Annealing is a heat treatment process used to alter the physical and sometimes chemical properties of a material to increase its ductility and reduce its hardness, making it more workable. The process involves heating the material to a specific temperature, holding it there for a certain period, and then cooling it slowly. Quenching, on the other hand, involves rapid cooling, typically used to harden materials. Whether to quench after annealing depends on the material and the desired properties. For most materials, especially metals, quenching is not typically done after annealing because it would counteract the annealing's purpose of increasing ductility and reducing hardness. However, in specific processes like quench annealing, quenching is an integral part of the process to achieve certain material properties.
Key Points Explained:
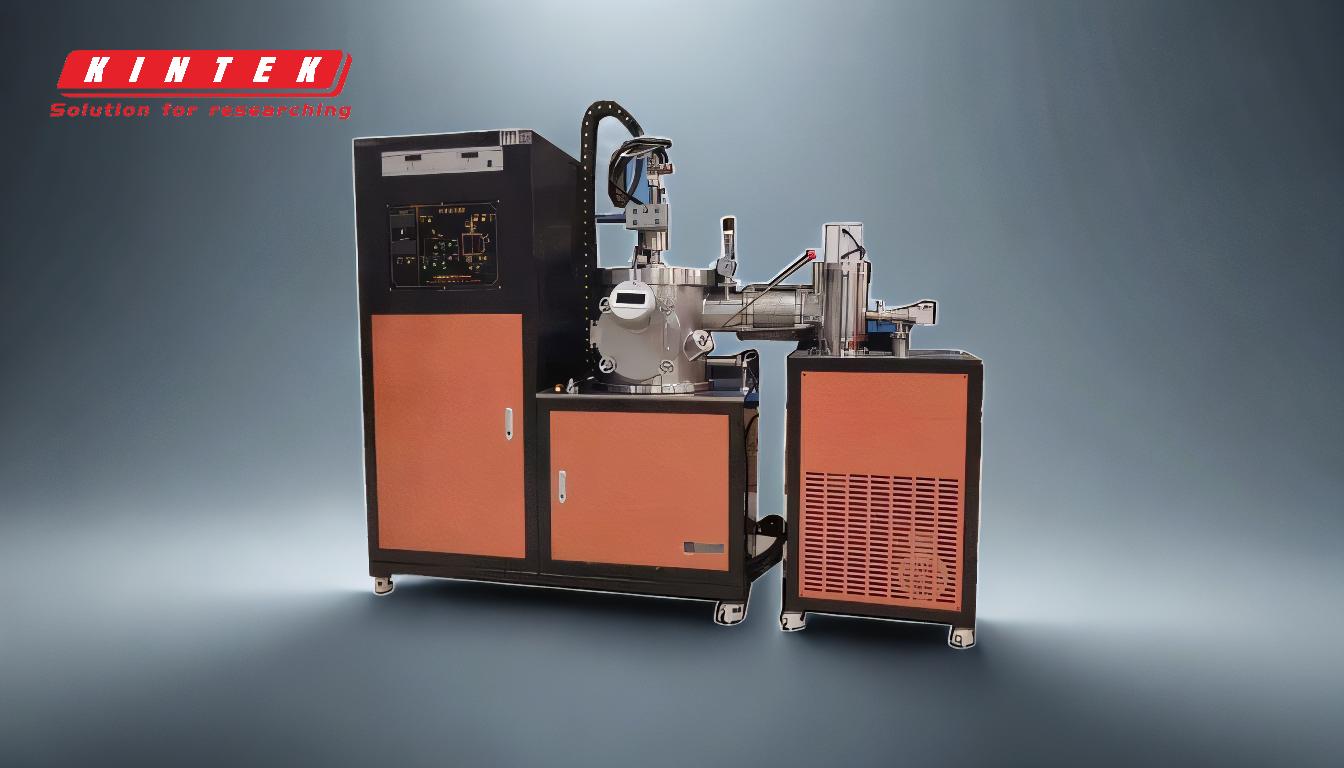
-
Purpose of Annealing:
- Annealing is primarily used to relieve internal stresses, increase ductility, and reduce hardness. This makes the material more workable and less prone to cracking or deformation during subsequent processing or use.
-
Annealing Process Stages:
- Recovery: The material is heated to a temperature where internal stresses begin to relieve without altering the microstructure significantly.
- Recrystallization: The material is heated to a higher temperature where new grains form, replacing the deformed grains, leading to a softer and more ductile structure.
- Grain Growth: If the material is held at the recrystallization temperature for too long, grain growth can occur, which may not be desirable as it can reduce the material's strength.
-
Cooling After Annealing:
- After annealing, the material is typically allowed to cool slowly in the furnace or in air. This slow cooling is crucial to maintain the ductile and soft structure achieved during annealing.
-
Quenching After Annealing:
- General Case: Quenching is not typically done after standard annealing because rapid cooling would reintroduce hardness and reduce ductility, counteracting the benefits of annealing.
- Special Cases: In processes like quench annealing, quenching is used to achieve specific material properties. For example, in quench annealing of steel, the material is heated and then rapidly cooled to achieve a specific microstructure that balances hardness and toughness.
-
Quench and Temper Process:
- This process is distinct from annealing and involves heating the material above its transformation range, rapidly cooling it (quenching), and then reheating it to a lower temperature to temper. This process is used to increase both strength and hardness, which is different from the goals of annealing.
-
Material-Specific Considerations:
- The decision to quench after annealing depends on the material and the desired final properties. For example, in ceramics, rapid cooling after annealing can lead to cracking, so slow cooling is preferred. In metals, the choice depends on whether the goal is to increase ductility (no quenching) or to achieve a specific balance of hardness and toughness (quench annealing).
-
Practical Implications:
- For equipment and consumable purchasers, understanding whether quenching is required after annealing is crucial for selecting the right material and heat treatment process. This ensures that the material will perform as needed in its intended application.
In summary, quenching after annealing is not a standard practice and is generally avoided unless specific material properties are desired, as in the case of quench annealing. The typical annealing process aims to increase ductility and reduce hardness, which is best achieved through slow cooling.
Summary Table:
Aspect | Description |
---|---|
Purpose of Annealing | Relieves internal stresses, increases ductility, and reduces hardness. |
Cooling After Annealing | Slow cooling maintains ductility and soft structure. |
Quenching After Annealing | Rarely done; rapid cooling reintroduces hardness, counteracting annealing goals. |
Special Cases | Quench annealing uses quenching to achieve specific material properties. |
Material Considerations | Depends on material type and desired properties (e.g., metals vs. ceramics). |
Need help selecting the right heat treatment process? Contact our experts today for tailored solutions!