Temperature plays a critical role in deposition processes, influencing both the rate and quality of film formation. While substrate temperature may not significantly affect the deposition rate, it profoundly impacts the film's density and structural integrity. Higher temperatures generally lead to denser films, but the specific temperature range must be carefully controlled to avoid adverse effects such as contamination or graphitization. The process temperature must also align with the application's requirements, as certain materials and techniques, like chemical vapor deposition (CVD) of diamond films, demand precise temperature conditions to ensure optimal results.
Key Points Explained:
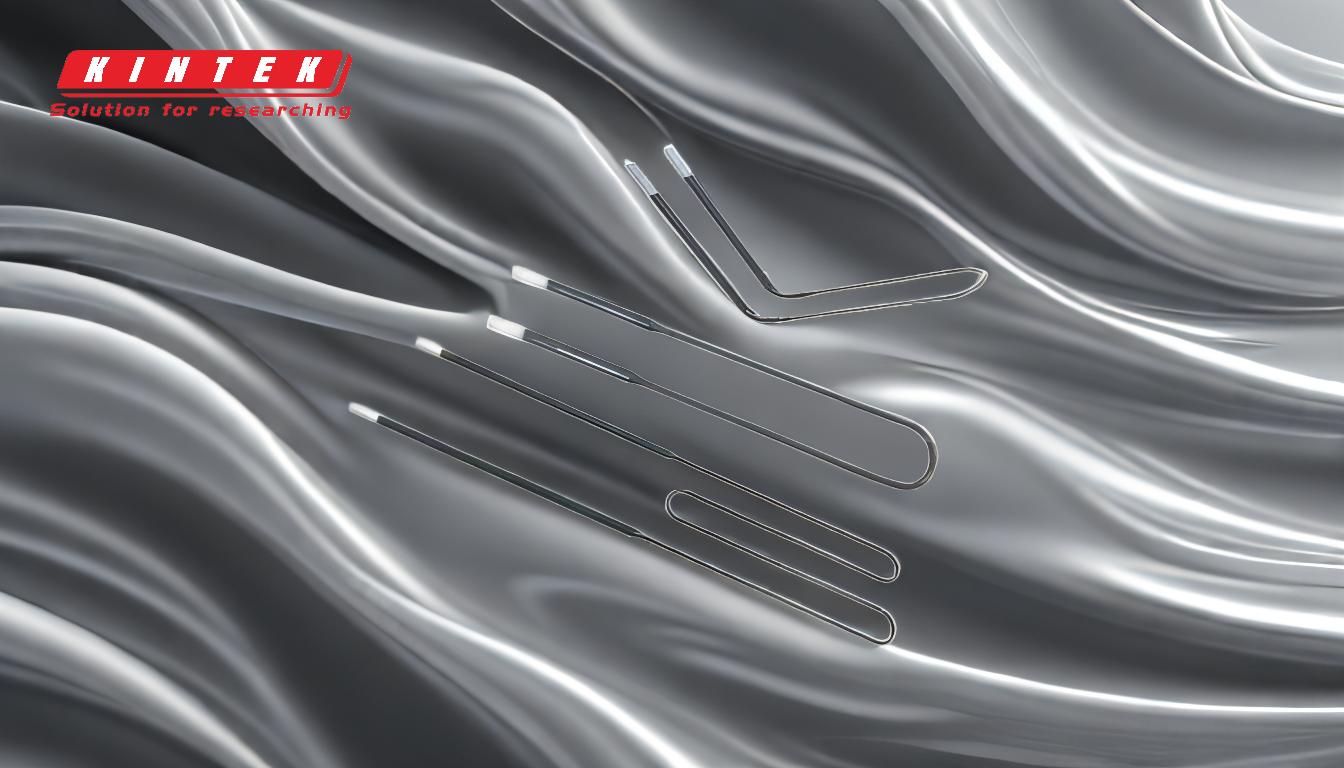
-
Impact of Temperature on Deposition Rate
- Substrate temperature has minimal influence on the deposition rate. This means that whether the substrate is heated or not, the rate at which material is deposited remains relatively constant.
- However, the quality of the deposited film is highly sensitive to temperature. Higher temperatures often result in denser and more uniform films, which are desirable for many applications.
-
Effect of Temperature on Film Quality
- Higher temperatures during deposition lead to denser films. This is because increased thermal energy allows atoms to rearrange more efficiently, reducing voids and defects in the film structure.
- In processes like chemical vapor deposition (CVD), temperature is critical for activating gas-phase reactions. For example, in diamond film deposition, the tungsten wire must be heated to 2000–2200°C to dissociate hydrogen and hydrocarbon groups, which are essential for diamond formation.
-
Temperature Limits in Deposition Processes
- Each deposition process has an optimal temperature range. Exceeding this range can lead to undesirable outcomes. For instance, in diamond CVD, if the substrate temperature exceeds 1200°C, graphitization occurs, degrading the diamond film.
- Similarly, if the temperature is too low, the dissociation of hydrogen and hydrocarbons may be insufficient, hindering diamond film formation.
-
Application-Specific Temperature Constraints
- The application of the deposited film often imposes temperature limits. For example, high-temperature processes may not be suitable for substrates that are sensitive to heat or for applications requiring low thermal stress.
- In diamond CVD, the substrate temperature is controlled by a combination of tungsten wire radiation and cooling water to maintain it below 1200°C, ensuring the formation of high-quality diamond films without contamination.
-
Balancing Temperature for Optimal Results
- Achieving the right balance of temperature is crucial. Too high a temperature can lead to issues like matrix contamination (e.g., tungsten carbide volatilization in diamond CVD), while too low a temperature can result in incomplete reactions and poor film quality.
- Process optimization involves fine-tuning the temperature to match the specific requirements of the material being deposited and the intended application.
In summary, while temperature may not drastically alter the deposition rate, it is a pivotal factor in determining the quality, density, and structural integrity of the deposited film. Precise temperature control is essential to avoid defects, contamination, or unwanted chemical reactions, ensuring the film meets the desired performance criteria.
Summary Table:
Aspect | Impact of Temperature |
---|---|
Deposition Rate | Minimal influence; rate remains relatively constant regardless of substrate temperature. |
Film Quality | Higher temperatures lead to denser, more uniform films with fewer defects. |
Temperature Limits | Exceeding optimal ranges can cause graphitization or incomplete reactions. |
Application-Specific Constraints | Temperature must align with substrate sensitivity and application requirements. |
Balancing Temperature | Crucial for avoiding contamination, defects, and ensuring optimal film performance. |
Need help optimizing your deposition process? Contact our experts today for tailored solutions!