Molds for injection molding are primarily manufactured using advanced industrial techniques such as CNC machining and electric discharge machining (EDM). These methods are chosen for their precision and ability to create durable molds from metal, which are essential for high-volume production. The process involves specialized equipment, sophisticated software, and skilled labor, making it a costly but necessary investment for producing high-quality molds. Below, we explore the key steps and considerations involved in mold manufacturing.
Key Points Explained:
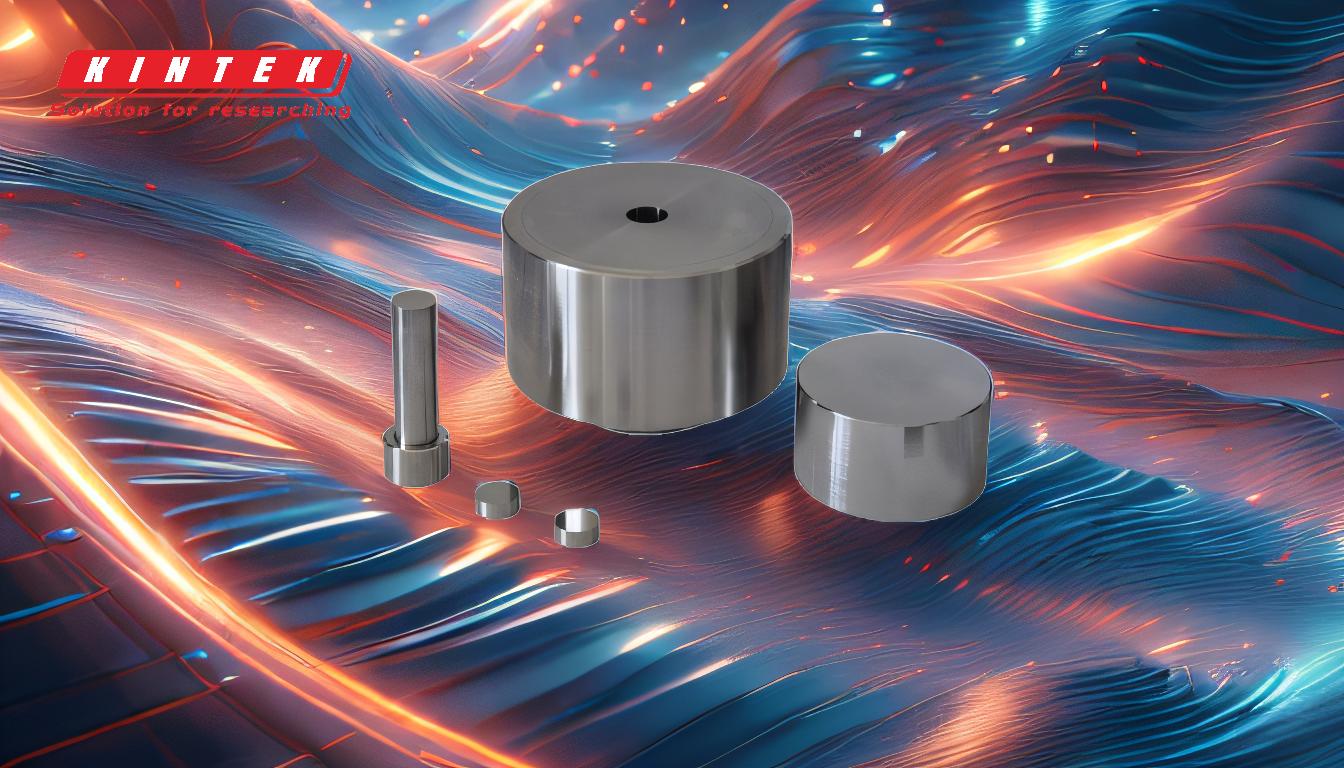
-
Material Selection for Molds
- Molds are typically made from metals like steel or aluminum due to their durability, heat resistance, and ability to withstand high pressure during the injection molding process.
- Steel molds are preferred for high-volume production because of their longevity, while aluminum molds are used for prototyping or low-volume runs due to their lower cost and faster machining time.
-
CNC Machining
- CNC (Computer Numerical Control) machining is a widely used method for mold manufacturing. It involves using computer-controlled machines to precisely cut and shape the metal into the desired mold design.
- Advantages:
- High precision and repeatability.
- Ability to create complex geometries.
- Challenges:
- Requires advanced software for design (e.g., CAD/CAM).
- High initial cost for equipment and skilled operators.
-
Electric Discharge Machining (EDM)
- EDM is used for creating intricate details or hard-to-machine features in molds. It works by using electrical discharges to erode the metal into the desired shape.
- Advantages:
- Ideal for hard metals and complex designs.
- Produces fine surface finishes.
- Challenges:
- Slower process compared to CNC machining.
- Higher energy consumption and operational costs.
-
Design and Prototyping
- Before manufacturing, molds are designed using CAD (Computer-Aided Design) software to ensure accuracy and functionality.
- Prototyping may involve creating a test mold (often in aluminum) to validate the design before committing to full-scale production.
-
Surface Treatment and Finishing
- After machining, molds undergo surface treatments like polishing, coating, or heat treatment to enhance durability, reduce friction, and improve the quality of the final molded product.
-
Quality Control and Testing
- Finished molds are rigorously tested to ensure they meet design specifications and performance standards. This includes checking dimensions, surface finish, and functionality during trial runs.
-
Cost and Time Considerations
- Mold manufacturing is a time-intensive and expensive process due to the need for specialized equipment, skilled labor, and high-quality materials.
- However, the investment is justified by the mold's ability to produce thousands or even millions of parts with consistent quality.
-
Emerging Technologies
- While traditional methods like CNC and EDM dominate, additive manufacturing (3D printing) is emerging as a complementary technology for creating molds, especially for prototyping or low-volume production.
In summary, mold manufacturing is a sophisticated process that combines advanced machining techniques, meticulous design, and rigorous testing to create durable and precise tools for injection molding. The choice of method and materials depends on factors like production volume, part complexity, and budget, with CNC machining and EDM being the most common approaches. While the process is costly and time-consuming, it is essential for producing high-quality molds that meet the demands of modern manufacturing.
Summary Table:
Key Aspect | Details |
---|---|
Material Selection | Steel for high-volume production; aluminum for prototyping/low-volume runs. |
CNC Machining | High precision, complex geometries; requires CAD/CAM software and skilled labor. |
EDM | Ideal for hard metals and intricate designs; slower process, higher costs. |
Design & Prototyping | CAD software ensures accuracy; prototyping validates design before production. |
Surface Treatment | Polishing, coating, or heat treatment enhances durability and surface finish. |
Quality Control | Rigorous testing ensures dimensions, finish, and functionality meet standards. |
Cost & Time | High investment due to equipment, labor, and materials; justified by quality. |
Emerging Technologies | Additive manufacturing (3D printing) complements traditional methods. |
Need high-quality molds for your injection molding projects? Contact our experts today to get started!