Pressure plays a critical role in the pyrolysis process, influencing the yield, composition, and properties of the resulting products (bio-oil, char, and pyrolytic gas). While temperature and residence time are often highlighted as primary factors, pressure can alter reaction kinetics, product distribution, and the efficiency of the process. Higher pressures can suppress the release of volatile compounds, leading to increased char formation, while lower pressures favor the production of gases and liquids. The interplay between pressure and other variables, such as temperature and feedstock properties, determines the overall efficiency and environmental impact of pyrolysis.
Key Points Explained:
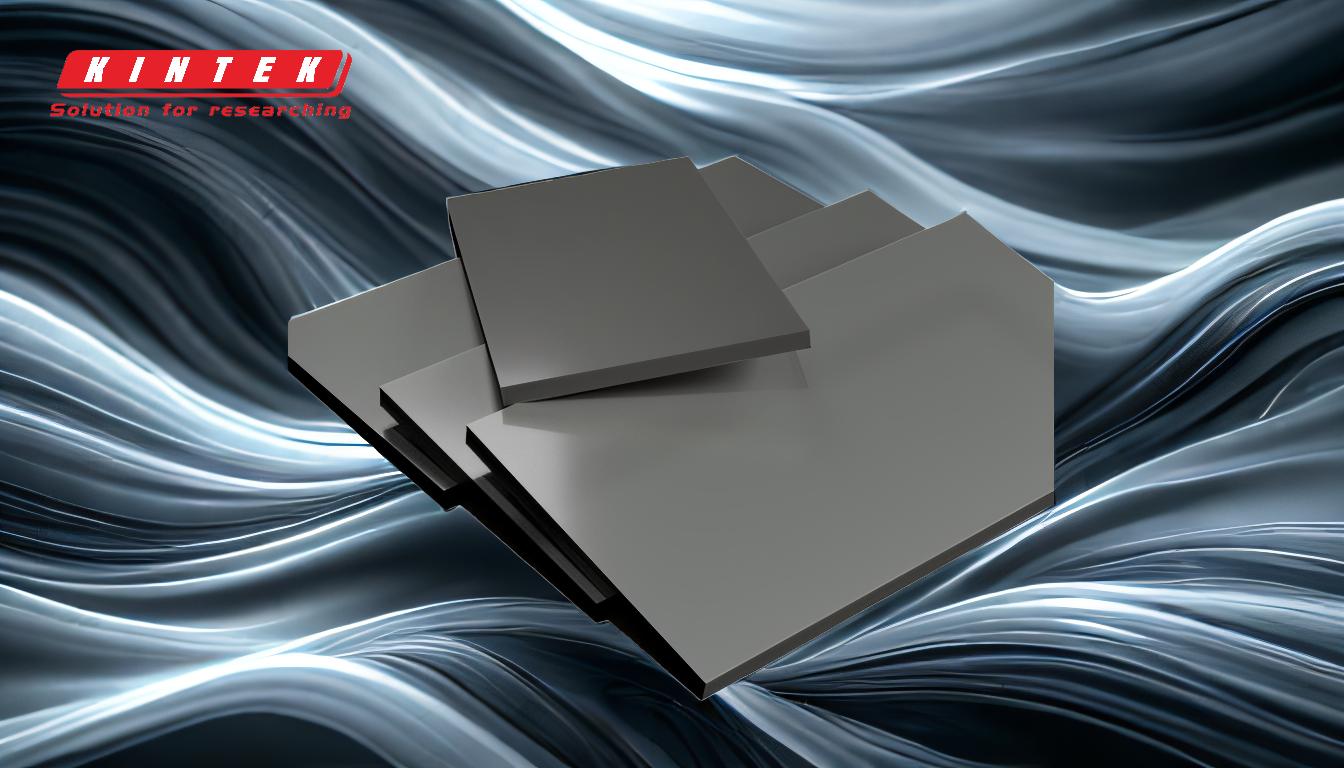
-
Impact on Product Distribution:
- Higher Pressure: Increases the formation of solid char due to the suppression of volatile compound release. This is because high pressure restricts the escape of gases, allowing more time for secondary reactions that promote char formation.
- Lower Pressure: Favors the production of gases and liquids (bio-oil) by facilitating the rapid release of volatile compounds from the feedstock. This is particularly beneficial for processes aiming to maximize bio-oil yield.
- Example: In biomass pyrolysis, lower pressures are often used to enhance bio-oil production, while higher pressures are employed in processes like carbonization to maximize char yield.
-
Reaction Kinetics and Efficiency:
- Pressure influences the rate of thermal decomposition and the extent of secondary reactions. Higher pressures can slow down the release of volatiles, leading to more complete thermal degradation and potentially higher energy efficiency.
- Lower pressures, on the other hand, can accelerate the pyrolysis process by reducing the resistance to volatile release, which may result in shorter residence times and faster processing.
-
Effect on Gas Composition:
- Non-Condensable Gases: Higher pressures tend to increase the production of non-condensable gases (e.g., methane, hydrogen, and carbon monoxide) due to enhanced cracking of heavier hydrocarbons.
- Condensable Gases: Lower pressures favor the formation of condensable gases, which can be condensed into bio-oil.
- Example: In tire pyrolysis, higher pressures can lead to increased gas yields, while lower pressures are better suited for maximizing liquid product recovery.
-
Influence on Feedstock Properties:
- The physical structure and particle size of the feedstock interact with pressure to affect the pyrolysis process. Smaller particle sizes, combined with optimal pressure conditions, can lead to more uniform heating and faster decomposition.
- Example: Shredded tires, which have smaller particle sizes, decompose more efficiently under lower pressures, yielding higher quantities of pyrolysis oil.
-
Environmental and Economic Considerations:
- Pressure control can influence the energy requirements and greenhouse gas (GHG) emissions of the pyrolysis process. Higher pressures may require more energy input but can also enhance the recovery of valuable byproducts like syngas.
- Lower pressures reduce energy consumption but may require additional post-processing steps to upgrade the bio-oil.
-
Synergy with Other Process Variables:
- Pressure interacts with temperature, residence time, and heating rate to determine the overall outcome of pyrolysis. For instance, higher temperatures combined with lower pressures can maximize gas yields, while moderate temperatures and higher pressures are better for char production.
- Example: In biomass pyrolysis, a combination of moderate pressure and high temperature is often used to optimize the balance between bio-oil and char yields.
-
Practical Applications and Optimization:
- Industrial pyrolysis systems are designed to operate at specific pressures tailored to the desired product slate. For example, fast pyrolysis for bio-oil production typically operates at near-atmospheric pressure, while slow pyrolysis for char production may use higher pressures.
- Optimization involves balancing pressure with other factors like feedstock type, reactor design, and economic considerations to achieve the desired product quality and yield.
By understanding how pressure affects pyrolysis, operators can fine-tune process conditions to achieve specific goals, whether maximizing bio-oil yield, enhancing char production, or optimizing energy efficiency. This knowledge is particularly valuable for purchasers of pyrolysis equipment, as it informs decisions about reactor design, operating parameters, and feedstock selection.
Summary Table:
Aspect | Higher Pressure | Lower Pressure |
---|---|---|
Product Distribution | Increases char formation by suppressing volatile release. | Favors bio-oil and gas production by facilitating volatile release. |
Reaction Kinetics | Slows volatile release, enhancing secondary reactions and energy efficiency. | Accelerates pyrolysis, reducing residence time and speeding up processing. |
Gas Composition | Increases non-condensable gases (e.g., methane, hydrogen). | Favors condensable gases, which can be converted into bio-oil. |
Feedstock Properties | Smaller particle sizes with optimal pressure improve heating uniformity. | Shredded tires decompose efficiently under lower pressure, yielding more oil. |
Environmental Impact | Higher energy input but enhances syngas recovery. | Reduces energy consumption but may require bio-oil upgrading. |
Synergy with Variables | Combines with temperature and residence time to optimize product yields. | Lower pressure with high temperature maximizes gas yields. |
Ready to optimize your pyrolysis process? Contact our experts today for tailored solutions!