A crucible furnace is a specialized piece of equipment used for melting metals and other materials by heating them to their melting points within a crucible. The furnace operates by generating heat through a heating element, which can be powered by electricity, natural gas, propane, or oil. This heat is transferred to the crucible, a container made of high-temperature-resistant materials like graphite, clay, or silicon carbide. Once the material inside the crucible reaches its melting point, it becomes molten and can be poured into molds or containers to take the desired shape. The process is controlled by adjusting the heat or using a temperature control system, and the furnace's design and size can influence the melting time and efficiency.
Key Points Explained:
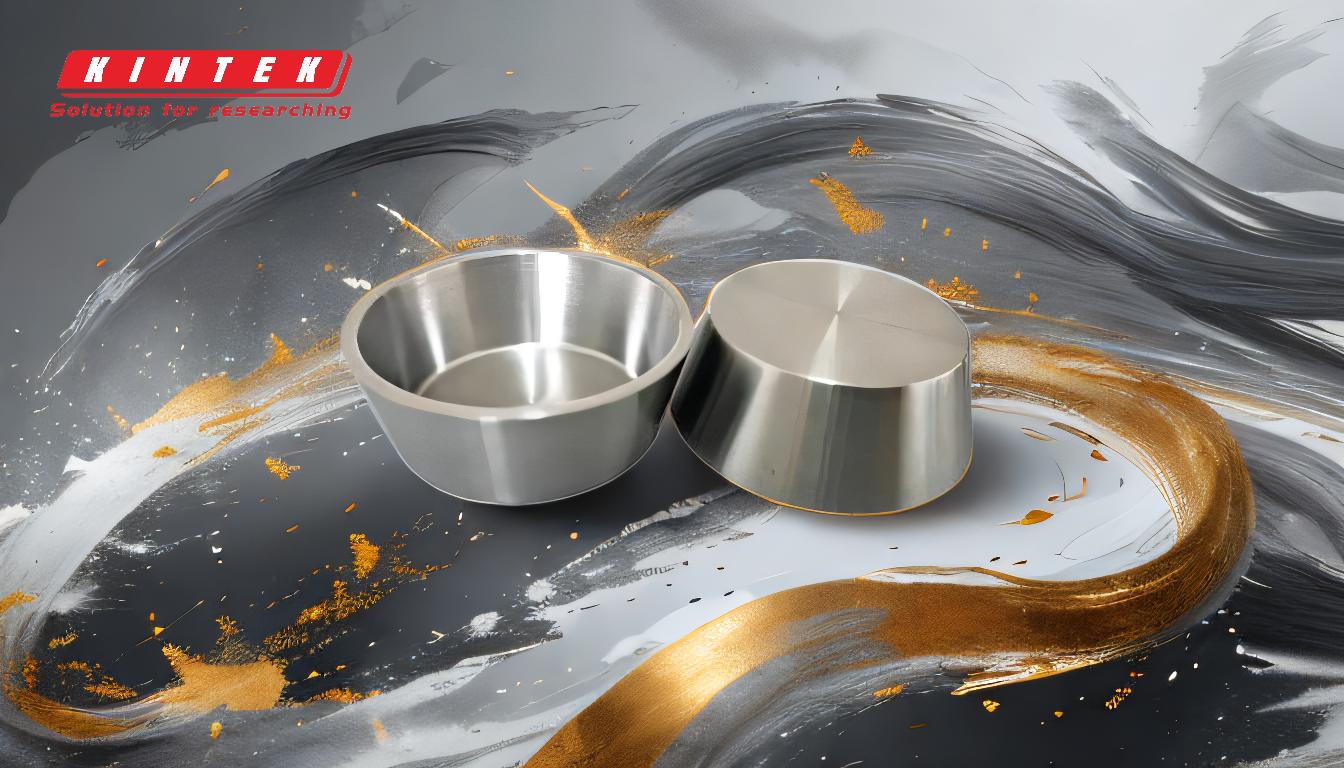
-
Heating Mechanism:
- The crucible furnace generates heat through a heating element, which can be powered by electricity, natural gas, propane, or oil.
- The heat is transferred to the crucible, which is made of materials capable of withstanding high temperatures, such as graphite, clay, or silicon carbide.
-
Crucible Function:
- The crucible is a container that holds the material to be melted. It is designed to withstand extreme temperatures and chemical reactions with the molten material.
- The crucible is placed inside the furnace chamber, which is lined with refractory materials to retain heat and protect the furnace structure.
-
Melting Process:
- The material inside the crucible is heated until it reaches its melting point, at which point it becomes molten.
- The melting process can be controlled by adjusting the heat output or using a temperature control system to maintain the desired temperature.
-
Pouring and Shaping:
- Once the material is molten, it is poured into molds or containers to take the desired shape.
- The furnace may be designed to tilt, allowing for complete emptying of the crucible and efficient pouring of the molten material.
-
Furnace Design and Efficiency:
- The size and design of the furnace can impact the melting time and overall efficiency.
- Features such as a swivelable lid help save energy and minimize heat dissipation, while an exhaust channel vents flue gases.
- The furnace may include an opening at the bottom for tapping in case of crucible breakage, ensuring safety and ease of maintenance.
-
Applications:
- Crucible furnaces are commonly used in foundries for melting and casting metals with low melting points, such as brass, bronze, and aluminum.
- They are one of the oldest types of melting ovens and remain widely used in the industry due to their simplicity and effectiveness.
-
Control and Safety:
- The process can be precisely controlled using temperature control systems, ensuring consistent results and preventing overheating.
- Safety features, such as refractory linings and tiltable designs, help protect operators and equipment from the high temperatures and potential hazards associated with melting metals.
By understanding these key points, a purchaser can make informed decisions about the type of crucible furnace that best meets their needs, considering factors such as the materials to be melted, desired production capacity, and available energy sources.
Summary Table:
Aspect | Details |
---|---|
Heating Mechanism | Powered by electricity, natural gas, propane, or oil. |
Crucible Material | Made of graphite, clay, or silicon carbide for high-temperature resistance. |
Melting Process | Controlled via heat adjustment or temperature control systems. |
Pouring & Shaping | Molten material is poured into molds; tiltable designs ensure efficiency. |
Applications | Used in foundries for metals like brass, bronze, and aluminum. |
Safety Features | Refractory linings, tiltable designs, and flue gas venting for safety. |
Ready to find the perfect crucible furnace for your needs? Contact us today for expert advice!