Improving the efficiency of an induction furnace involves optimizing various aspects of its operation, including power supply, coil design, material handling, and maintenance. By focusing on these areas, you can reduce energy consumption, enhance melting rates, and extend the lifespan of the furnace. Key strategies include upgrading to advanced power systems like IGBT induction furnaces, optimizing coil configurations, ensuring proper material loading, and implementing regular maintenance practices. Additionally, adopting smart control systems and monitoring tools can further enhance operational efficiency. This approach not only reduces costs but also improves the overall performance of the furnace in industrial applications.
Key Points Explained:
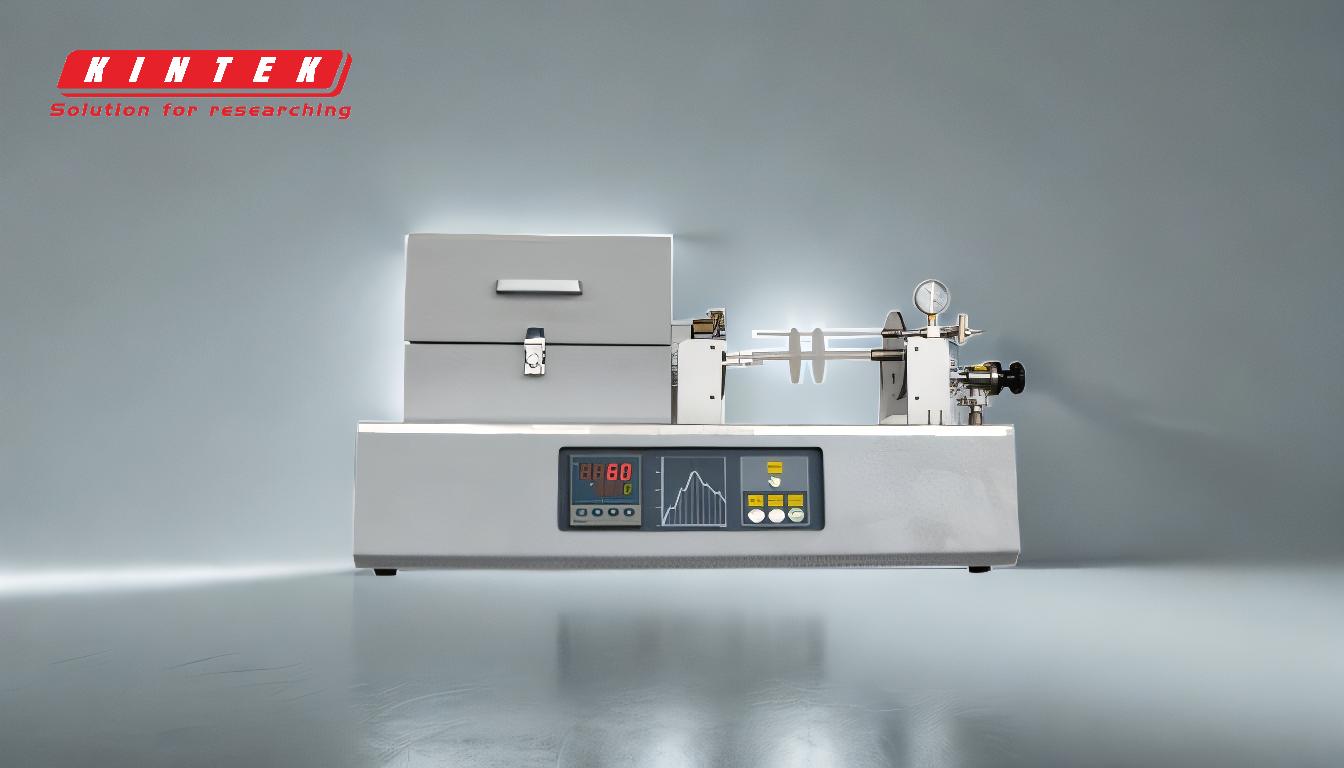
-
Upgrade to IGBT Induction Furnace Technology
- IGBT induction furnaces are known for their high efficiency and precise control over power output. Unlike traditional SCR-based systems, IGBTs provide better power factor correction and reduced harmonic distortion, leading to significant energy savings.
- These systems also offer faster switching frequencies, which improve heat distribution and reduce melting times. Upgrading to an IGBT-based system can result in a 10-20% improvement in overall efficiency.
-
Optimize Coil Design and Configuration
- The induction coil is a critical component that directly impacts furnace efficiency. Ensuring the coil is properly designed and matched to the load can minimize energy losses.
- Use high-quality, water-cooled copper coils with appropriate turns and spacing to maximize magnetic coupling and heat transfer. Regularly inspect coils for wear and tear to prevent inefficiencies caused by damage or misalignment.
-
Proper Material Loading and Charging Practices
- Efficient material handling is essential for maintaining furnace efficiency. Avoid overloading or underloading the furnace, as both can lead to energy wastage.
- Use preheated materials when possible to reduce the energy required for melting. Properly sized and shaped charge materials also ensure uniform heating and faster melting rates.
-
Implement Regular Maintenance and Inspection
- Regular maintenance of the furnace components, including the crucible, coils, and cooling systems, is crucial for sustained efficiency.
- Clean the furnace interior to remove slag and debris, which can act as insulators and reduce heat transfer. Inspect and replace worn-out components promptly to avoid breakdowns and inefficiencies.
-
Adopt Advanced Control and Monitoring Systems
- Modern induction furnaces can be equipped with smart control systems that optimize power usage and monitor operational parameters in real-time.
- These systems provide insights into energy consumption patterns, allowing operators to make data-driven adjustments for improved efficiency. Features like automatic power regulation and fault detection further enhance performance.
-
Focus on Thermal Insulation and Heat Recovery
- Effective thermal insulation around the furnace reduces heat loss to the environment, ensuring more energy is directed toward the melting process.
- Consider implementing heat recovery systems to capture and reuse waste heat generated during operation. This can be used for preheating materials or other industrial processes, further improving overall efficiency.
-
Train Operators for Optimal Usage
- Skilled operators play a significant role in maximizing furnace efficiency. Provide training on best practices for furnace operation, including proper loading, power management, and troubleshooting.
- Encourage operators to monitor and record performance metrics regularly, enabling continuous improvement in furnace operations.
By addressing these key areas, you can significantly improve the efficiency of your induction furnace, leading to cost savings, enhanced productivity, and reduced environmental impact.
Summary Table:
Key Strategy | Benefits |
---|---|
Upgrade to IGBT Induction Furnace | 10-20% efficiency improvement, precise power control, reduced energy loss |
Optimize Coil Design | Minimized energy losses, improved heat transfer, and durability |
Proper Material Loading | Uniform heating, faster melting rates, and reduced energy waste |
Regular Maintenance | Sustained efficiency, reduced breakdowns, and extended furnace lifespan |
Smart Control Systems | Real-time monitoring, optimized power usage, and fault detection |
Thermal Insulation & Heat Recovery | Reduced heat loss, waste heat reuse, and improved overall efficiency |
Operator Training | Skilled operation, better power management, and continuous improvement |
Ready to optimize your induction furnace? Contact our experts today for tailored solutions!