Cleaning before PVD (Physical Vapor Deposition) coating is a critical step to ensure the quality and adhesion of the coating. The process involves removing contaminants such as oils, oxides, EDM recast layers, and organic films that can interfere with the coating's performance. Techniques like ultrasonic cleaning, rinsing, drying, polishing, tumbling, acid etching, and sand or glass-bead blasting are commonly used. These methods ensure that the surface is free of impurities, allowing the PVD coating to adhere properly and perform as intended.
Key Points Explained:
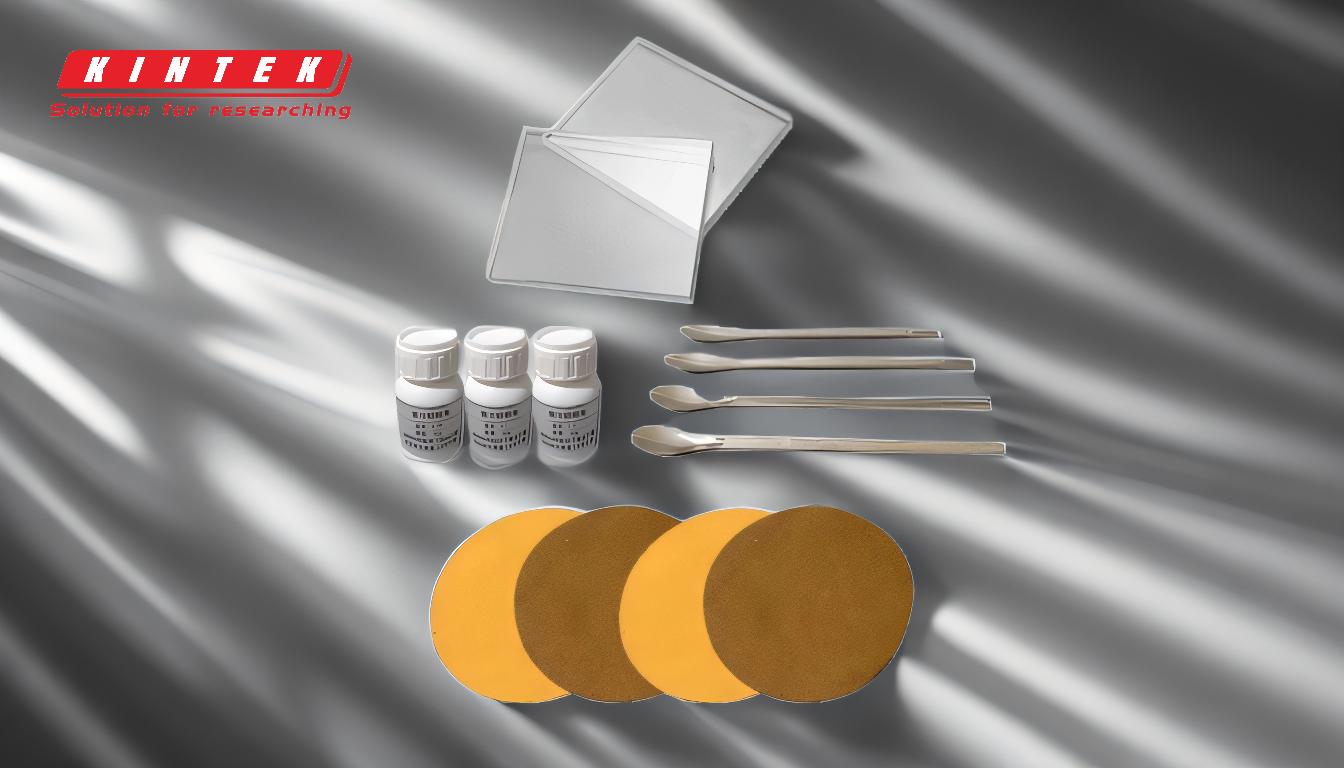
-
Importance of Cleaning Before PVD Coating
- Contaminants like oils, oxides, and organic films can negatively impact the adhesion and quality of the PVD coating.
- Proper cleaning ensures a clean surface, which is essential for achieving a durable and well-adhered coating.
-
Common Contaminants to Remove
- Oils and Greases: Often left from machining or handling, these can prevent proper adhesion.
- Oxides: Surface oxides can interfere with the bonding of the coating.
- EDM Recast Layers: Residues from electrical discharge machining (EDM) need to be removed.
- Organic Films: These can include residues from fingerprints or other organic materials.
-
Cleaning Techniques
-
Ultrasonic Cleaning:
- Uses high-frequency sound waves in a liquid cleaning solution to remove contaminants.
- Environmentally friendly detergents are often used to ensure thorough cleaning without harming the material.
-
Rinsing:
- After ultrasonic cleaning, parts are rinsed to remove any remaining detergent or loosened contaminants.
- Deionized water is commonly used to avoid introducing new impurities.
-
Drying:
- Parts are dried completely to prevent water spots or residual moisture, which can affect coating adhesion.
-
Polishing and Tumbling:
- Mechanical methods to smooth surfaces and remove surface imperfections.
-
Acid Etching:
- Chemical treatment to remove oxides and other surface contaminants.
-
Sand or Glass-Bead Blasting:
- Abrasive techniques to clean and prepare the surface for coating.
-
Ultrasonic Cleaning:
-
Sequence of Cleaning Steps
- The cleaning process is typically performed in a specific sequence:
- Initial Cleaning: Remove gross contaminants using mechanical methods like tumbling or blasting.
- Ultrasonic Cleaning: Deep clean to remove finer contaminants.
- Rinsing: Ensure no cleaning solution residues remain.
- Drying: Prepare the surface for the PVD coating process.
- The cleaning process is typically performed in a specific sequence:
-
Environmental Considerations
- Environmentally friendly detergents are often used in ultrasonic cleaning to minimize environmental impact.
- Proper disposal of cleaning solutions and waste materials is essential to comply with environmental regulations.
-
Quality Control and Inspection
- After cleaning, parts are often inspected to ensure they are free of contaminants.
- Techniques like visual inspection, magnification, or surface analysis may be used to verify cleanliness.
By following these steps, the surface is properly prepared for PVD coating, ensuring optimal adhesion, durability, and performance of the final product.
Summary Table:
Key Aspect | Details |
---|---|
Importance of Cleaning | Ensures proper adhesion and durability of PVD coatings. |
Common Contaminants | Oils, oxides, EDM recast layers, and organic films. |
Cleaning Techniques | Ultrasonic cleaning, rinsing, drying, polishing, acid etching, blasting. |
Cleaning Sequence | 1. Initial cleaning 2. Ultrasonic cleaning 3. Rinsing 4. Drying. |
Environmental Considerations | Use eco-friendly detergents and proper waste disposal. |
Quality Control | Inspect parts post-cleaning for contamination-free surfaces. |
Ensure your PVD coating process delivers top results—contact our experts today for tailored cleaning solutions!