects, typically operate on a standard 120-volt household outlet. These kilns consume between 1.5 and 1.8 kilowatts, making them relatively energy-efficient for their size.
- Larger kilns, such as medium-sized models, can draw around 5 kW to 8 kW, which is significantly higher but still manageable for many users.
- Industrial-grade kilns, like electric rotary kilns, have much higher power requirements, with rated heating power reaching up to 300 kW. These are designed for heavy-duty applications and require substantial energy input.
-
Operational Efficiency and Stable Power Consumption:
- During the initial heating phase, electric kilns consume more power to reach the desired temperature. This is especially true for larger kilns, which may require significant energy to heat up.
- Once the kiln reaches stable operation, power consumption decreases. This is because maintaining a consistent temperature requires less energy than the initial heating process.
- For example, an electric rotary kiln may use up to 300 kW during startup but will stabilize at a lower power level once operational.
-
Factors Influencing Electricity Usage:
- Insulation and Design: Well-insulated kilns retain heat more effectively, reducing the need for continuous energy input. Modern designs often prioritize energy efficiency.
- Usage Patterns: Frequent heating and cooling cycles increase energy consumption. Optimizing usage schedules can help minimize electricity use.
- Temperature Requirements: Higher firing temperatures require more energy. Understanding the specific needs of your project can help in selecting an appropriately sized kiln.
-
Cost Implications:
- The cost of operating an electric kiln depends on local electricity rates and the kiln's power consumption. For example, a small kiln using 1.8 kW for 10 hours would consume 18 kWh, costing approximately $2.16 at $0.12 per kWh.
- Larger kilns, such as electric rotary kilns, can be more expensive to operate due to their higher power requirements. However, their efficiency during stable operation can offset some of these costs.
-
Energy-Saving Tips:
- Batch Processing: Firing multiple items at once maximizes energy use and reduces the need for frequent heating cycles.
- Proper Maintenance: Regularly inspecting and maintaining the kiln ensures it operates efficiently, reducing unnecessary energy consumption.
- Temperature Control: Using programmable controllers can help maintain optimal temperatures, preventing energy waste.
By understanding these key points, you can make informed decisions about the type of kiln to purchase and how to optimize its energy use. Whether you're using a small pottery kiln or an industrial electric rotary kiln, managing power consumption effectively can lead to significant cost savings and environmental benefits.
Summary Table:
Kiln Type | Power Consumption | Key Features |
---|---|---|
Small Kilns | 1.5–1.8 kW | Energy-efficient, suitable for pottery and small-scale projects. |
Medium Kilns | 5–8 kW | Higher power draw, ideal for larger projects. |
Industrial Kilns | Up to 300 kW | Heavy-duty applications, high power during startup, efficient at stable operation. |
Factors Affecting Use | Insulation, usage patterns, temperature requirements. | Optimize usage for energy savings. |
Ready to optimize your kiln's energy use? Contact our experts today for personalized advice!