Casting is a manufacturing process where molten material is poured into a mold to solidify into a desired shape. This process can indeed change the material properties of the final product due to factors like cooling rates, microstructure formation, and potential defects. The extent of these changes depends on the material being cast, the casting method, and post-casting treatments. Understanding these changes is crucial for selecting the right casting process and ensuring the final product meets performance requirements.
Key Points Explained:
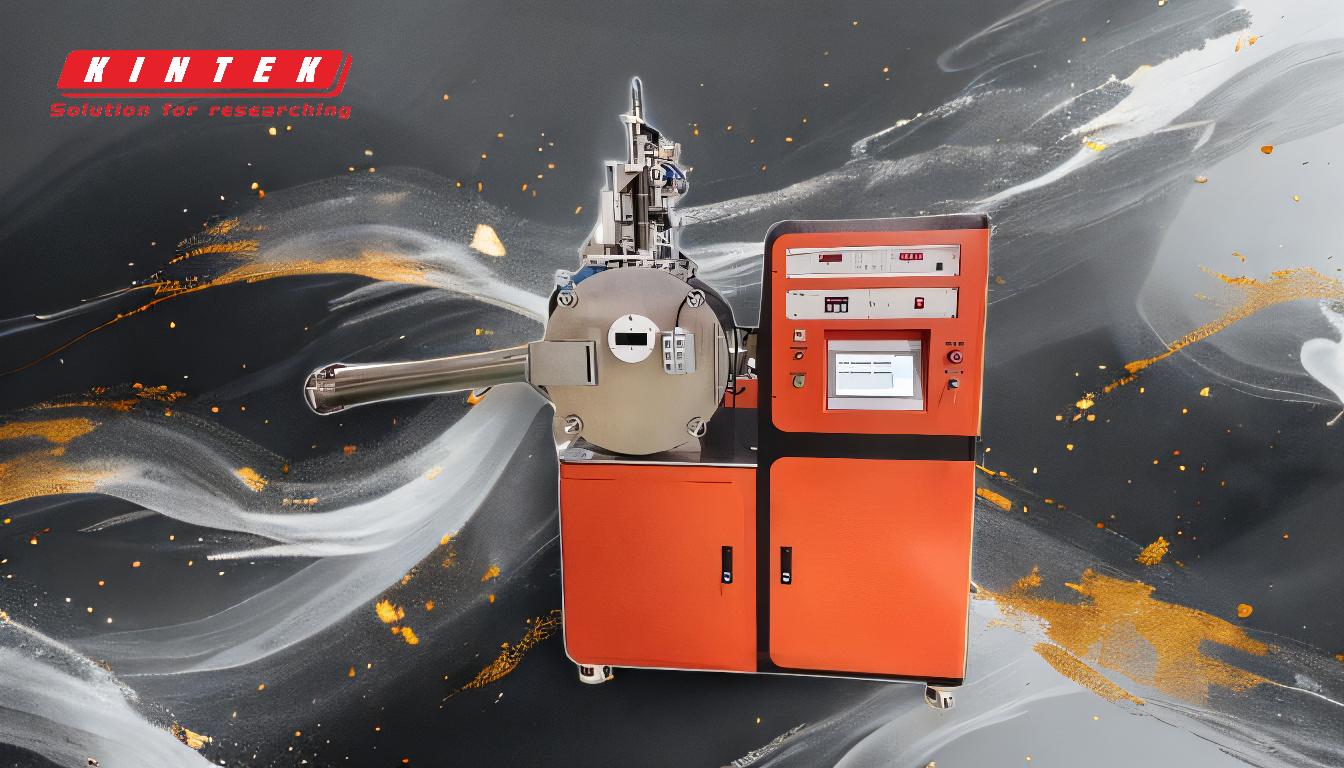
-
Cooling Rate and Microstructure:
- During casting, the cooling rate significantly influences the material's microstructure, which in turn affects its mechanical properties.
- Faster cooling rates, such as in die casting, can lead to finer grain structures, improving strength and hardness.
- Slower cooling rates, as in sand casting, may result in coarser grains, which can reduce strength but improve ductility.
- The microstructure formed during solidification determines properties like tensile strength, toughness, and fatigue resistance.
-
Material-Specific Changes:
- Metals: Metals like aluminum, steel, and cast iron exhibit changes in grain size, phase distribution, and porosity. For example, aluminum castings may develop porosity, reducing density and strength.
- Polymers: In polymer casting, cooling rates affect crystallinity. Faster cooling can lead to amorphous structures with higher transparency but lower strength.
- Ceramics: Ceramic casting involves sintering, which can alter density and thermal properties. Improper cooling may lead to cracking or warping.
-
Defects and Their Impact:
- Casting defects such as porosity, shrinkage cavities, and inclusions can weaken the material and reduce its fatigue life.
- These defects are often influenced by factors like mold design, pouring temperature, and cooling conditions.
- Post-casting treatments like heat treatment or hot isostatic pressing (HIP) can mitigate some defects and improve properties.
-
Post-Casting Treatments:
- Heat treatment processes like annealing, quenching, and tempering can refine the microstructure and enhance mechanical properties.
- Surface treatments, such as shot peening or coating, can improve wear resistance and fatigue life.
- These treatments are often necessary to achieve the desired balance of strength, ductility, and toughness.
-
Comparison with Other Manufacturing Processes:
- Casting generally results in lower mechanical properties compared to processes like forging or extrusion due to potential defects and coarser microstructures.
- However, casting allows for complex shapes and large parts that are difficult or impossible to produce with other methods.
- The choice of casting method (e.g., sand casting, investment casting, die casting) depends on the required properties and application.
-
Design Considerations for Casting:
- Engineers must account for potential changes in material properties when designing cast components.
- Factors like wall thickness, cooling channels, and gating systems can influence the final properties.
- Simulation tools are often used to predict and optimize microstructure and defect formation.
-
Applications and Trade-Offs:
- Casting is widely used in industries like automotive, aerospace, and construction due to its versatility and cost-effectiveness.
- While casting may reduce some material properties, it is often the best option for producing intricate or large-scale components.
- Understanding the trade-offs between properties, cost, and manufacturability is essential for selecting the right process.
By carefully controlling the casting process and applying appropriate post-casting treatments, manufacturers can optimize material properties to meet specific application requirements. However, it is important to recognize that casting inherently introduces changes to material properties, which must be accounted for in design and engineering decisions.
Summary Table:
Aspect | Impact on Material Properties |
---|---|
Cooling Rate | Faster cooling: finer grains, higher strength. Slower cooling: coarser grains, improved ductility. |
Material-Specific | Metals: porosity, grain size. Polymers: crystallinity. Ceramics: density, thermal properties. |
Defects | Porosity, shrinkage, and inclusions weaken material and reduce fatigue life. |
Post-Casting Treatments | Heat treatment and surface treatments enhance strength, ductility, and wear resistance. |
Design Considerations | Wall thickness, cooling channels, and gating systems influence final properties. |
Applications | Automotive, aerospace, and construction industries benefit from casting's versatility. |
Optimize your casting process for superior material performance—contact our experts today!