Film thickness in an evaporation system is controlled through a combination of precise adjustments to the evaporation process and monitoring techniques. Key factors include the temperature of the evaporant, the deposition rate, the distance between the evaporant and the substrate, and the use of quartz crystal microbalances (QCMs) for real-time thickness measurement. Additionally, environmental conditions such as vacuum pressure, substrate temperature, and surface preparation play a significant role in ensuring uniformity and quality. By carefully managing these parameters, the system can achieve consistent and accurate film thicknesses tailored to specific requirements.
Key Points Explained:
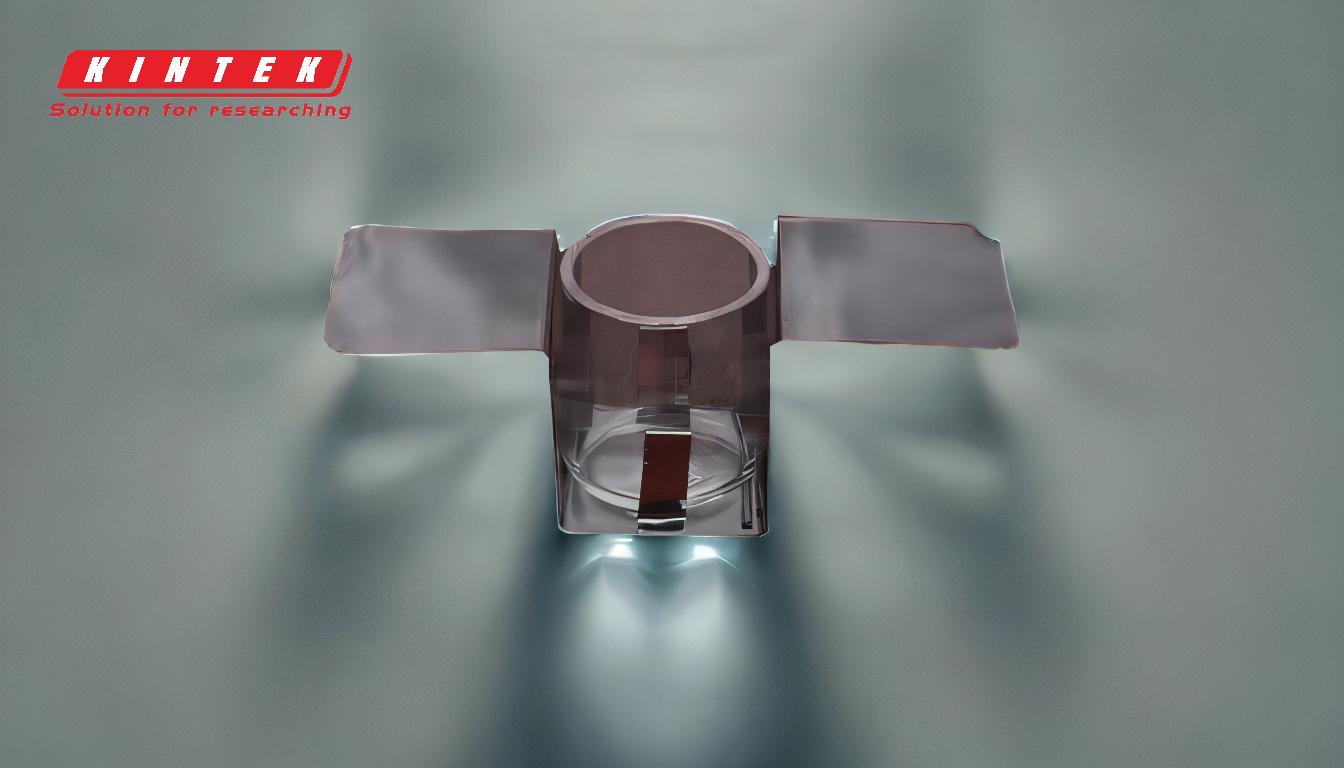
-
Control of Evaporant Temperature:
- The temperature of the evaporant directly influences the rate at which material is vaporized. Higher temperatures increase the evaporation rate, while lower temperatures slow it down.
- Precise control of the evaporant temperature ensures a consistent deposition rate, which is critical for achieving the desired film thickness.
-
Deposition Rate Adjustment:
- The deposition rate, or the rate at which material is deposited onto the substrate, is a key factor in controlling film thickness.
- By adjusting the deposition rate, operators can control how quickly or slowly the film grows, allowing for fine-tuning of the final thickness.
-
Distance Between Evaporant and Substrate:
- The distance between the evaporant source and the substrate affects the uniformity and thickness of the deposited film.
- A shorter distance typically results in a higher deposition rate and thicker films, while a longer distance can lead to more uniform but thinner films.
-
Use of Quartz Crystal Microbalances (QCMs):
- QCMs are widely used in evaporation systems to measure and regulate film thickness in real-time.
- These devices provide accurate feedback on the deposition rate and thickness, allowing for immediate adjustments to maintain precise control over the process.
-
Influence of Vacuum Pressure:
- The pressure inside the vacuum chamber plays a crucial role in the quality and uniformity of the film.
- Higher vacuum levels reduce the presence of residual gases, minimizing collisions that can lead to non-uniform thickness and impurities in the film.
-
Substrate Temperature and Surface Preparation:
- Heating the substrate improves the mobility of deposited atoms, promoting better adhesion and uniformity.
- Proper surface preparation, such as cleaning and smoothing, ensures that the substrate is free from contaminants and irregularities that could affect film quality.
-
Substrate Holder Rotation:
- Rotating the substrate holder during deposition can enhance the uniformity of the film thickness by ensuring even exposure to the evaporant.
- This is particularly important for substrates with complex geometries or when depositing over large areas.
-
Source Material Purity and Properties:
- The purity and molecular weight of the source material influence the evaporation rate and the quality of the deposited film.
- High-purity materials are essential for producing films with consistent properties and minimal defects.
By integrating these factors and leveraging advanced monitoring and control technologies, evaporation systems can achieve precise and repeatable control over film thickness, ensuring high-quality results for a wide range of applications.
Summary Table:
Factor | Role in Film Thickness Control |
---|---|
Evaporant Temperature | Controls evaporation rate; higher temps increase rate, lower temps slow it down. |
Deposition Rate | Adjusts how quickly or slowly the film grows, enabling fine-tuning of thickness. |
Evaporant-Substrate Distance | Affects uniformity and thickness; shorter distance = thicker films, longer = more uniform films. |
Quartz Crystal Microbalances | Provides real-time thickness measurement and feedback for precise control. |
Vacuum Pressure | Higher vacuum reduces residual gases, improving film uniformity and quality. |
Substrate Temperature | Enhances atom mobility, promoting better adhesion and uniformity. |
Surface Preparation | Ensures a clean, smooth substrate for high-quality film deposition. |
Substrate Holder Rotation | Improves uniformity by ensuring even exposure to the evaporant. |
Source Material Purity | High-purity materials ensure consistent film properties and minimal defects. |
Need precise control over film thickness in your evaporation system? Contact our experts today for tailored solutions!