When deciding whether you need a two-stage furnace, it’s essential to evaluate your heating needs, budget, and long-term operational costs. A two-stage furnace offers improved energy efficiency and comfort by adjusting its heating output based on the temperature demands. On milder days, it operates in the first stage, consuming less energy, while on colder days, it switches to the second stage for higher heat output. This results in fewer start-stop cycles, reducing wear and tear on components and improving longevity. However, the initial cost is higher than single-stage furnaces, so it’s crucial to weigh these benefits against your specific requirements and budget.
Key Points Explained:
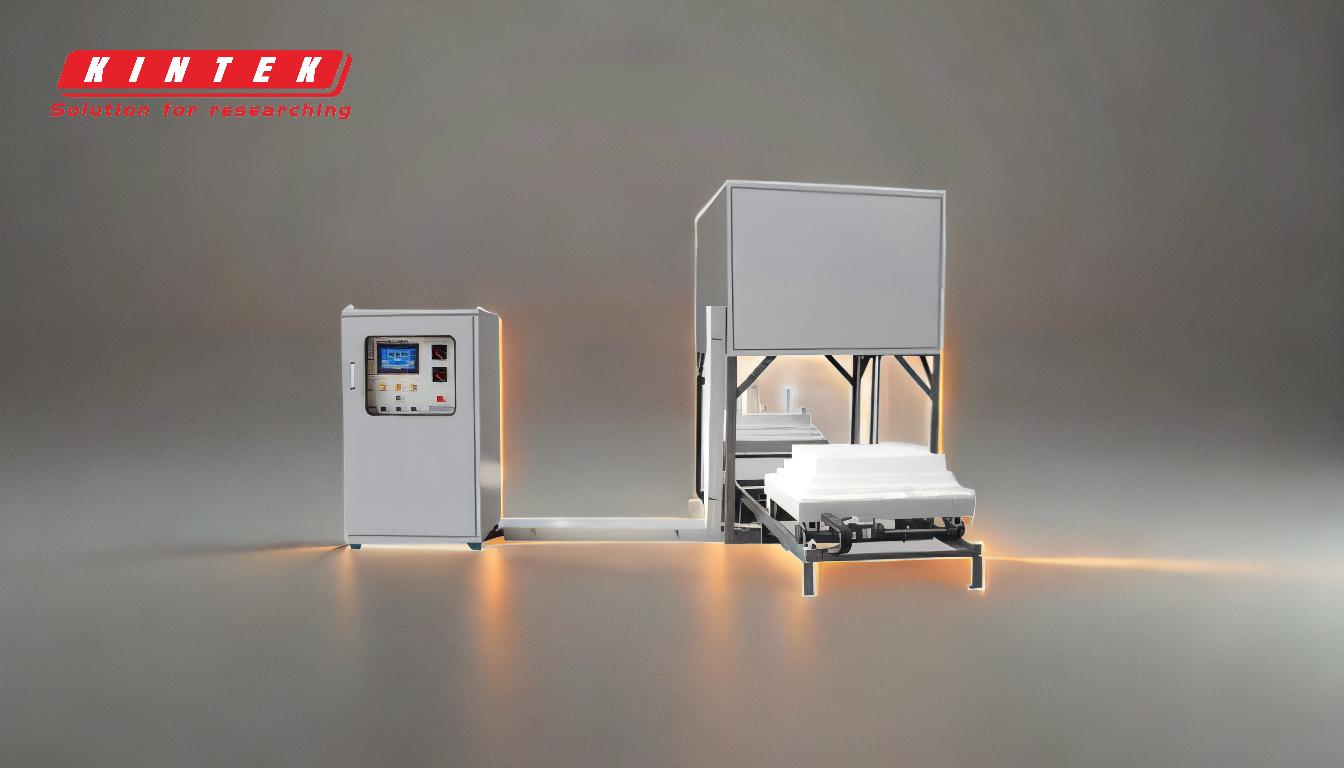
-
Understanding Two-Stage Furnaces:
- A two-stage furnace operates at two levels of heating output: a low stage for milder weather and a high stage for colder days.
- This dual-stage operation ensures consistent indoor temperatures and reduces temperature fluctuations, enhancing comfort.
-
Energy Efficiency:
- Two-stage furnaces are more energy-efficient than single-stage models because they often run at a lower capacity, consuming less fuel.
- On milder days, the furnace operates in the first stage, using less energy, which can lead to lower utility bills over time.
-
Comfort and Temperature Control:
- The ability to adjust heating output based on demand ensures a more consistent and comfortable indoor environment.
- Longer run times at lower stages reduce the frequency of on-off cycles, minimizing temperature swings and improving overall comfort.
-
Durability and Maintenance:
- Fewer start-stop cycles mean less wear and tear on the furnace components, potentially extending the lifespan of the system.
- Reduced mechanical stress can also lead to lower maintenance costs over time.
-
Cost Considerations:
- Two-stage furnaces typically have a higher upfront cost compared to single-stage models.
- However, the long-term savings from improved energy efficiency and reduced maintenance can offset the initial investment.
-
Climate and Usage:
- In regions with mild winters, a two-stage furnace may not be necessary, as the second stage might rarely be used.
- For colder climates, the second stage ensures adequate heating during extreme cold, making it a more suitable choice.
-
Comparison with Single-Stage Furnaces:
- Single-stage furnaces operate at full capacity regardless of the temperature demand, leading to less efficient energy use and more frequent cycling.
- While single-stage furnaces are cheaper initially, they may cost more to operate and maintain in the long run.
-
Decision-Making Factors:
- Budget: If the upfront cost is a significant concern, a single-stage furnace might be more appealing.
- Energy Savings: For those prioritizing long-term energy savings and efficiency, a two-stage furnace is a better investment.
- Comfort Needs: If consistent indoor temperatures and reduced noise from fewer cycles are important, a two-stage furnace is ideal.
- Climate: Consider the severity of winters in your area; colder climates benefit more from the dual-stage operation.
In conclusion, whether you need a two-stage furnace depends on your specific heating needs, budget, and climate. While it offers significant advantages in terms of energy efficiency, comfort, and durability, the higher initial cost may not be justified in milder climates or for those with tighter budgets. Carefully evaluate these factors to make an informed decision that aligns with your long-term goals.
Summary Table:
Aspect | Two-Stage Furnace | Single-Stage Furnace |
---|---|---|
Heating Output | Two levels: low for mild weather, high for cold days | Single level: full capacity regardless of demand |
Energy Efficiency | More efficient, consumes less fuel on milder days | Less efficient, operates at full capacity even when not needed |
Comfort | Consistent indoor temperatures, fewer temperature swings | Frequent temperature fluctuations |
Durability | Fewer start-stop cycles, less wear and tear, longer lifespan | More frequent cycling, higher wear and tear |
Initial Cost | Higher upfront cost | Lower upfront cost |
Long-Term Savings | Lower utility bills and maintenance costs over time | Higher operational and maintenance costs |
Best For | Colder climates, those prioritizing comfort and energy savings | Milder climates, tighter budgets |
Still unsure if a two-stage furnace is right for you? Contact our experts today for personalized advice!