Temperature control in a resistance furnace is a critical aspect of ensuring efficient and precise heating processes. It involves regulating the power input to the furnace to maintain a desired temperature, using various methods such as adjusting voltage, resistance, or the on-off cycle of the heating elements. Advanced systems incorporate temperature sensors, controllers, and power regulation technologies like SCR (Silicon Controlled Rectifier) or PID (Proportional-Integral-Derivative) control to achieve accurate and stable temperature management. The choice of method depends on the furnace type, application, and desired precision.
Key Points Explained:
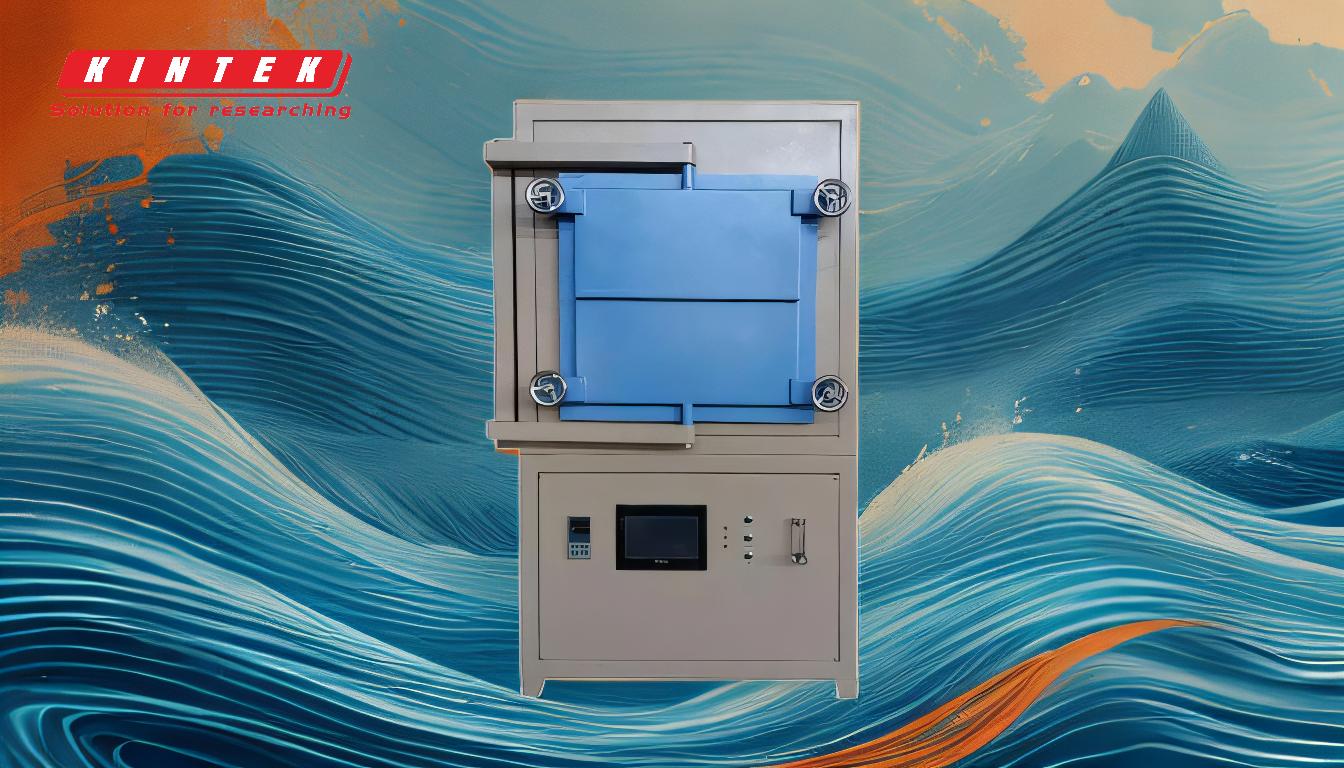
-
Power Regulation Methods:
- SCR Power Regulation: This method controls the temperature by adjusting the number of heating voltage sine waves through the on-off state of the SCR in a given period. It is a precise and efficient way to regulate power input to the furnace.
- Voltage Variation: Temperature can be controlled by varying the applied voltage to the heating elements. This can be achieved using transformer tappings, auto-transformers, or induction regulators.
- Resistance Variation: Adjusting the resistance of the heating elements can also regulate temperature, though this method is less common in practice.
- On-Off Cycle Control: The ratio of on and off times of the power supply can be varied to control temperature, which is a simpler but less precise method.
-
Temperature Sensors and Controllers:
- Thermocouples: These sensors detect the furnace temperature and transmit the signal to a controller. The controller adjusts the power input based on the set temperature curve.
- PID Control: This advanced method calculates the energy required to maintain a set temperature while considering heat loss. It is the most energy-efficient and precise method for temperature regulation.
-
Control Systems:
- Proportional Control: This system adjusts the fuel and air supply to maintain a consistent temperature, improving fuel efficiency and reducing operating costs.
- Pulse Control: This method maintains a fixed ratio of fuel and air with high flame velocity, ensuring consistent temperatures throughout the process cycle.
- Basic Systems: These systems only regulate fuel flow and are cost-effective but less efficient compared to proportional or pulse control systems.
-
Medium Control in Laboratory Furnaces:
- Flow and Pressure Control: Temperature in laboratory furnaces is controlled by regulating the outlet temperature, flow rate, and pressure of the medium. Flow control is applied before the medium enters the furnace, and pressure control is applied after it enters, ensuring effective temperature regulation.
-
Advanced Technologies:
- Thermostat: A simple on/off switch that maintains a set temperature.
- Proportional Control: This method eases heating as it approaches the preheat value to prevent overheating.
- PID Control: The most energy-efficient method, which calculates the required energy to maintain a set temperature while considering heat loss.
-
Large Furnaces:
- Independent Generating Sets: In large furnaces, an independent generating set may provide a variable voltage supply, allowing for precise temperature control.
By understanding and implementing these methods, one can effectively control the temperature inside a resistance furnace, ensuring optimal performance and efficiency for various industrial and laboratory applications.
Summary Table:
Method | Description |
---|---|
SCR Power Regulation | Adjusts heating voltage sine waves for precise power input control. |
Voltage Variation | Varies applied voltage using transformers or regulators. |
Resistance Variation | Adjusts heating element resistance (less common). |
On-Off Cycle Control | Varies power supply on/off times for simpler temperature control. |
Thermocouples | Detect temperature and transmit signals to controllers. |
PID Control | Calculates energy needs for set temperature, considering heat loss. |
Proportional Control | Adjusts fuel and air supply for consistent temperature and efficiency. |
Pulse Control | Maintains fixed fuel/air ratio with high flame velocity. |
Flow and Pressure Control | Regulates medium flow and pressure in laboratory furnaces. |
Thermostat | Simple on/off switch for maintaining set temperature. |
Independent Generating Sets | Provides variable voltage for precise control in large furnaces. |
Need precise temperature control for your resistance furnace? Contact our experts today for tailored solutions!