Heating metal can indeed affect its strength, but the outcome depends on the specific temperature, duration of heating, and the type of metal involved. Metals undergo various structural changes when heated, such as annealing, tempering, or hardening, which can either weaken or strengthen the material. For example, heating metal to high temperatures for extended periods can cause grain growth, reducing its strength. Conversely, controlled heating and cooling processes like tempering can enhance strength and durability. Understanding these effects is crucial for applications in manufacturing, construction, and engineering where metal strength is a critical factor.
Key Points Explained:
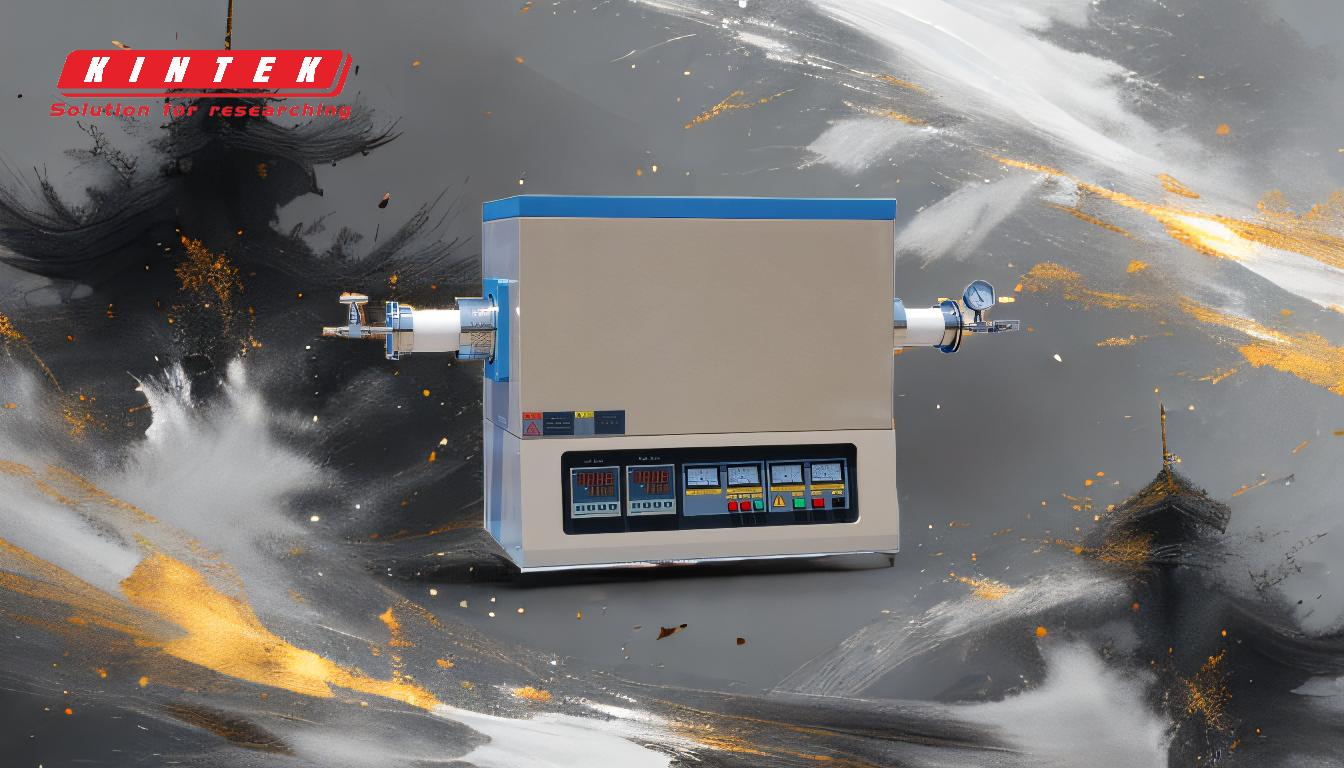
-
Effect of Heating on Metal Strength:
- Heating metal can lead to changes in its microstructure, which directly impacts its mechanical properties. When metals are heated, their atomic structure becomes more mobile, allowing for rearrangement. This can result in softening or hardening, depending on the process.
- For instance, annealing involves heating metal to a specific temperature and then cooling it slowly, which reduces internal stresses and increases ductility but may decrease hardness. On the other hand, quenching (rapid cooling) after heating can increase hardness but may also make the metal more brittle.
-
Temperature and Duration:
- The temperature to which a metal is heated and the duration of heating are critical factors. Mild heating may not significantly alter the metal's properties, but prolonged exposure to high temperatures can lead to grain growth, where the metal's crystalline structure becomes coarser. This grain growth typically reduces the metal's strength and toughness.
- For example, steel heated above its critical temperature (around 727°C for most carbon steels) and then cooled slowly will undergo annealing, making it softer and more workable. However, if the same steel is rapidly cooled (quenched), it becomes harder but more brittle.
-
Type of Metal:
- Different metals respond differently to heating. For example, aluminum alloys can be heat-treated to improve strength, while some stainless steels may become weaker if heated excessively.
- The presence of alloying elements also plays a role. Alloying elements like chromium, nickel, or molybdenum can enhance a metal's ability to retain strength at high temperatures, making it suitable for applications like turbine blades or engine components.
-
Applications and Implications:
- In manufacturing, understanding how heating affects metal strength is essential for processes like forging, welding, and heat treatment. Forging involves shaping metal by heating it to a malleable state, which can refine its grain structure and improve strength.
- In construction, metals used in structural applications must maintain their strength under varying temperatures. For example, steel beams in buildings are designed to withstand both high and low temperatures without significant loss of strength.
-
Controlled Heating Processes:
- Controlled heating processes like tempering, normalizing, and case hardening are used to achieve specific mechanical properties. Tempering, for instance, involves reheating quenched steel to a lower temperature to reduce brittleness while maintaining hardness.
- These processes are tailored to the intended use of the metal, ensuring it meets the required strength, ductility, and toughness for its application.
In summary, heating metal can make it weaker or stronger depending on the process and conditions. Proper understanding and control of heating parameters are essential to achieve the desired mechanical properties for specific applications.
Summary Table:
Factor | Impact on Metal Strength |
---|---|
Temperature | High temperatures can weaken metals by causing grain growth, while controlled heat can strengthen them. |
Duration of Heating | Prolonged heating reduces strength, but short, controlled processes like tempering improve it. |
Type of Metal | Different metals (e.g., aluminum, steel) respond uniquely to heat, affecting strength differently. |
Heating Processes | Annealing softens metal, quenching increases hardness, and tempering balances strength and ductility. |
Applications | Critical for manufacturing, construction, and engineering to ensure optimal metal performance. |
Need expert advice on how heating affects metal strength? Contact us today for tailored solutions!