Preparing carbon nanotubes (CNTs) using chemical vapor deposition (CVD) is a widely adopted commercial method due to its cost-effectiveness, structural controllability, and relatively lower environmental impact compared to traditional methods like laser ablation and arc discharge. The process involves thermal treatments, gas-phase rearrangement, and catalyst deposition to synthesize CNTs. Catalytic chemical vapor deposition (CCVD) is the most common approach, offering precise control over the nanotube structure. To minimize environmental impact, it is essential to optimize material and energy consumption while reducing greenhouse gas emissions during the synthesis process.
Key Points Explained:
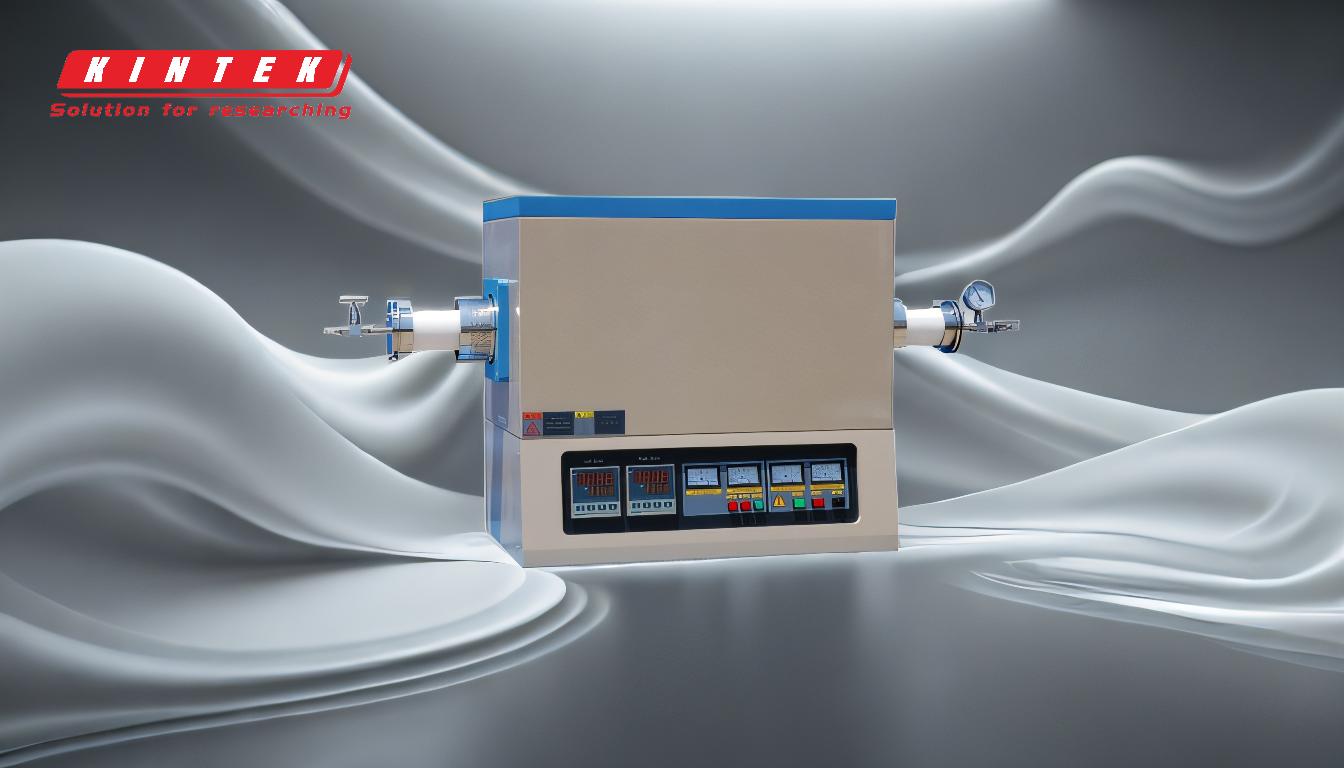
-
Overview of CVD for CNT Synthesis:
- Chemical vapor deposition (CVD) is a dominant method for producing carbon nanotubes commercially.
- It involves the decomposition of carbon-containing gases at high temperatures in the presence of a catalyst.
- This method is preferred over traditional techniques like laser ablation and arc discharge due to its scalability, cost-effectiveness, and ability to control nanotube structure.
-
Steps in the CVD Process:
- Catalyst Preparation: A catalyst, typically a transition metal like iron, cobalt, or nickel, is deposited on a substrate. The catalyst plays a crucial role in initiating and guiding the growth of CNTs.
- Gas Introduction: A carbon-containing gas, such as methane, ethylene, or acetylene, is introduced into the reaction chamber.
- Thermal Decomposition: The reaction chamber is heated to high temperatures (600–1200°C), causing the carbon-containing gas to decompose. The carbon atoms are then deposited onto the catalyst particles.
- Nucleation and Growth: Carbon atoms diffuse through or around the catalyst particles, forming carbon nanotubes. The size and structure of the CNTs depend on the catalyst size and reaction conditions.
- Cooling and Collection: After synthesis, the system is cooled, and the CNTs are collected from the substrate.
-
Catalytic Chemical Vapor Deposition (CCVD):
- CCVD is the most widely used CVD method for CNT synthesis.
- It offers better control over the diameter, length, and alignment of CNTs.
- The catalyst is critical in determining the quality and yield of the nanotubes.
-
Environmental Considerations:
- The synthesis process is a key contributor to the life cycle ecotoxicity of CNTs.
- To minimize environmental impact, it is important to:
- Optimize material consumption (e.g., catalyst and carbon feedstock).
- Reduce energy consumption during thermal treatments.
- Limit greenhouse gas emissions by using efficient gas handling systems.
-
Emerging Trends in CNT Synthesis:
- Researchers are exploring the use of green or waste feedstocks, such as carbon dioxide captured by electrolysis in molten salts or methane pyrolysis.
- These methods aim to further reduce the environmental footprint of CNT production while maintaining high-quality output.
By following these steps and considerations, CVD provides a reliable and efficient method for producing carbon nanotubes with controlled properties and reduced environmental impact.
Summary Table:
Step | Description |
---|---|
Catalyst Preparation | Deposit a transition metal catalyst (e.g., iron, cobalt, nickel) on a substrate. |
Gas Introduction | Introduce carbon-containing gas (e.g., methane, ethylene) into the chamber. |
Thermal Decomposition | Heat to 600–1200°C to decompose gas and deposit carbon atoms on the catalyst. |
Nucleation and Growth | Carbon atoms form nanotubes, guided by the catalyst. |
Cooling and Collection | Cool the system and collect synthesized CNTs from the substrate. |
Discover how CVD can revolutionize your carbon nanotube production—contact our experts today!