To control the temperature of a heating element, a combination of sensors, controllers, and feedback mechanisms is typically employed. The process involves measuring the current temperature, comparing it to the desired setpoint, and adjusting the power supplied to the heating element accordingly. Key methods include using thermostats, thermocouples, or resistance temperature detectors (RTDs) as sensors, and employing proportional-integral-derivative (PID) controllers or on/off control systems to regulate power. Advanced systems may incorporate microprocessors or programmable logic controllers (PLCs) for precise and automated temperature management. Proper insulation and heat distribution also play a critical role in maintaining consistent temperatures.
Key Points Explained:
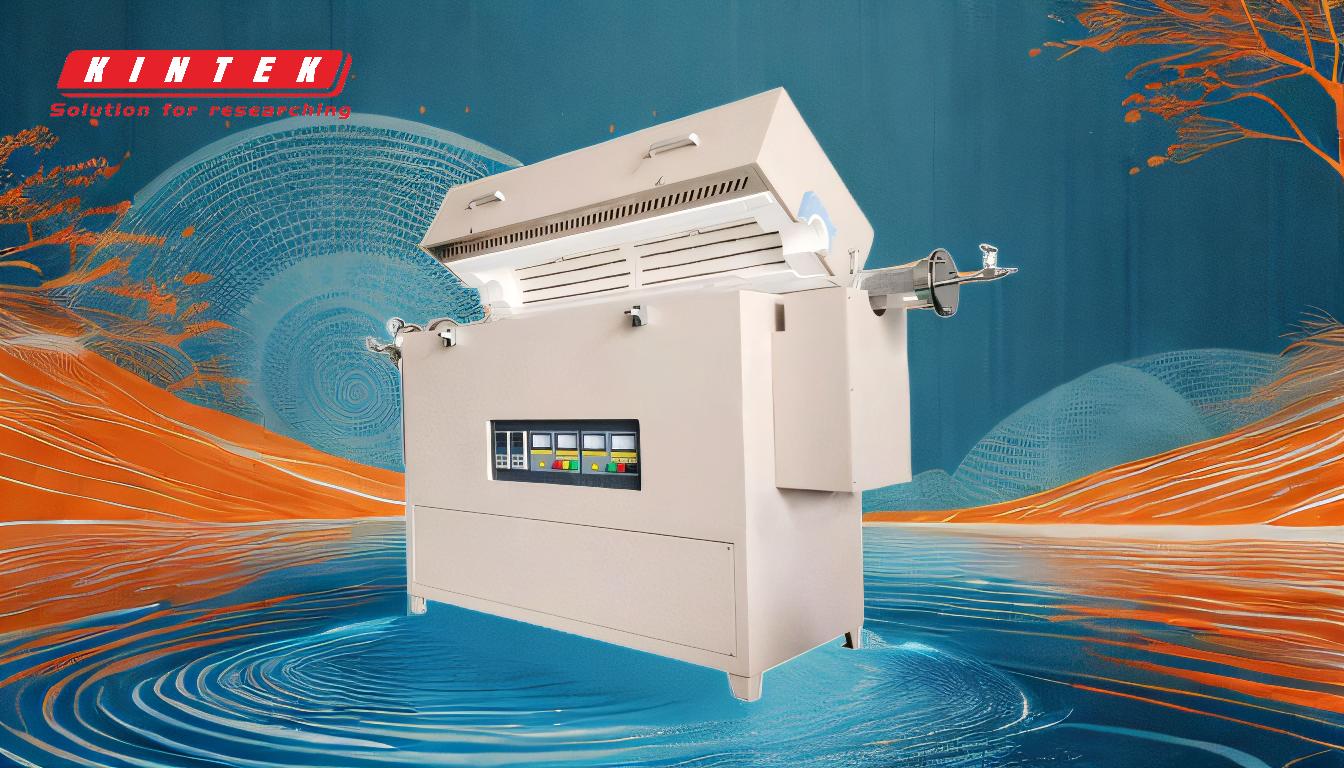
-
Temperature Sensing Mechanisms:
- Thermocouples: These are widely used due to their wide temperature range and durability. They generate a voltage proportional to the temperature difference between two junctions.
- Resistance Temperature Detectors (RTDs): RTDs provide high accuracy and stability by measuring the change in electrical resistance of a metal (usually platinum) as temperature changes.
- Thermistors: These are temperature-sensitive resistors that offer high sensitivity within a limited temperature range.
- Infrared Sensors: Non-contact sensors that measure temperature by detecting infrared radiation emitted by the heating element.
-
Control Systems:
- On/Off Control: The simplest method, where the heating element is turned fully on or off based on whether the temperature is below or above the setpoint. This can cause oscillations around the desired temperature.
- Proportional Control: Adjusts the power supplied to the heating element in proportion to the difference between the current temperature and the setpoint, reducing oscillations.
- PID Control (Proportional-Integral-Derivative): Combines proportional control with integral and derivative actions to achieve precise and stable temperature regulation. The integral term eliminates steady-state errors, while the derivative term reduces overshoot.
-
Power Regulation Techniques:
- Pulse Width Modulation (PWM): Rapidly switches the power on and off to the heating element, controlling the average power delivered by adjusting the duty cycle.
- Phase-Angle Control: Adjusts the phase angle of the AC voltage waveform to control the power delivered to the heating element.
- Solid-State Relays (SSRs): Used for precise and fast switching of power to the heating element, often in conjunction with PID controllers.
-
Feedback Loops:
- A feedback loop continuously monitors the temperature using sensors and adjusts the power to the heating element to maintain the desired setpoint. This ensures stability and accuracy in temperature control.
-
Advanced Control Systems:
- Microprocessors and PLCs: These allow for programmable and automated temperature control, enabling complex control strategies and integration with other systems.
- Data Logging and Remote Monitoring: Advanced systems can log temperature data and allow remote monitoring and control, enhancing process reliability and traceability.
-
Heat Distribution and Insulation:
- Proper insulation minimizes heat loss, ensuring efficient use of energy and consistent temperature control.
- Uniform heat distribution is achieved through careful design of the heating element and its placement, preventing hot spots and ensuring even heating.
-
Safety Considerations:
- Over-temperature protection mechanisms, such as thermal fuses or limit switches, are essential to prevent damage or hazards.
- Redundant sensors and fail-safe controls can enhance system reliability.
By combining these elements, temperature control of a heating element can be achieved with precision, efficiency, and safety, meeting the needs of various applications.
Summary Table:
Component | Key Features |
---|---|
Temperature Sensors | - Thermocouples: Wide range, durable |
- RTDs: High accuracy, stable | |
- Thermistors: High sensitivity, limited range | |
- Infrared Sensors: Non-contact, measures radiation | |
Control Systems | - On/Off Control: Simple, causes oscillations |
- Proportional Control: Reduces oscillations | |
- PID Control: Precise, stable, eliminates errors | |
Power Regulation | - PWM: Adjusts power via duty cycle |
- Phase-Angle Control: Adjusts AC voltage phase | |
- SSRs: Fast, precise switching | |
Advanced Systems | - Microprocessors/PLCs: Programmable, automated control |
- Data Logging & Remote Monitoring: Enhances reliability | |
Safety & Efficiency | - Over-temperature protection: Prevents hazards |
- Insulation & Heat Distribution: Ensures consistency and energy efficiency |
Need help with temperature control for your heating element? Contact our experts today for tailored solutions!