An electric arc furnace (EAF) is a high-temperature industrial furnace used for melting metal, primarily scrap steel, by generating an electric arc between electrodes and the metal charge. The process involves charging the furnace with scrap metal, preheating it, and using high-voltage electric arcs to melt the metal. The furnace is equipped with a tilting mechanism for pouring molten metal and a fume extraction system for safety. The process includes stages like meltdown, refining, and slag formation, with additives like burnt lime and spar used to enhance efficiency. The furnace operates on three-phase electric current, utilizing graphite electrodes to create the arc and generate the heat necessary for melting.
Key Points Explained:
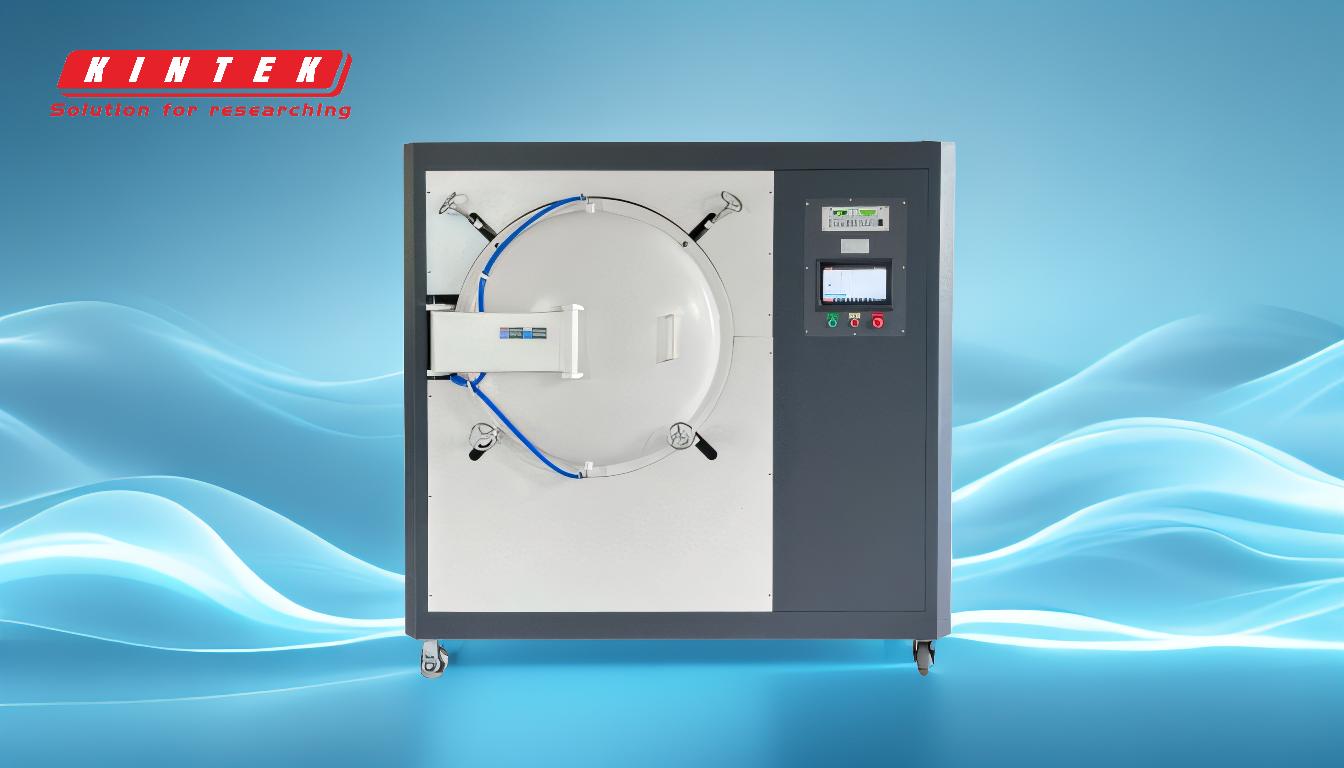
-
Basic Working Principle:
- The electric arc furnace uses an electric arc to generate intense heat, which melts the metal charge.
- The arc is formed between graphite electrodes and the metal scrap, creating temperatures high enough to melt the metal.
-
Components of the Furnace:
- Roof: Contains holes for electrode insertion and is made of refractory materials like alumina and magnesite-chromite bricks.
- Hearth: Holds the molten metal and slag, often water-cooled to withstand high temperatures.
- Electrodes: Typically made of graphite, these are the primary components that create the electric arc.
- Tilting Mechanism: Allows the furnace to pour molten metal into molds or ladles.
- Fume Extraction System: Ensures operator safety by removing harmful gases and particulates.
-
Operation Stages:
- Charging: Scrap metal is loaded into the furnace using a large basket. The roof swings open to allow charging.
- Meltdown: Electrodes are lowered onto the scrap, and an electric arc is struck. The voltage is increased to accelerate melting.
- Refining: Additives like burnt lime and spar are introduced to form slag, which helps remove impurities.
- Tapping: The furnace is tilted to pour the molten metal into a ladle or mold.
-
Energy Source:
- The furnace operates on three-phase electric current, which is supplied via copper busbars.
- The electric arc generates the heat needed for melting, making the process highly energy-efficient compared to traditional blast furnaces.
-
Material Handling:
- Both heavy and light scrap metal can be used as the charge.
- Preheating the scrap with exhaust gas improves energy efficiency.
- The use of additives like burnt lime and spar speeds up slag formation and improves the quality of the molten metal.
-
Safety and Environmental Considerations:
- The fume extraction system is crucial for maintaining a safe working environment by removing harmful fumes and particulates.
- The furnace is designed to operate at slightly positive pressure to prevent the ingress of contaminants.
-
Advantages of Electric Arc Furnaces:
- Flexibility: Capable of melting a wide range of scrap metals.
- Efficiency: High energy efficiency due to the direct heating method.
- Environmental Impact: Lower carbon footprint compared to traditional blast furnaces, especially when powered by renewable energy sources.
By understanding these key points, one can appreciate the complexity and efficiency of electric arc furnaces in modern metallurgical processes. The design and operation of these furnaces are optimized for high productivity, safety, and environmental sustainability.
Summary Table:
Aspect | Details |
---|---|
Working Principle | Uses electric arcs between graphite electrodes and metal to generate heat. |
Key Components | Roof, hearth, electrodes, tilting mechanism, fume extraction system. |
Operation Stages | Charging, meltdown, refining, tapping. |
Energy Source | Three-phase electric current supplied via copper busbars. |
Material Handling | Handles heavy and light scrap, preheating, and additives for efficiency. |
Safety & Environment | Fume extraction system, positive pressure design for safety. |
Advantages | Flexibility, high energy efficiency, lower carbon footprint. |
Ready to optimize your metal melting process? Contact our experts today to learn more about electric arc furnaces!