Thin film coating is a process used to deposit thin layers of material onto a substrate, typically ranging from a few nanometers to several micrometers in thickness. This process is essential in various industries, including electronics, optics, and energy, due to its ability to precisely control the thickness, composition, and properties of the films. The primary methods for thin film deposition include Physical Vapor Deposition (PVD), Chemical Vapor Deposition (CVD), Atomic Layer Deposition (ALD), and Spray Pyrolysis. Each method has its own advantages and is chosen based on the specific requirements of the application, such as the type of material, the desired film properties, and the scale of production.
Key Points Explained:
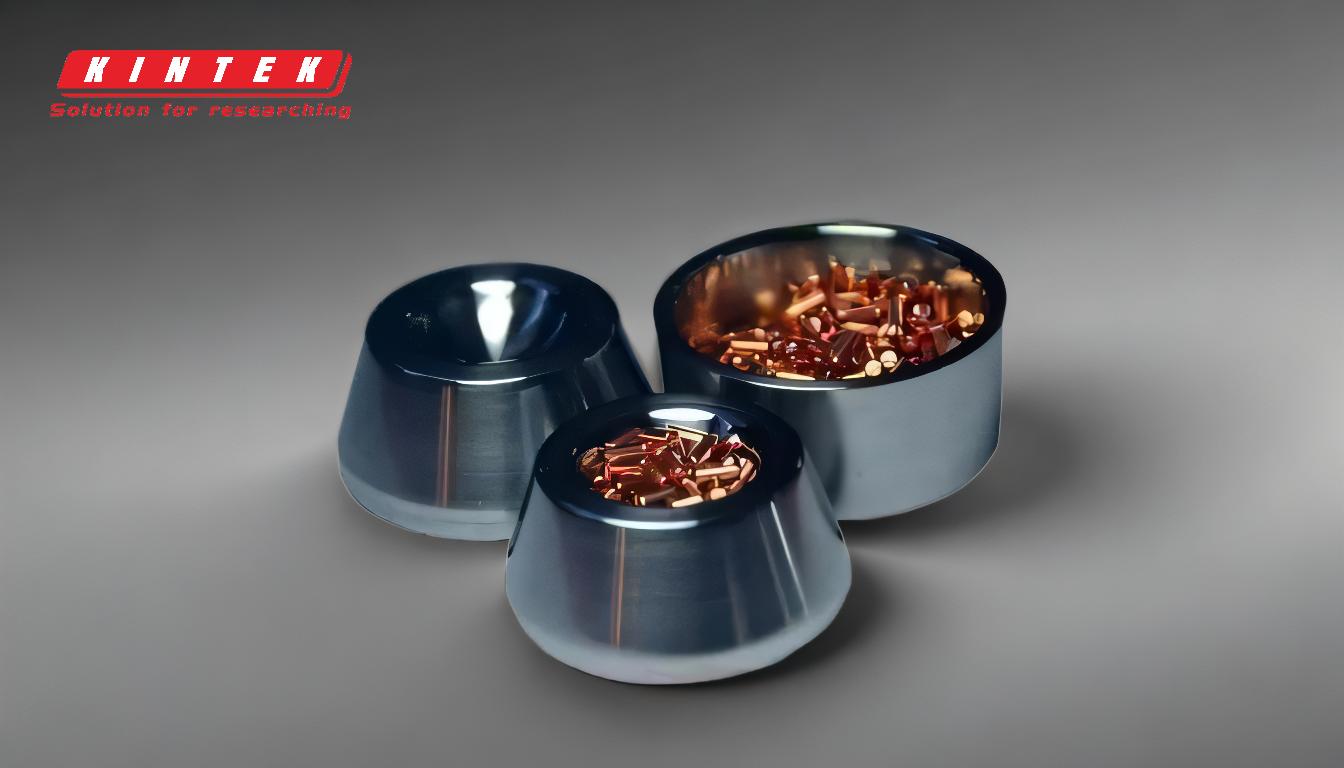
-
Physical Vapor Deposition (PVD):
- Process Overview: PVD involves the physical transfer of material from a source to a substrate. This is typically done through evaporation or sputtering.
- Evaporation: In this method, the source material is heated until it evaporates, and the vapor then condenses on the substrate to form a thin film. This technique is often used for metals and simple compounds.
- Sputtering: In sputtering, high-energy particles (usually ions) bombard the source material, causing atoms to be ejected and deposited onto the substrate. This method is versatile and can be used for a wide range of materials, including metals, alloys, and ceramics.
- Applications: PVD is commonly used in the production of thin films for semiconductors, optical coatings, and decorative finishes.
-
Chemical Vapor Deposition (CVD):
- Process Overview: CVD involves the use of chemical reactions to deposit a thin film on a substrate. The process typically occurs in a reaction chamber where the substrate is exposed to volatile precursors that react or decompose on the substrate surface.
- Types of CVD: There are several variations of CVD, including low-pressure CVD (LPCVD), plasma-enhanced CVD (PECVD), and metal-organic CVD (MOCVD). Each variation offers different advantages in terms of deposition rate, film quality, and temperature requirements.
- Applications: CVD is widely used in the semiconductor industry for depositing silicon dioxide, silicon nitride, and other materials. It is also used in the production of coatings for cutting tools and in the fabrication of optical fibers.
-
Atomic Layer Deposition (ALD):
- Process Overview: ALD is a specialized form of CVD that deposits thin films one atomic layer at a time. The process involves alternating exposure of the substrate to two or more precursors, with each exposure resulting in a single atomic layer of material.
- Advantages: ALD offers exceptional control over film thickness and uniformity, making it ideal for applications requiring precise thin films, such as in microelectronics and nanotechnology.
- Applications: ALD is used in the production of high-k dielectrics for transistors, barrier layers in integrated circuits, and protective coatings for various devices.
-
Spray Pyrolysis:
- Process Overview: Spray Pyrolysis involves spraying a solution containing the desired material onto a heated substrate. The solvent evaporates, and the remaining material decomposes to form a thin film.
- Advantages: This method is relatively simple and can be used to deposit a wide range of materials, including oxides, sulfides, and nitrides.
- Applications: Spray Pyrolysis is used in the production of thin films for solar cells, sensors, and transparent conductive coatings.
-
Other Deposition Techniques:
- Spin Coating: This technique involves applying a liquid solution to a substrate, which is then spun at high speed to spread the solution into a thin, uniform layer. After spinning, the solvent evaporates, leaving behind a solid thin film. Spin coating is commonly used in the production of photoresists and organic electronics.
- Electroplating: In this method, a thin film is deposited onto a conductive substrate by passing an electric current through a solution containing the desired metal ions. Electroplating is widely used for decorative and protective coatings.
-
Equipment and Systems:
- Batch Systems: These systems process multiple wafers or substrates simultaneously in a single chamber. They are suitable for high-volume production.
- Cluster Tools: These systems use multiple chambers for different processes, allowing for sequential deposition steps without exposing the substrate to the environment. They are ideal for complex, multi-layer thin films.
- Factory Systems: Large-scale systems designed for high-volume production, often used in semiconductor manufacturing.
- Laboratory Systems: Smaller, bench-top systems used for low-volume, experimental applications. These systems are ideal for research and development.
In conclusion, thin film coating is a versatile and essential process in modern technology, with a variety of methods available to suit different materials and applications. The choice of deposition technique depends on factors such as the desired film properties, the type of substrate, and the scale of production. Each method offers unique advantages, allowing for precise control over the thickness, composition, and properties of the thin films.
Summary Table:
Method | Process Overview | Applications |
---|---|---|
Physical Vapor Deposition (PVD) | Material transfer via evaporation or sputtering. | Semiconductors, optical coatings, decorative finishes. |
Chemical Vapor Deposition (CVD) | Chemical reactions deposit films on substrates. | Semiconductors, cutting tools, optical fibers. |
Atomic Layer Deposition (ALD) | Precise atomic layer-by-layer deposition. | High-k dielectrics, barrier layers, protective coatings. |
Spray Pyrolysis | Spraying solution onto heated substrate, followed by decomposition. | Solar cells, sensors, transparent conductive coatings. |
Spin Coating | Spinning substrate to spread liquid solution into a thin film. | Photoresists, organic electronics. |
Electroplating | Deposition via electric current in a solution containing metal ions. | Decorative and protective coatings. |
Discover the perfect thin film coating solution for your needs—contact our experts today!