A high-frequency induction heater works by utilizing electromagnetic induction and the Joule heating effect to generate heat in conductive materials. When an alternating current (AC) is passed through an induction coil, it creates a rapidly changing magnetic field. If a conductive material is placed within this magnetic field, eddy currents are induced within the material. These eddy currents encounter resistance as they flow through the material, generating heat due to the Joule effect. The process is non-contact, efficient, and allows for precise heating of metals, making it ideal for applications like metal hardening, melting, and welding. The frequency of the alternating current determines the depth of heating, with higher frequencies providing more localized and rapid heating.
Key Points Explained:
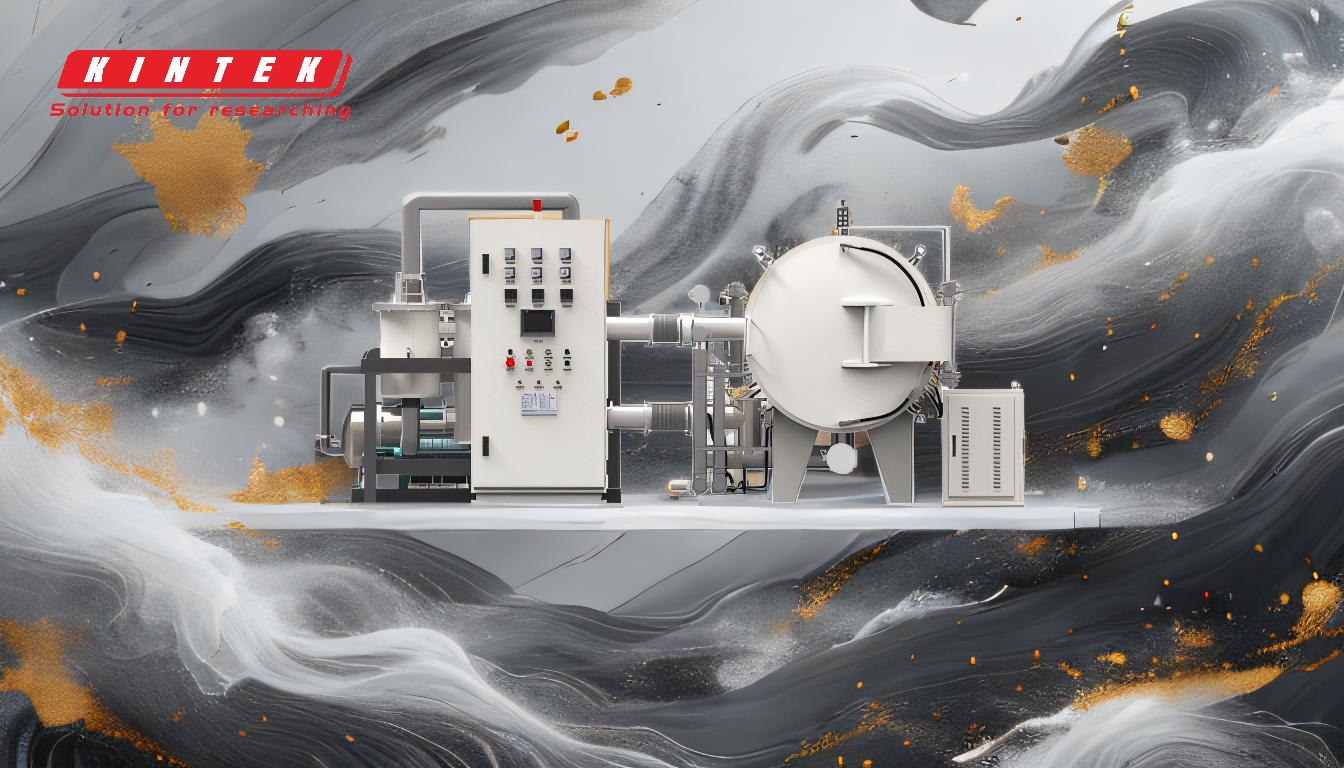
-
Electromagnetic Induction:
- When an alternating current flows through an induction coil, it generates a rapidly changing magnetic field around the coil.
- This magnetic field induces eddy currents in any nearby conductive material placed within the field.
- The strength and frequency of the magnetic field directly influence the magnitude and distribution of the induced currents.
-
Eddy Currents and Joule Heating:
- Eddy currents are circular electric currents induced within the conductive material due to the changing magnetic field.
- As these currents flow through the material, they encounter resistance, which converts electrical energy into heat (Joule heating).
- The heat generated is proportional to the square of the current and the material's electrical resistance.
-
Non-Contact Heating:
- Induction heating is a non-contact process, meaning the heat is generated directly within the material without physical contact between the heating element and the workpiece.
- This eliminates contamination and allows for precise, localized heating, making it ideal for applications requiring high purity or specific heat zones.
-
Frequency and Heating Depth:
- The frequency of the alternating current determines the depth of heating. Higher frequencies result in shallower heating (skin effect), while lower frequencies penetrate deeper into the material.
- High-frequency induction heaters (typically 10 kHz to several MHz) are used for surface heating, hardening, or small-scale applications, while lower frequencies are suitable for bulk heating or melting.
-
Applications of High-Frequency Induction Heating:
- Surface Hardening: Used to harden the surface of metal components while keeping the core soft and ductile.
- Melting and Casting: Ideal for melting metals in induction furnaces due to precise temperature control and efficiency.
- Welding and Brazing: Provides localized heating for joining metals without affecting surrounding areas.
- Annealing and Tempering: Used to alter the mechanical properties of metals by controlled heating and cooling.
-
Advantages of Induction Heating:
- Efficiency: Energy is directly transferred to the material, minimizing losses.
- Precision: Allows for localized and controlled heating.
- Speed: Rapid heating due to high-frequency operation.
- Cleanliness: Non-contact process reduces contamination risks.
- Automation-Friendly: Easily integrated into automated systems for consistent results.
-
Components of an Induction Heater:
- Power Supply: Converts standard AC power to high-frequency AC.
- Induction Coil: Generates the alternating magnetic field and is designed based on the application.
- Workpiece: The conductive material to be heated, placed within the magnetic field.
- Cooling System: Prevents overheating of the induction coil and power supply.
-
Physical Principles:
- Maxwell’s Equations: Describe how changing magnetic fields induce electric currents in conductive materials.
- Skin Effect: At high frequencies, eddy currents are concentrated near the surface of the material, limiting penetration depth.
- Hysteresis Losses: In magnetic materials, additional heat is generated due to the reversal of magnetic domains.
By combining these principles, high-frequency induction heaters provide a versatile and efficient method for heating conductive materials in a wide range of industrial and manufacturing applications.
Summary Table:
Key Aspect | Description |
---|---|
Electromagnetic Induction | Alternating current creates a magnetic field, inducing eddy currents in materials. |
Joule Heating | Eddy currents generate heat as they flow through conductive materials. |
Non-Contact Heating | Heat is generated within the material without physical contact. |
Frequency & Heating Depth | Higher frequencies provide shallow, localized heating; lower frequencies penetrate deeper. |
Applications | Metal hardening, melting, welding, annealing, and tempering. |
Advantages | Efficiency, precision, speed, cleanliness, and automation-friendly. |
Discover how high-frequency induction heaters can transform your industrial processes—contact us today for expert advice!