Hardening steel can indeed change its dimensions, but the extent and nature of these changes depend on several factors, including the type of steel, the hardening process used, and the initial state of the material. Hardening typically involves heating the steel to a high temperature and then rapidly cooling it, which can lead to changes in the microstructure of the steel. These microstructural changes can cause the steel to expand or contract, leading to dimensional changes. However, the exact impact on dimensions can vary, and in some cases, the changes may be minimal or negligible. Understanding the specific hardening process and the properties of the steel is crucial for predicting and managing these dimensional changes.
Key Points Explained:
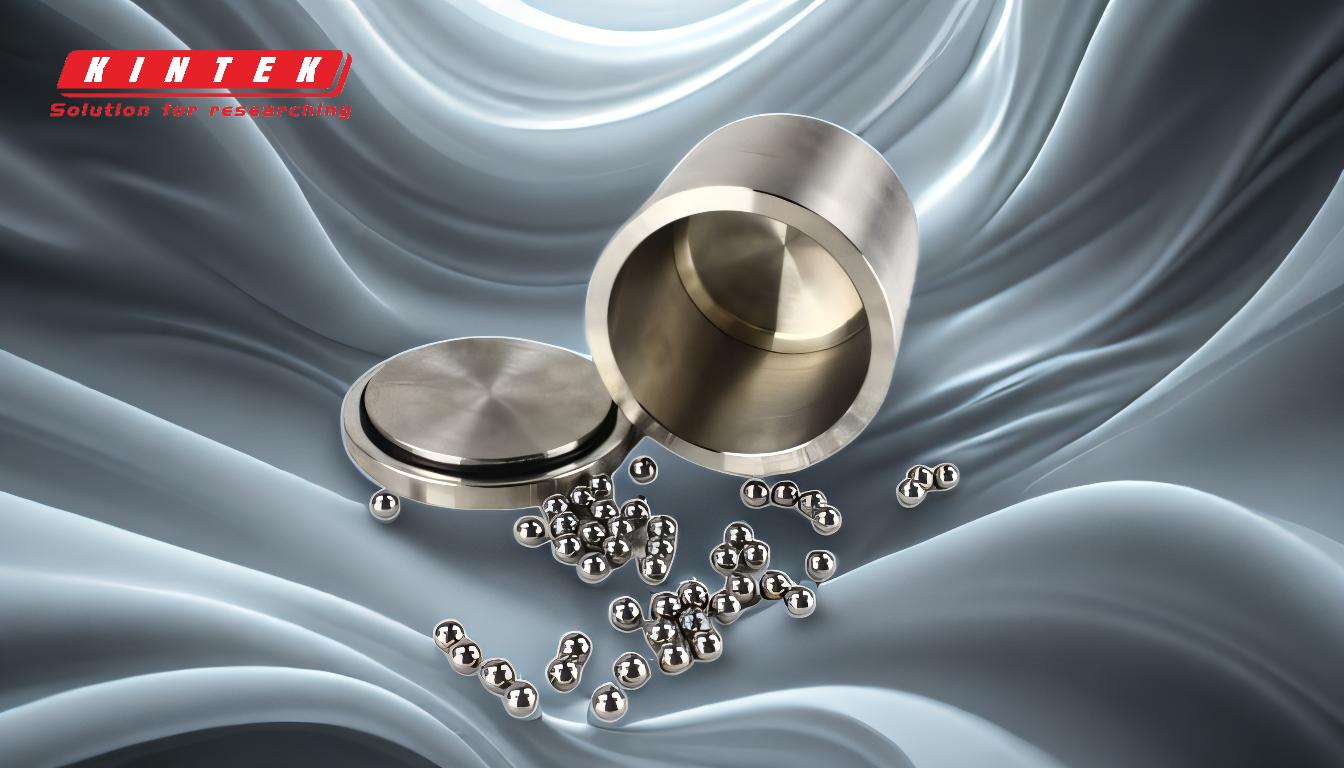
-
Hardening Process and Microstructural Changes:
- Hardening steel involves heating it to a high temperature (typically above its critical temperature) and then rapidly cooling it, often through quenching. This process transforms the steel's microstructure, typically from austenite to martensite, which is harder but more brittle.
- The transformation to martensite is accompanied by a volume expansion because the martensitic structure occupies more space than the original austenitic structure. This expansion can lead to an increase in the overall dimensions of the steel.
-
Factors Influencing Dimensional Changes:
- Type of Steel: Different types of steel have different compositions and microstructures, which can affect how much they expand or contract during hardening. For example, high-carbon steels are more likely to experience significant dimensional changes compared to low-carbon steels.
- Quenching Medium: The medium used for quenching (e.g., water, oil, or air) can influence the cooling rate and, consequently, the extent of dimensional changes. Faster cooling rates generally lead to greater dimensional changes.
- Initial State of the Material: The initial microstructure and stress state of the steel before hardening can also affect the final dimensions. For instance, if the steel has residual stresses from prior processing, these can be relieved or exacerbated during hardening.
-
Predicting and Managing Dimensional Changes:
- Precision Engineering: In applications where dimensional accuracy is critical, such as in precision engineering or tool manufacturing, it is essential to account for potential dimensional changes during the design and manufacturing process. This may involve allowing for some dimensional tolerance or using post-hardening processes like tempering to stabilize the dimensions.
- Tempering: After hardening, steel is often tempered to reduce brittleness and stabilize the microstructure. Tempering can also help to reduce residual stresses and minimize further dimensional changes.
- Simulation and Modeling: Advanced simulation and modeling techniques can be used to predict the dimensional changes that will occur during hardening. This allows manufacturers to adjust their processes and designs to achieve the desired final dimensions.
-
Practical Considerations:
- Warping and Distortion: In addition to uniform expansion or contraction, hardening can cause warping or distortion, especially in complex or asymmetrical parts. This is due to uneven cooling rates and the development of internal stresses.
- Surface Hardening vs. Through Hardening: Surface hardening processes, such as case hardening or induction hardening, primarily affect the surface layer of the steel. These processes may result in less overall dimensional change compared to through hardening, where the entire cross-section of the material is affected.
In summary, hardening steel can lead to dimensional changes due to microstructural transformations and the development of internal stresses. The extent of these changes depends on various factors, including the type of steel, the hardening process, and the initial state of the material. By understanding these factors and employing appropriate techniques, manufacturers can predict and manage dimensional changes to achieve the desired results.
Summary Table:
Key Factor | Impact on Dimensional Changes |
---|---|
Type of Steel | High-carbon steels experience more significant changes than low-carbon steels. |
Quenching Medium | Faster cooling rates (e.g., water) lead to greater dimensional changes. |
Initial State of Material | Residual stresses from prior processing can influence final dimensions. |
Tempering | Reduces brittleness and stabilizes dimensions post-hardening. |
Warping/Distortion | Complex parts may warp due to uneven cooling rates and internal stresses. |
Surface vs. Through Hardening | Surface hardening causes less overall dimensional change compared to through hardening. |
Need help managing dimensional changes in hardened steel? Contact our experts today for tailored solutions!